The epitaxial growth process of graphene, particularly via Chemical Vapor Deposition (CVD), involves the controlled deposition of carbon atoms onto a substrate to form a single, continuous layer of graphene. This process typically occurs in a high-temperature environment and involves the use of a metal catalyst, such as nickel or copper, to facilitate the decomposition of carbon precursors and the subsequent formation of graphene. The process can be broken down into two main steps: the pyrolysis of carbon precursors to form carbon species, and the nucleation and growth of graphene from these carbon species. The quality of the graphene produced depends on factors such as temperature, pressure, and the choice of catalyst.
Key Points Explained:
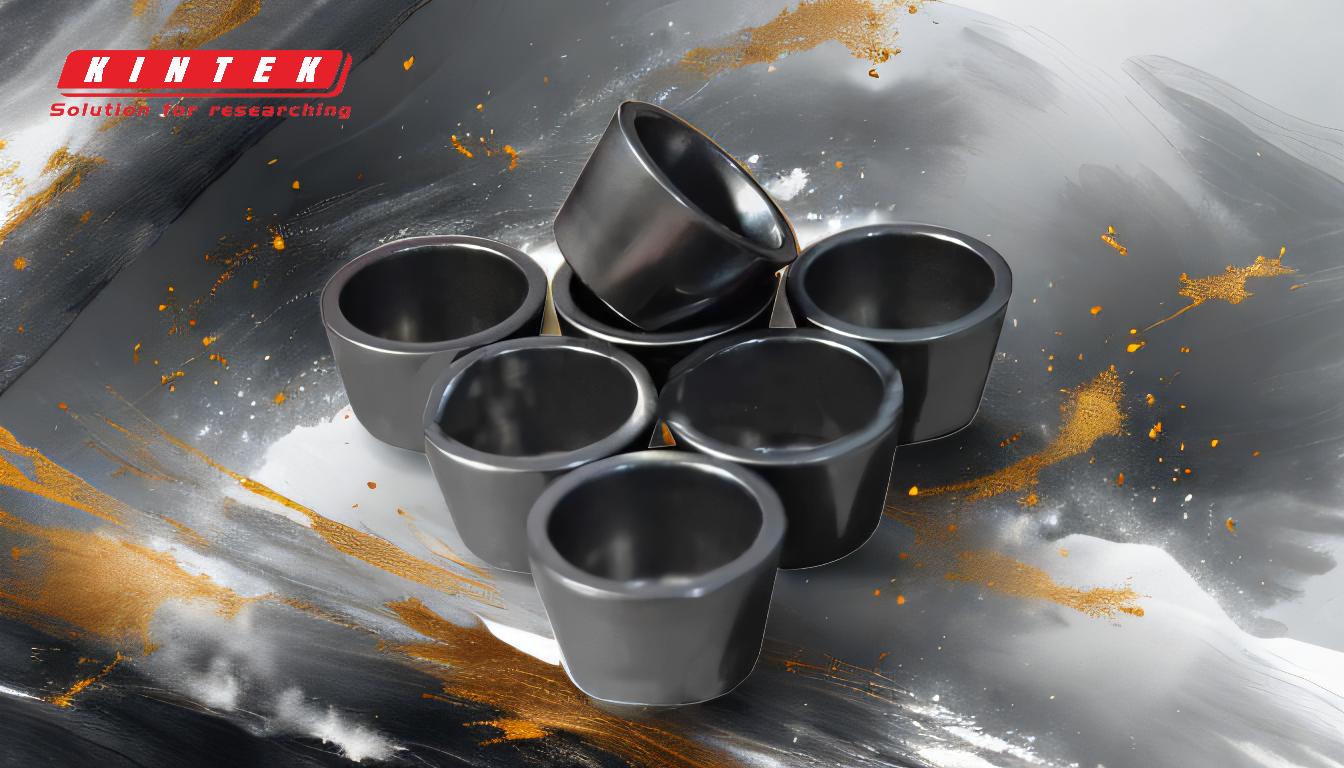
-
Carbon Precursor Adsorption and Decomposition:
- Process: In the CVD process, carbon-containing gases (such as methane, CH₄) are introduced into a reaction chamber where they adsorb onto the surface of a metal catalyst (e.g., nickel or copper).
- Decomposition: The adsorbed carbon precursors decompose on the catalyst surface at high temperatures (typically 900-1000°C), releasing carbon atoms. This step is crucial for ensuring that the carbon atoms are available for graphene formation.
- Importance: The decomposition must occur on the substrate surface to prevent the formation of carbon soot or clusters, which can degrade the quality of the graphene.
-
Carbon Diffusion and Cluster Formation:
- Diffusion: The carbon atoms generated from the decomposition step diffuse across the surface of the catalyst. This diffusion is driven by the high temperature and the catalytic properties of the metal substrate.
- Cluster Formation: As the carbon atoms diffuse, they begin to form small carbon clusters. These clusters are the initial stages of graphene nucleation.
- Critical Size: Once these clusters exceed a critical size, they act as nucleation sites for the growth of graphene crystals.
-
Nucleation and Growth of Graphene:
- Nucleation: The carbon clusters that exceed the critical size serve as the nucleation points for graphene crystals. At this stage, the graphene islands start to form on the catalyst surface.
- Growth: As the CVD process continues, additional carbon atoms are incorporated into the edges of the graphene islands, causing them to grow larger. This growth continues until the islands merge to form a continuous, single layer of graphene.
- Continuous Layer: The final product is a continuous, uniform layer of graphene that covers the entire surface of the catalyst.
-
Role of the Catalyst:
- Catalyst Selection: The choice of catalyst (e.g., nickel or copper) is critical in determining the quality and properties of the graphene. Nickel, for example, allows for the dissolution of carbon atoms into the metal, which can lead to the formation of a solid solution. Upon cooling, the carbon atoms precipitate out to form graphene.
- Temperature Control: The catalyst also helps to lower the required reaction temperature, making the process more energy-efficient. The catalyst's ability to facilitate the decomposition of carbon precursors and the diffusion of carbon atoms is key to the successful growth of graphene.
-
Cooling and Graphene Formation:
- Cooling Process: After the graphene has formed, the substrate is cooled down, typically in an inert gas atmosphere (e.g., argon). This cooling step is crucial for stabilizing the graphene layer and preventing defects.
- Solid Solution Formation: In the case of nickel, the carbon atoms dissolve into the metal during the high-temperature phase and then precipitate out during cooling to form graphene. This process helps to ensure a uniform and high-quality graphene layer.
-
Preventing Carbon Soot Formation:
- Surface Pyrolysis: One of the key challenges in the CVD process is preventing the formation of carbon soot or unwanted carbon clusters. This is achieved by ensuring that the pyrolysis of carbon precursors occurs on the substrate surface rather than in the gas phase.
- Quality Control: By controlling the temperature, pressure, and gas flow rates, it is possible to minimize the formation of defects and ensure the production of high-quality graphene.
-
Applications and Implications:
- High-Quality Graphene: The epitaxial growth process via CVD is widely used to produce high-quality graphene for various applications, including electronics, sensors, and energy storage devices.
- Scalability: The CVD method is scalable, making it suitable for industrial production of graphene. However, the process requires precise control over various parameters to ensure consistent quality.
In summary, the epitaxial growth of graphene via CVD is a complex but highly controlled process that involves the adsorption and decomposition of carbon precursors, the diffusion and clustering of carbon atoms, and the nucleation and growth of graphene crystals. The use of a metal catalyst is essential for facilitating these steps and ensuring the production of high-quality graphene. The process is scalable and has significant implications for the development of graphene-based technologies.
Summary Table:
Step | Description |
---|---|
Carbon Precursor Adsorption | Carbon-containing gases adsorb onto a metal catalyst surface. |
Decomposition | High temperatures break down carbon precursors into carbon atoms. |
Carbon Diffusion | Carbon atoms diffuse across the catalyst surface, forming clusters. |
Nucleation | Clusters exceed critical size, initiating graphene crystal formation. |
Growth | Carbon atoms integrate into graphene edges, forming a continuous layer. |
Cooling | Substrate cooling stabilizes the graphene layer, ensuring high quality. |
Catalyst Role | Catalysts like nickel or copper facilitate decomposition and carbon diffusion. |
Discover how CVD can revolutionize your graphene production—contact our experts today for tailored solutions!