Debinding in 3D printing is a critical post-processing step that involves removing binding agents or carrier materials from a 3D-printed part before sintering. These binding agents, which are essential during the printing process to hold the powder particles together, become unnecessary and even problematic during sintering. Debinding can be achieved through thermal or chemical methods, depending on the type of binder used. The process ensures the part is free from impurities, prevents furnace contamination, and prepares the part for sintering. It requires careful control of factors like temperature, pressure, and time to avoid defects such as warping or cracking. The duration of debinding can vary significantly, often taking up to 24-36 hours, depending on the part's geometry and the debinding method.
Key Points Explained:
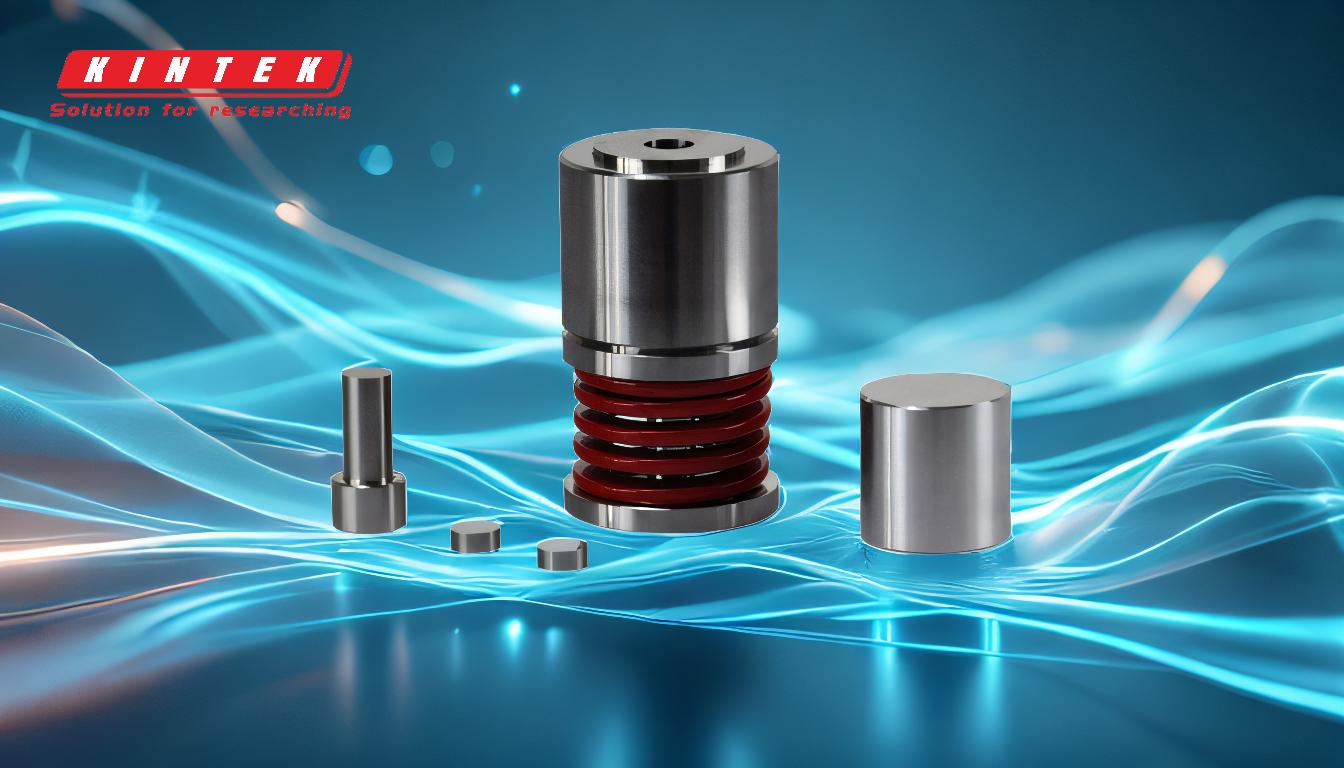
-
Definition and Purpose of Debinding:
- Debinding is the process of removing binding agents or carrier materials from 3D-printed parts.
- These binders are initially necessary to hold powder particles together during the printing process but must be removed before sintering to avoid contamination and defects in the final product.
- The primary goal is to ensure the part is clean, sturdy, and ready for the sintering process.
-
Methods of Debinding:
- Thermal Debinding: Involves heating the part in a furnace to evaporate or degrade the binder. This method relies on the binder's organic compounds having different melting points, which allows for controlled removal.
- Chemical Debinding: Uses a chemical bath to dissolve the binder. This method is often faster but requires careful handling of chemicals.
- The choice of method depends on the type of binder used and the material properties of the part.
-
Factors Influencing Debinding:
- Temperature Profile: The temperature must be carefully controlled to avoid defects like warping or cracking. For example, debinding for technical ceramics typically starts at room temperature and finishes at 600°C.
- Pressure and Gas Atmosphere: These factors help in the efficient removal of binders and prevent contamination.
- Part Geometry: Complex geometries may require longer debinding times, often up to 24-36 hours, to ensure complete binder removal.
-
Importance of Debinding:
- Prevents Contamination: Residual binders can contaminate the sintering furnace and the final product, leading to defects like blistering or pores.
- Improves Efficiency: Proper debinding makes the sintering process faster and more efficient by preventing furnace clogging.
- Ensures Part Integrity: Removing binders ensures the part is sturdy and free from impurities, which is critical for achieving the desired mechanical properties.
-
Challenges and Considerations:
- Defects: Improper debinding can lead to defects such as warping, cracking, or incomplete binder removal.
- Time-Consuming: The process can be lengthy, especially for parts with complex geometries.
- Equipment Requirements: Specialized equipment, such as debinding plants, is often required to handle the removal and condensation of binders safely.
-
Applications and Relevance:
- Debinding is essential in powder metallurgy and the manufacturing of technical ceramics, where binder removal is a prerequisite for sintering.
- It is a critical step in metal 3D printing, ensuring the final product meets quality and performance standards.
By understanding these key points, equipment and consumable purchasers can better appreciate the importance of debinding in 3D printing and make informed decisions about the materials and processes they choose.
Summary Table:
Aspect | Details |
---|---|
Definition | Removal of binding agents from 3D-printed parts before sintering. |
Purpose | Ensures parts are clean, sturdy, and free from impurities. |
Methods | Thermal (heating) or Chemical (dissolving binders). |
Key Factors | Temperature, pressure, gas atmosphere, and part geometry. |
Duration | Typically 24-36 hours, depending on part complexity. |
Importance | Prevents contamination, improves sintering efficiency, and ensures quality. |
Challenges | Risk of defects like warping, cracking, and long processing times. |
Applications | Essential for powder metallurgy, technical ceramics, and metal 3D printing. |
Ready to optimize your 3D printing process? Contact us today to learn more about debinding solutions!