Evaporation in thin film deposition is a process where a source material is heated to its evaporation point in a vacuum environment, causing it to transition from a solid or liquid state into a vapor. This vapor then travels through the vacuum and condenses onto a substrate, forming a thin, uniform film. The process relies on thermal energy, typically provided by electrical resistance heating or electron beams, to achieve the necessary temperatures for evaporation. The vacuum environment is crucial to prevent contamination and ensure the vapor particles travel unimpeded to the substrate. This method is widely used in microfabrication and industrial applications, such as creating metallized plastic films.
Key Points Explained:
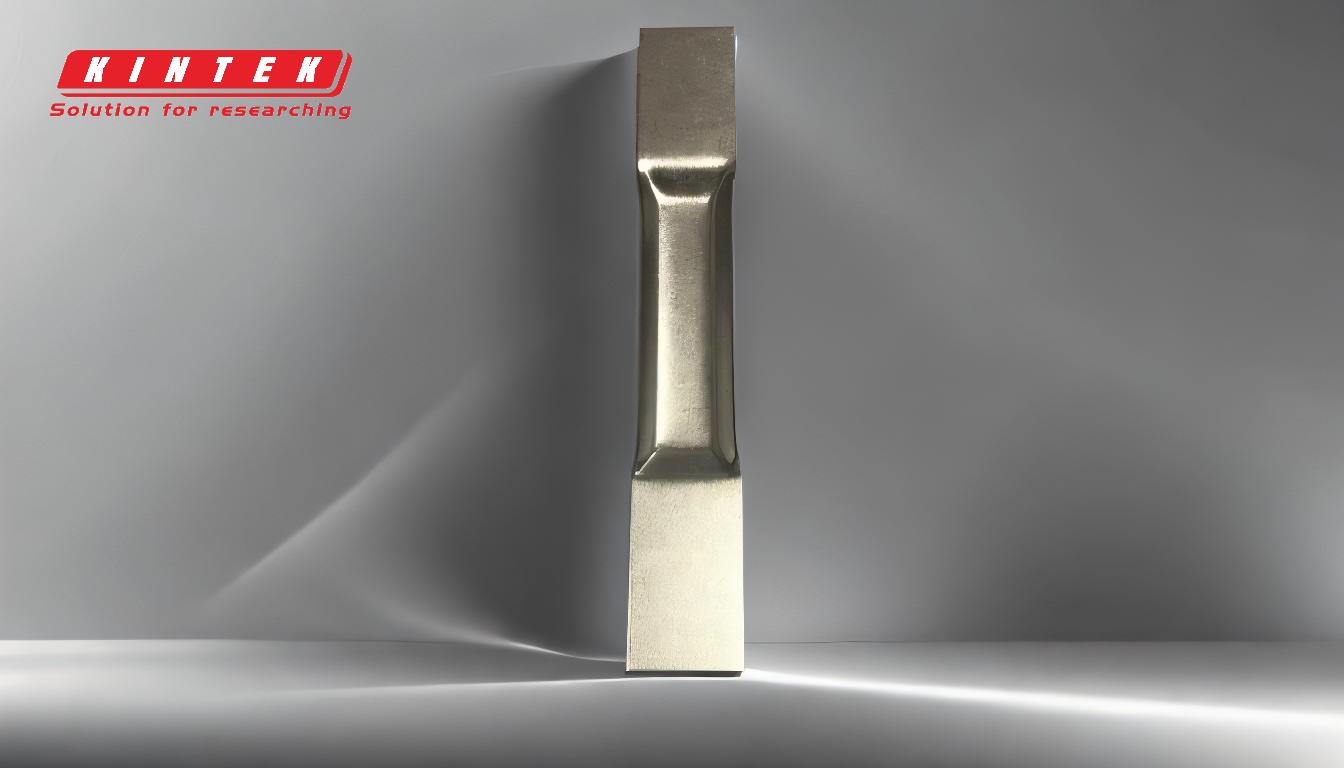
-
Definition of Evaporation in Thin Film Deposition:
- Evaporation in thin film deposition refers to the process of heating a source material until it evaporates, forming a vapor that travels through a vacuum and condenses onto a substrate to form a thin film.
- This process is essential in creating uniform, high-quality thin films for various applications, including microfabrication and industrial coatings.
-
Role of Thermal Energy:
- Thermal energy is the driving force behind the evaporation process. It is typically generated using:
- Electric resistance heaters: These use tungsten heating elements to melt and evaporate the source material.
- Electron beam evaporators: These direct a focused electron beam to heat and vaporize the material, especially useful for materials with high melting points.
- The choice of heat source depends on the material's properties and the desired film characteristics.
- Thermal energy is the driving force behind the evaporation process. It is typically generated using:
-
Importance of Vacuum Environment:
- The process must occur in a vacuum to:
- Prevent contamination from air or other gases.
- Allow vapor particles to travel directly to the substrate without interference.
- Ensure uniform deposition and high-quality film formation.
- The vacuum environment is critical for maintaining the integrity of the thin film.
- The process must occur in a vacuum to:
-
Steps in the Evaporation Process:
- Heating: The source material is heated to its evaporation point using a thermal or electron beam source.
- Evaporation: The material transitions from a solid or liquid state into a vapor.
- Transport: The vapor particles travel through the vacuum to the substrate.
- Condensation: The vapor condenses on the substrate, forming a solid thin film.
- This sequence ensures precise control over film thickness and uniformity.
-
Applications of Evaporation in Thin Film Deposition:
- Microfabrication: Used in semiconductor manufacturing to create thin films for electronic devices.
- Macro-scale Products: Applied in industrial processes, such as metallizing plastic films for packaging or reflective coatings.
- The versatility of the evaporation method makes it suitable for both small-scale and large-scale production.
-
Comparison to Natural Phenomena:
- The evaporation process can be likened to the condensation of steam from a bath into water droplets on a ceiling. In both cases, a vapor transitions back to a solid or liquid state upon contact with a cooler surface.
-
Advantages of Thermal Evaporation:
- High purity of deposited films due to the vacuum environment.
- Precise control over film thickness and uniformity.
- Compatibility with a wide range of materials, including metals, alloys, and some ceramics.
-
Challenges and Considerations:
- Material Limitations: Some materials may decompose or react at high temperatures.
- Equipment Costs: High vacuum systems and specialized heating sources can be expensive.
- Scalability: While effective for small-scale applications, scaling up for large-area coatings can be challenging.
By understanding these key points, one can appreciate the complexity and precision involved in the evaporation process for thin film deposition, as well as its critical role in modern manufacturing and technology.
Summary Table:
Key Aspect | Details |
---|---|
Definition | Heating a material to evaporate it, forming a vapor that condenses into a thin film. |
Thermal Energy Sources | Electric resistance heaters, electron beam evaporators. |
Vacuum Importance | Prevents contamination, ensures vapor travels unimpeded, maintains film quality. |
Process Steps | Heating → Evaporation → Transport → Condensation. |
Applications | Microfabrication, semiconductor manufacturing, metallized plastic films. |
Advantages | High purity, precise thickness control, material versatility. |
Challenges | Material limitations, high equipment costs, scalability issues. |
Discover how evaporation in thin film deposition can elevate your applications—contact our experts today!