Dry ashing is a laboratory technique used to determine the inorganic (ash) content of a sample by burning off organic material in a controlled environment. This process is typically carried out in a muffle furnace, which provides precise temperature control and isolates the sample from external contaminants. The sample is heated to high temperatures (usually between 500-600°C) in the presence of oxygen, causing organic matter to combust and leaving behind inorganic residues such as sulfates, phosphates, chlorides, and silicates. The ash content is calculated by comparing the weight of the sample before and after the ashing process. Dry ashing is widely used in industries and research to comply with international standards like ISO, EN, or ASTM, or for specific applications such as Loss on Ignition (LOI).
Key Points Explained:
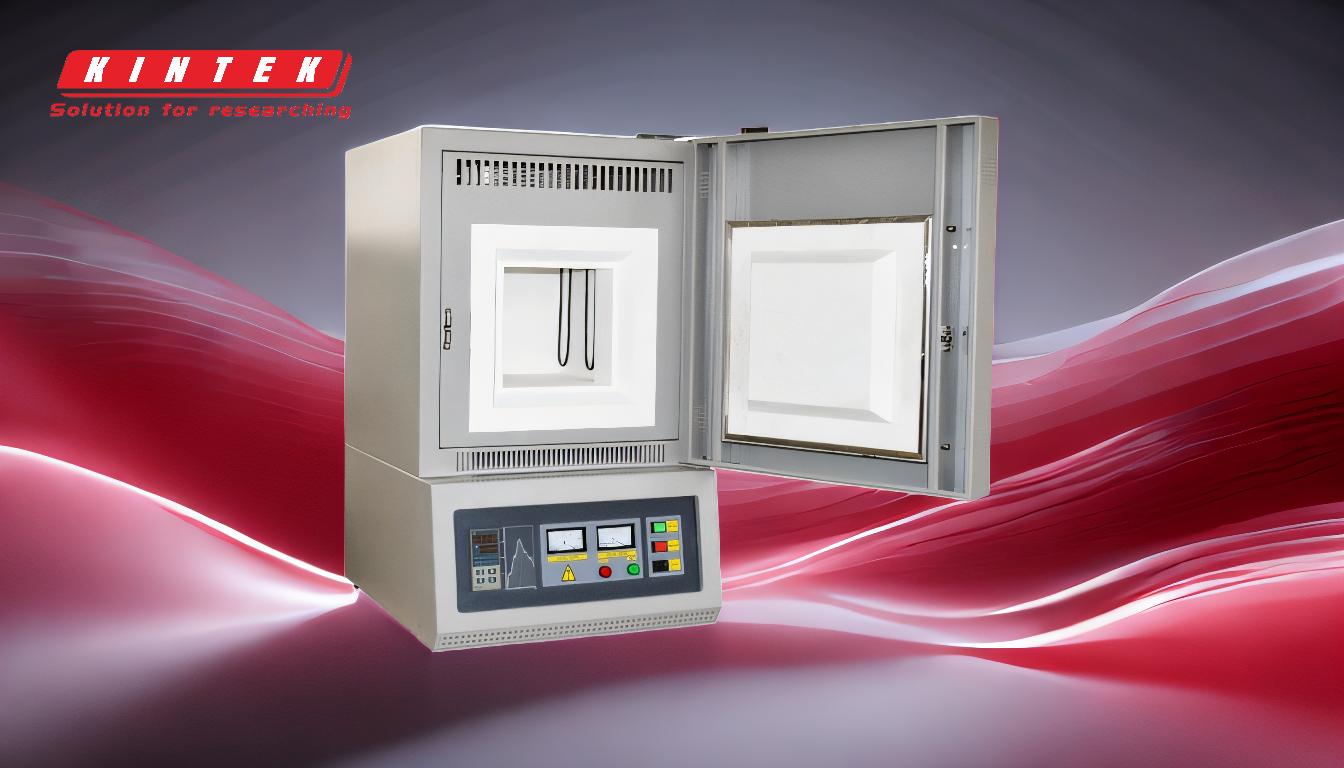
-
Definition of Dry Ashing:
- Dry ashing is an analytical technique used to determine the inorganic (non-combustible) content of a sample by burning off organic material in a controlled environment.
- It involves heating the sample in a high-temperature muffle furnace, typically between 500-600°C, in the presence of oxygen.
-
Purpose of Dry Ashing:
- The primary goal is to remove organic material and leave behind inorganic residues, which can then be analyzed to determine the ash content of the sample.
- It is used in various industries and research settings to measure ash content, comply with international standards, or perform specific tests like Loss on Ignition (LOI).
-
Equipment Used: Muffle Furnace:
- A muffle furnace is the most appropriate equipment for dry ashing due to its precise temperature control and ability to isolate the sample from combustion contaminants.
- The furnace ensures that the sample is heated uniformly and that the results are accurate and uncontaminated.
-
Process of Dry Ashing:
- The sample is placed in the muffle furnace and heated to high temperatures (500-600°C) in the presence of oxygen.
- During the process, water and volatile materials are vaporized, and organic matter is burned, producing carbon dioxide, water vapor, and nitrogen gas.
- Most minerals in the sample are converted into inorganic compounds such as sulfates, phosphates, chlorides, and silicates.
-
Calculation of Ash Content:
- The ash content is calculated using the formula: [ \text{Ash content} = \frac{M(\text{ash})}{M(\text{dry})} \times 100% ] where ( M(\text{ash}) ) is the weight of the sample after ashing, and ( M(\text{dry}) ) is the weight of the sample before ashing.
- This calculation provides a quantitative measure of the inorganic content in the sample.
-
Applications of Dry Ashing:
- Dry ashing is used in various industries, including food, pharmaceuticals, and environmental testing, to determine the inorganic content of materials.
- It is also used in research to study the composition of materials and to comply with international standards like ISO, EN, or ASTM.
-
Advantages of Using a Muffle Furnace for Dry Ashing:
- Precise Temperature Control: Ensures that the sample is heated uniformly and accurately.
- Isolation from Contaminants: Prevents external contaminants from affecting the results.
- Ease of Use: Modern muffle furnaces are designed with user-friendly features, such as easy replacement of components like the heating element and chamber.
-
Considerations for Dry Ashing:
- Sample Preparation: The sample must be prepared correctly to ensure accurate results.
- Temperature and Time: The temperature and duration of heating must be carefully controlled to avoid incomplete combustion or excessive loss of volatile materials.
- Safety: Proper safety measures must be taken when working with high temperatures and potentially hazardous materials.
By understanding these key points, one can effectively use dry ashing in a muffle furnace to determine the inorganic content of various samples, ensuring accurate and reliable results.
Summary Table:
Key Aspect | Details |
---|---|
Definition | Analytical technique to determine inorganic content by burning organic matter. |
Purpose | Measure ash content, comply with standards, or perform LOI tests. |
Equipment | Muffle furnace for precise temperature control and contamination isolation. |
Process | Heat sample to 500-600°C in oxygen, leaving inorganic residues. |
Ash Content Formula | [ \text{Ash content} = \frac{M(\text{ash})}{M(\text{dry})} \times 100% ] |
Applications | Food, pharmaceuticals, environmental testing, and research. |
Advantages | Precise heating, contamination-free results, and user-friendly design. |
Considerations | Proper sample prep, controlled temperature/time, and safety precautions. |
Ready to enhance your lab's capabilities? Contact us today to learn more about muffle furnaces for dry ashing!