An indirect arc furnace is a type of electric arc furnace where the arc is not in direct contact with the material being heated. Instead, the arc is struck between two electrodes, and the heat generated is transferred to the material through radiation and convection. This method allows for more controlled heating and is often used in applications where precise temperature control is necessary, such as in the melting of metals or the production of certain chemicals. The furnace typically consists of a refractory-lined chamber, electrodes, and a power supply system that generates the arc.
Key Points Explained:
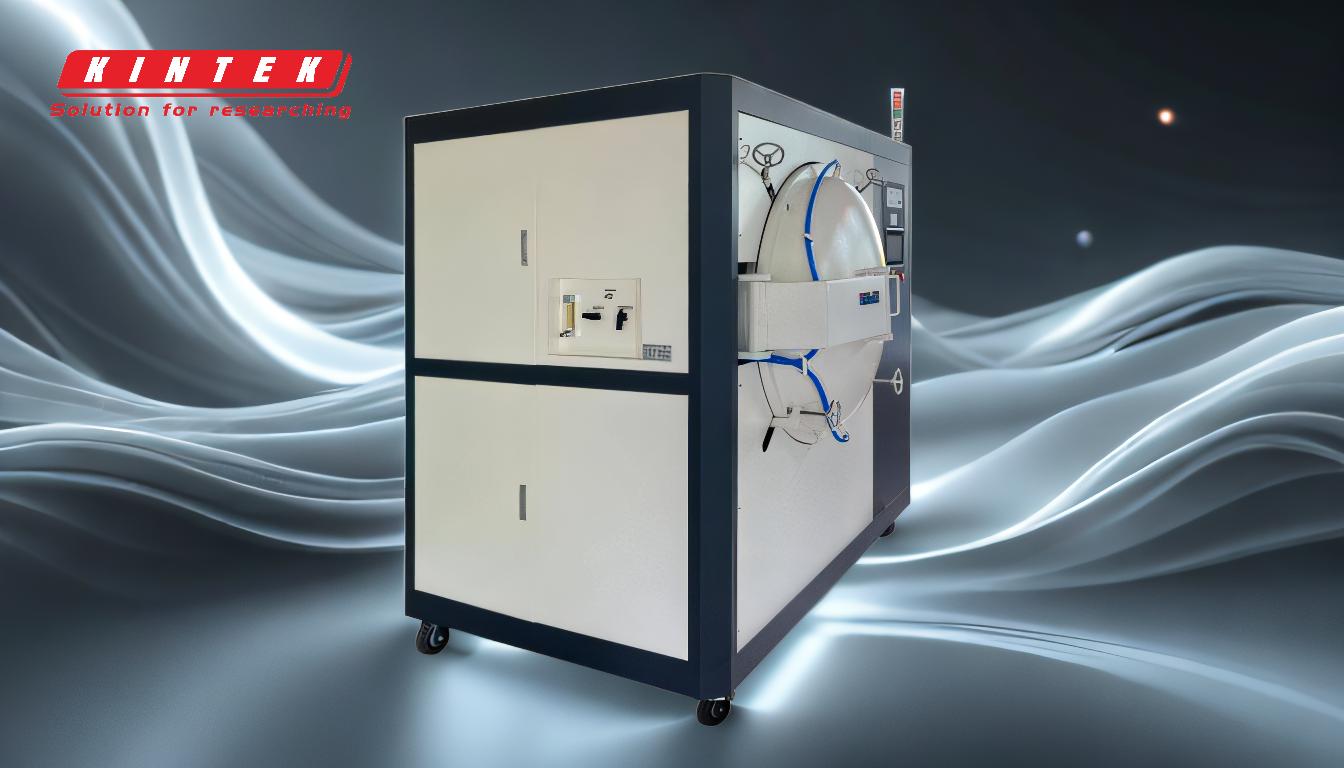
-
Definition and Basic Principle:
- An indirect arc furnace operates by generating an electric arc between two electrodes. Unlike a direct arc furnace, the arc does not come into direct contact with the material being heated. Instead, the heat from the arc is transferred to the material through radiation and convection. This indirect method of heating allows for more precise control over the temperature, making it suitable for processes that require careful thermal management.
-
Components of an Indirect Arc Furnace:
- Refractory-Lined Chamber: The chamber is lined with refractory materials that can withstand high temperatures and provide insulation to maintain the heat within the furnace.
- Electrodes: The electrodes are crucial for generating the electric arc. They are typically made of materials that can withstand high temperatures and are resistant to erosion.
- Power Supply System: This system converts the input voltage (usually 220V or 380V) into a low voltage and high current, which is necessary to create and sustain the electric arc.
-
Working Mechanism:
- The electric arc is initiated by creating a short circuit between the positive and negative electrodes. Once the arc is established, it becomes a self-sustaining discharge phenomenon, maintaining stable combustion without extinguishing. The heat generated by the arc is then transferred to the material in the furnace through radiation and convection, ensuring even heating.
-
Applications:
- Metal Melting: Indirect arc furnaces are commonly used in the melting of metals, especially those that require precise temperature control, such as certain alloys.
- Chemical Production: These furnaces are also used in the production of chemicals that require high-temperature processing, where the indirect heating method ensures that the material is heated uniformly without direct exposure to the arc.
-
Advantages:
- Precise Temperature Control: The indirect heating method allows for more precise control over the temperature, which is essential for processes that require specific thermal conditions.
- Uniform Heating: The heat is transferred evenly through radiation and convection, ensuring that the material is heated uniformly.
- Reduced Contamination: Since the arc does not come into direct contact with the material, there is less risk of contamination from the electrodes.
-
Comparison with Other Furnaces:
- Direct Arc Furnace: In a direct arc furnace, the arc comes into direct contact with the material, which can lead to more rapid heating but also increases the risk of contamination and less precise temperature control.
- Plasma Arc Furnace: A plasma arc furnace uses a low-temperature plasma flow generated by an electric arc heater to melt materials. While it also provides high temperatures, the mechanism of heat transfer is different, and it may not offer the same level of control as an indirect arc furnace.
- Channel Induction Furnace: A channel induction furnace uses electromagnetic induction to generate heat within the material itself. This method is efficient for melting metals but does not provide the same level of temperature control as an indirect arc furnace.
In summary, an indirect arc furnace is a versatile and efficient heating device that offers precise temperature control and uniform heating, making it suitable for a variety of industrial applications, particularly in metal melting and chemical production.
Summary Table:
Aspect | Details |
---|---|
Definition | Electric arc furnace where heat is transferred indirectly via radiation and convection. |
Key Components | Refractory-lined chamber, electrodes, power supply system. |
Working Mechanism | Arc between electrodes heats material indirectly, ensuring uniform heating. |
Applications | Metal melting, chemical production. |
Advantages | Precise temperature control, uniform heating, reduced contamination. |
Comparison | Offers better control than direct arc or channel induction furnaces. |
Discover how an indirect arc furnace can improve your industrial processes—contact us today for expert advice!