A deposition machine is a specialized piece of equipment used in various manufacturing and scientific processes to apply thin layers of material onto a substrate. This process is crucial in industries such as semiconductor manufacturing, optics, and surface engineering. The machine operates by creating a controlled environment, often involving a vacuum, where chemical or physical reactions deposit material onto the target surface. This results in a uniform and precise coating that enhances the substrate's properties, such as conductivity, durability, or resistance to environmental factors.
Key Points Explained:
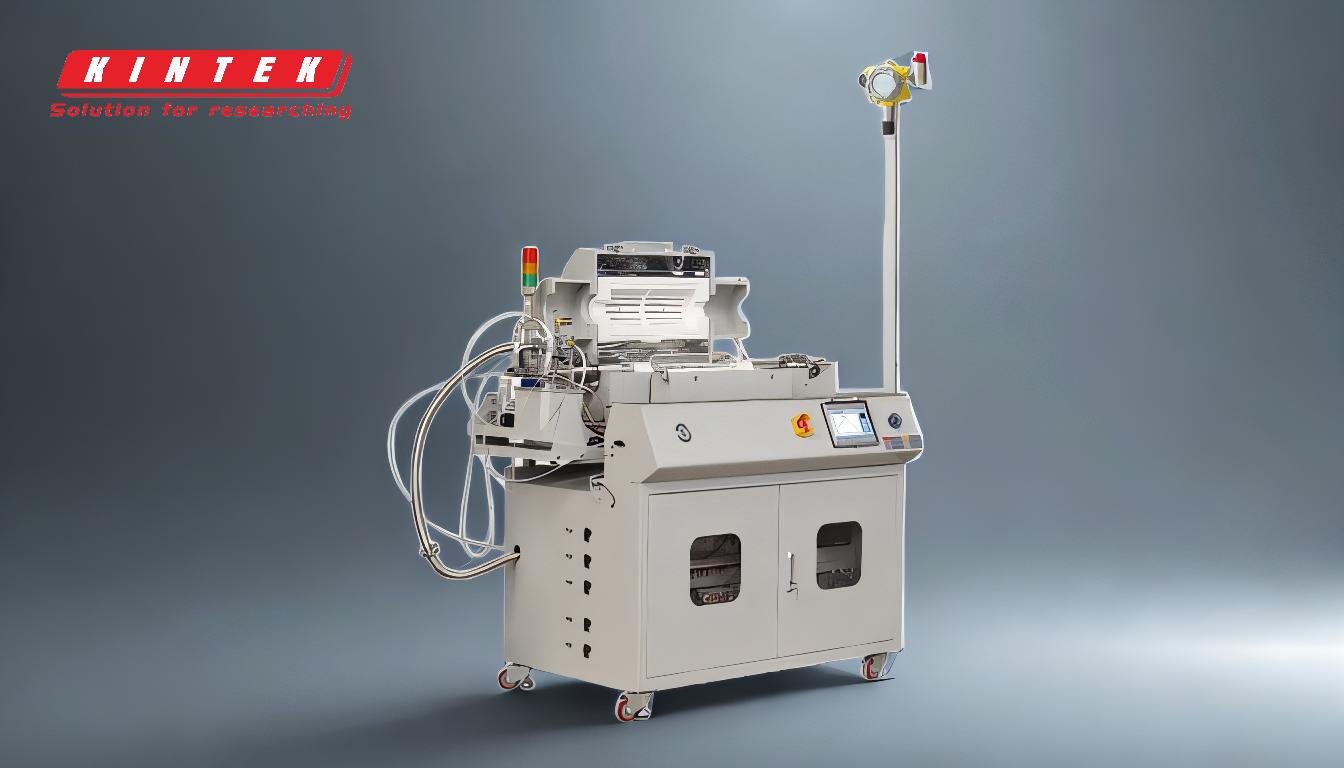
-
Purpose of a Deposition Machine:
- Thin Film Application: The primary function of a deposition machine is to apply thin films of material onto a substrate. These films can be as thin as a few nanometers and are used to modify the surface properties of the substrate.
- Enhanced Properties: The deposited layers can improve electrical conductivity, optical properties, corrosion resistance, and mechanical strength, depending on the material used.
-
Types of Deposition Processes:
- Chemical Vapor Deposition (CVD): In CVD, the substrate is exposed to volatile precursors that react or decompose on the substrate surface to produce the desired deposit. This process is often used in semiconductor manufacturing and can produce high-purity, high-performance solid materials.
- Physical Vapor Deposition (PVD): PVD involves the physical transfer of material from a source to the substrate. Techniques include sputtering, evaporation, and ion plating. PVD is commonly used for coating tools and components with wear-resistant layers.
-
Operating Environment:
- Vacuum Conditions: Many deposition processes, especially CVD and PVD, require a vacuum environment to ensure the purity and uniformity of the deposited layer. The vacuum helps to eliminate contaminants and allows for precise control over the deposition parameters.
- Controlled Atmosphere: The environment within the deposition chamber is carefully controlled in terms of temperature, pressure, and gas composition to achieve the desired film properties.
-
Components of a Deposition Machine:
- Reaction Chamber: The core component where the deposition process occurs. It is designed to maintain the necessary vacuum and temperature conditions.
- Gas Delivery System: Supplies the precursor gases or vapors to the reaction chamber. This system must be precise to ensure the correct chemical reactions take place.
- Substrate Holder: Holds the workpiece in place during the deposition process. It may include mechanisms for rotation or movement to ensure uniform coating.
- Vacuum System: Creates and maintains the vacuum within the reaction chamber. This system is critical for the success of the deposition process.
- Control System: Monitors and controls all parameters of the deposition process, including temperature, pressure, gas flow rates, and deposition time.
-
Applications of Deposition Machines:
- Semiconductor Industry: Used to deposit thin films of silicon, silicon dioxide, and other materials onto silicon wafers to create integrated circuits.
- Optical Coatings: Applied to lenses and mirrors to enhance their reflective or anti-reflective properties.
- Protective Coatings: Used to apply wear-resistant or corrosion-resistant coatings to tools and industrial components.
- Solar Cells: Deposition machines are used to create the thin film layers in photovoltaic cells, which convert sunlight into electricity.
-
Advantages of Using Deposition Machines:
- Precision and Control: Deposition machines offer high precision and control over the thickness and composition of the deposited layers, which is essential for applications requiring exact specifications.
- Versatility: They can deposit a wide range of materials, including metals, ceramics, and polymers, onto various substrates.
- Scalability: Deposition processes can be scaled up for industrial production, making them suitable for both small-scale research and large-scale manufacturing.
-
Challenges and Considerations:
- Cost: Deposition machines and the associated processes can be expensive, particularly for high-precision applications.
- Complexity: The operation and maintenance of deposition machines require specialized knowledge and skills.
- Material Limitations: Not all materials can be easily deposited using standard deposition techniques, which may require the development of new methods or modifications to existing ones.
In summary, a deposition machine is a critical tool in modern manufacturing and research, enabling the precise application of thin films to enhance the properties of various substrates. Its applications span multiple industries, and while it offers significant advantages, it also presents challenges that must be carefully managed.
Summary Table:
Key Aspect | Details |
---|---|
Purpose | Applies thin films to substrates to enhance properties like conductivity. |
Types of Processes | Chemical Vapor Deposition (CVD), Physical Vapor Deposition (PVD). |
Operating Environment | Vacuum or controlled atmosphere for purity and uniformity. |
Main Components | Reaction chamber, gas delivery system, substrate holder, vacuum system. |
Applications | Semiconductors, optical coatings, protective coatings, solar cells. |
Advantages | High precision, versatility, scalability. |
Challenges | High cost, complexity, material limitations. |
Learn how a deposition machine can elevate your manufacturing process—contact our experts today!