Dental ceramics are a specialized category of materials used in dentistry for creating crowns, bridges, veneers, and other restorative dental applications. These materials are primarily composed of inorganic compounds, with a focus on achieving high strength, biocompatibility, and aesthetic properties. The primary components of dental ceramics include silica-based materials, alumina, zirconia, and glass ceramics. These materials are often classified as fine ceramics due to their precise composition and advanced manufacturing processes. Dental ceramics are engineered to mimic the natural appearance of teeth while providing durability and resistance to wear. The choice of materials depends on the specific dental application, with each type offering unique properties such as translucency, strength, and thermal stability.
Key Points Explained:
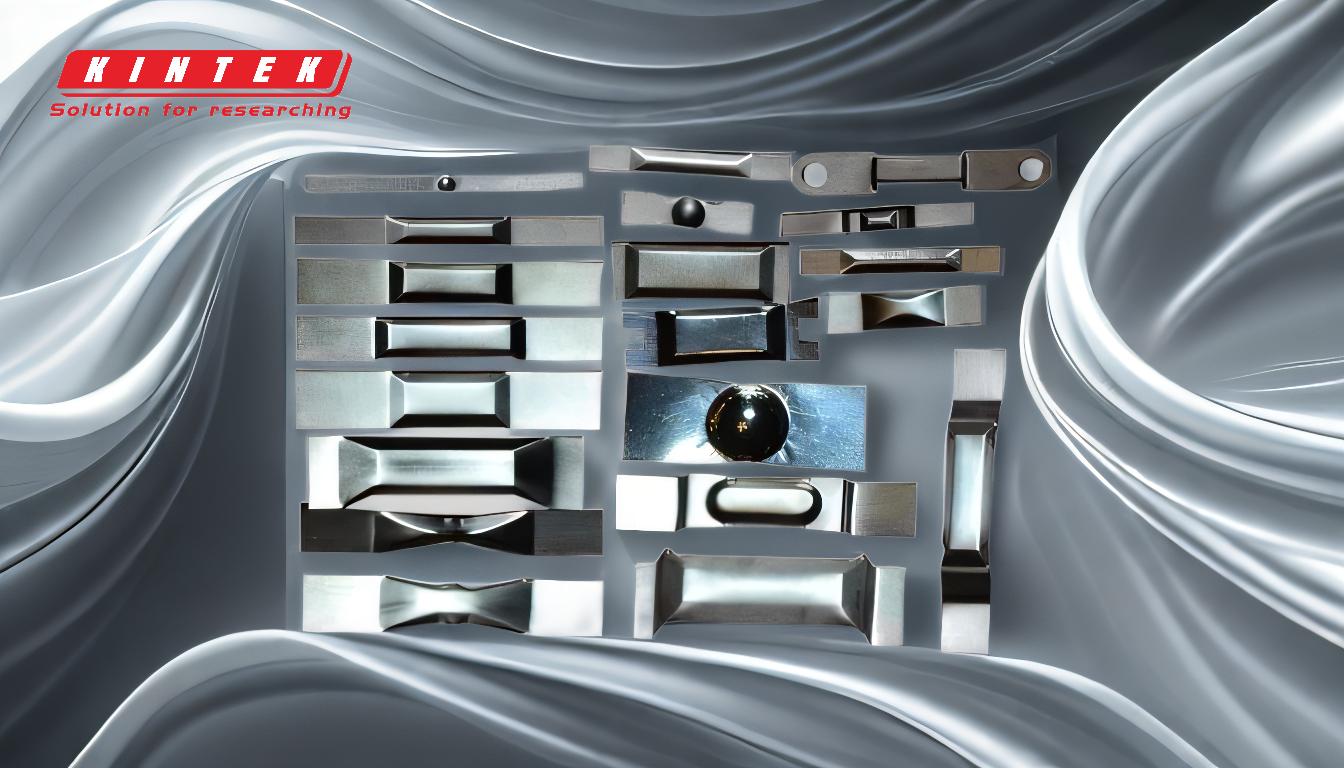
-
Primary Components of Dental Ceramics:
- Silica-Based Materials: Silica (SiO₂) is a fundamental component in many dental ceramics, often combined with other oxides to form glass ceramics. These materials are valued for their aesthetic properties and ability to replicate the natural translucency of teeth.
- Alumina (Al₂O₃): Alumina is used to enhance the strength and hardness of dental ceramics. It is often incorporated into materials designed for high-stress applications, such as crowns and bridges.
- Zirconia (ZrO₂): Zirconia is a high-strength ceramic material known for its exceptional durability and fracture resistance. It is widely used in dental restorations, particularly for posterior teeth, where mechanical strength is critical.
- Glass Ceramics: These are a combination of glass and crystalline phases, offering a balance of aesthetics and strength. They are commonly used for veneers and inlays.
-
Classification as Fine Ceramics:
- Dental ceramics fall under the category of fine ceramics, which are characterized by their high purity, precise composition, and advanced manufacturing techniques. Fine ceramics are engineered to meet specific performance requirements, such as biocompatibility, wear resistance, and thermal stability.
-
Properties of Dental Ceramics:
- Aesthetic Properties: Dental ceramics are designed to closely resemble natural teeth in terms of color, translucency, and texture. This is achieved through careful control of the material composition and processing techniques.
- Mechanical Strength: The strength of dental ceramics is critical for their performance in restorative applications. Materials like zirconia and alumina are chosen for their high fracture toughness and resistance to wear.
- Biocompatibility: Dental ceramics must be biocompatible, meaning they do not cause adverse reactions when in contact with oral tissues. This is a key consideration in their design and manufacturing.
-
Applications in Dentistry:
- Crowns and Bridges: Dental ceramics are commonly used to fabricate crowns and bridges, which restore the function and appearance of damaged or missing teeth. Zirconia and alumina-based ceramics are particularly suited for these applications due to their strength and durability.
- Veneers: Glass ceramics are often used for veneers, which are thin shells placed over the front surface of teeth to improve their appearance. These materials provide a natural look and are resistant to staining.
- Inlays and Onlays: These are indirect restorations used to repair teeth with moderate damage. Dental ceramics are ideal for these applications due to their precision fit and aesthetic qualities.
-
Manufacturing Processes:
- Sintering: Dental ceramics are typically sintered at high temperatures to achieve their final properties. This process involves heating the material to a point where the particles bond together, resulting in a dense and strong structure.
- CAD/CAM Technology: Computer-aided design and manufacturing (CAD/CAM) are widely used in the production of dental ceramics. This technology allows for precise customization of restorations to fit individual patients.
-
Advantages and Limitations:
- Advantages: Dental ceramics offer excellent aesthetic properties, biocompatibility, and durability. They are also resistant to wear and corrosion, making them suitable for long-term use in the oral environment.
- Limitations: Despite their many benefits, dental ceramics can be brittle and prone to fracture under certain conditions. Advances in material science are continually addressing these limitations to improve their performance.
In summary, dental ceramics are a versatile and essential material in modern dentistry, offering a combination of aesthetic appeal, strength, and biocompatibility. Their composition and properties make them ideal for a wide range of restorative applications, ensuring both functional and cosmetic benefits for patients.
Summary Table:
Component | Role in Dental Ceramics |
---|---|
Silica-Based Materials | Provides aesthetic properties and natural translucency, ideal for mimicking teeth. |
Alumina (Al₂O₃) | Enhances strength and hardness, suitable for high-stress applications like crowns and bridges. |
Zirconia (ZrO₂) | Offers exceptional durability and fracture resistance, commonly used for posterior teeth. |
Glass Ceramics | Combines aesthetics and strength, often used for veneers and inlays. |
Learn more about how dental ceramics can enhance your dental restorations—contact our experts today!