A drop tube furnace is a specialized type of tube furnace designed for high-temperature processes, particularly in research and industrial applications. It features a vertical orientation, allowing materials to be dropped or fed through the furnace tube, enabling rapid heating, cooling, or controlled thermal processing. The furnace typically consists of a cylindrical heating chamber with embedded heating coils, a thermally insulating matrix, and a precise temperature control system. Its vertical design facilitates gravity-assisted material movement, making it ideal for processes like pyrolysis, thermal decomposition, and materials testing. The drop tube furnace is widely used in fields such as materials science, chemistry, and energy research due to its ability to achieve uniform heating and controlled thermal gradients.
Key Points Explained:
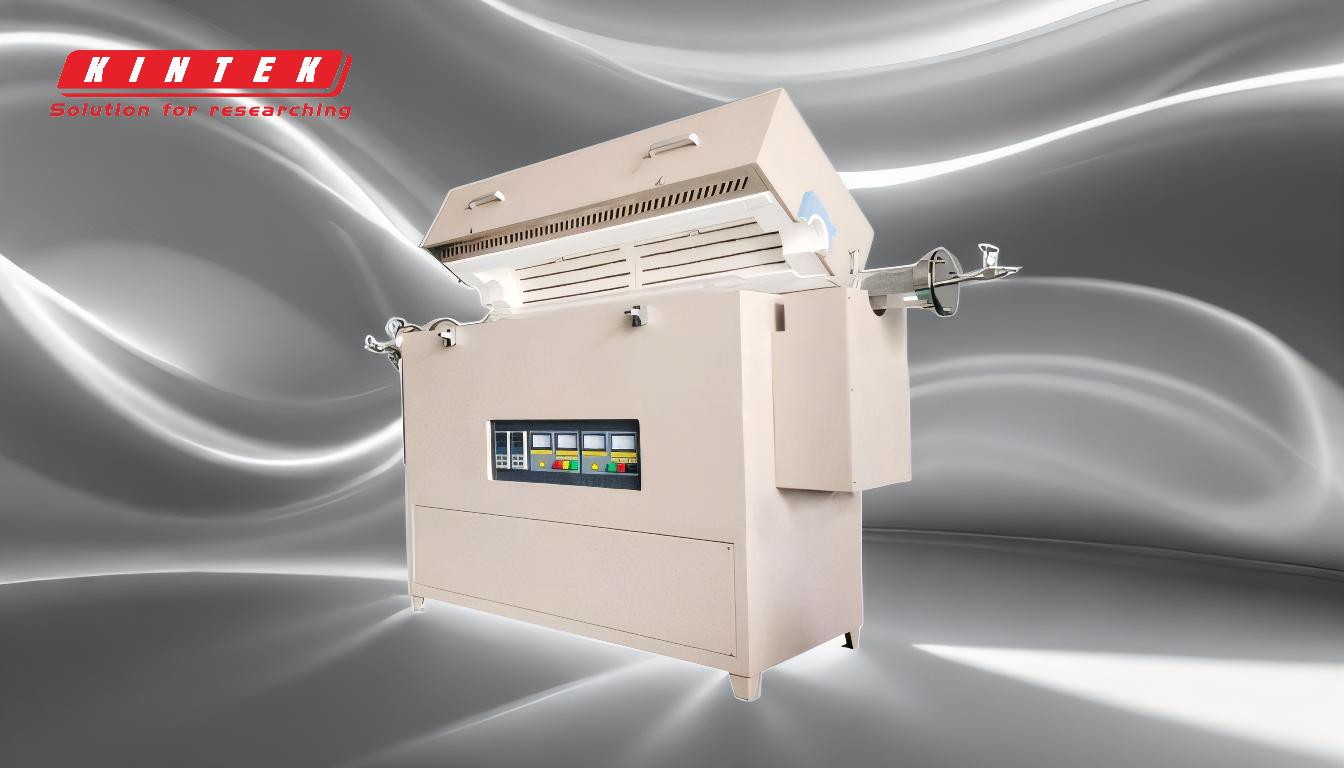
-
Definition and Purpose of a Drop Tube Furnace:
- A drop tube furnace is a vertical tube furnace designed for high-temperature applications where materials are dropped or fed through the furnace for rapid heating or cooling.
- It is commonly used in research and industrial processes such as pyrolysis, thermal decomposition, and materials testing.
-
Key Components:
- Heating Chamber: A cylindrical cavity made of high-temperature ceramics or refractory materials, surrounded by heating coils embedded in a thermally insulating matrix.
- Heating Elements: Typically include resistance wires, silicon carbon rods, or silicon molybdenum rods, which generate high temperatures.
- Thermocouple: Used for precise temperature control and feedback.
- Insulation Layer: Reduces energy loss and maintains high thermal efficiency.
- Outer Casing: Made of stainless steel or aluminum alloy for durability and corrosion resistance.
-
Vertical Orientation:
- The vertical design allows materials to be dropped or fed through the furnace tube, facilitating gravity-assisted movement and rapid thermal processing.
- This orientation is particularly useful for experiments requiring controlled heating or cooling rates.
-
Applications:
- Pyrolysis and Thermal Decomposition: Used to study the breakdown of materials at high temperatures in the absence of oxygen.
- Materials Testing: Ideal for testing the thermal properties of materials, such as ceramics, metals, and composites.
- Energy Research: Applied in the study of coal, biomass, and other fuels for energy production.
- Crystal Growth and Gradient Work: Suitable for processes requiring precise temperature gradients.
-
Advantages:
- Uniform Heating: The cylindrical design and multi-zone heating ensure high thermal uniformity.
- Controlled Temperature Gradients: Enables precise control over heating and cooling rates.
- Versatility: Suitable for a wide range of materials and processes.
- Energy Efficiency: The insulation layer minimizes heat loss, improving overall efficiency.
-
Comparison with Horizontal Tube Furnaces:
- Drop tube furnaces are vertically oriented, while traditional tube furnaces are typically horizontal.
- The vertical design of drop tube furnaces is better suited for processes involving gravity-assisted material movement.
- Horizontal tube furnaces are more commonly used for processes like annealing, brazing, and calcining, where material movement is not a primary concern.
-
Considerations for Equipment Purchasers:
- Material Compatibility: Ensure the furnace materials (e.g., quartz, alumina, graphite) are compatible with the intended applications.
- Temperature Range: Verify that the furnace can achieve the required temperatures for specific processes.
- Control System: Look for advanced temperature control systems with precise feedback mechanisms.
- Size and Throughput: Consider the dimensions of the furnace and its capacity for handling materials.
- Safety Features: Ensure the furnace includes safety mechanisms for high-temperature operations.
By understanding these key points, purchasers can make informed decisions when selecting a drop tube furnace for their specific needs, ensuring optimal performance and efficiency in their applications.
Summary Table:
Feature | Description |
---|---|
Design | Vertical orientation for gravity-assisted material movement. |
Key Components | Heating chamber, heating elements, thermocouple, insulation layer, outer casing. |
Applications | Pyrolysis, thermal decomposition, materials testing, energy research. |
Advantages | Uniform heating, controlled gradients, versatility, energy efficiency. |
Comparison | Better for gravity-assisted processes compared to horizontal tube furnaces. |
Purchasing Considerations | Material compatibility, temperature range, control system, size, safety. |
Ready to enhance your high-temperature processes? Contact us today to find the perfect drop tube furnace for your needs!