Ion beam sputtering (IBS) is a highly precise thin film deposition technique used in physical vapor deposition (PVD). It involves directing a focused ion beam onto a target material, causing the ejection of atomic-sized particles that deposit onto a substrate to form a thin film. This method is characterized by its monoenergetic and highly collimated ion beam, which allows for exceptional control over film growth, resulting in dense, high-quality films. IBS is versatile, capable of depositing a wide range of materials, including metals, oxides, nitrides, and carbides. Its advantages include superior energy bonding, precision, uniformity, and flexibility in material composition.
Key Points Explained:
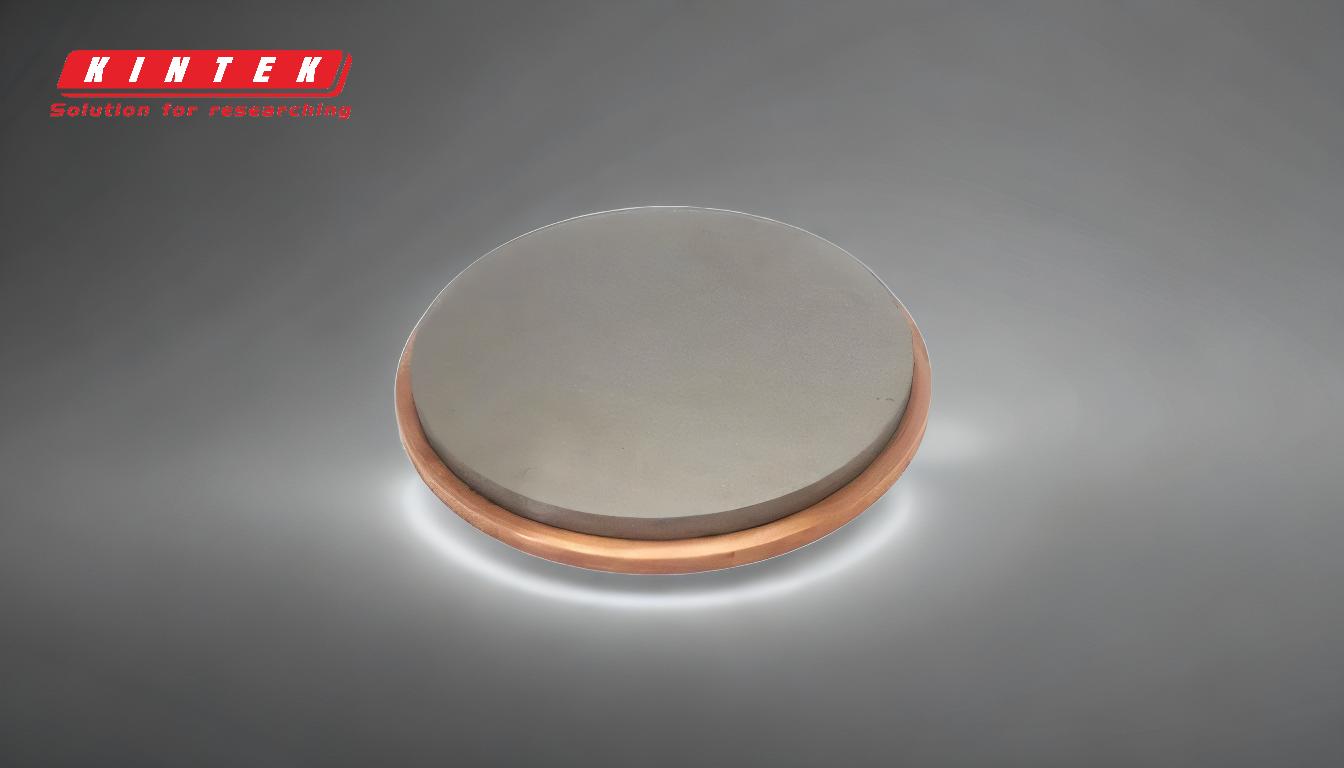
-
Definition and Process of Ion Beam Sputtering (IBS):
- IBS is a physical vapor deposition (PVD) technique where an ion beam is used to sputter a target material, ejecting atoms that deposit onto a substrate.
- The process occurs in a vacuum chamber filled with inert gas (e.g., argon). The target material is negatively charged, attracting positively charged ions from the ion beam.
- These ions collide with the target, dislodging atomic-sized particles that travel and adhere to the substrate, forming a thin film.
-
Key Components of IBS:
- Ion Source: Generates a focused, monoenergetic ion beam (e.g., argon ions) that is directed at the target material.
- Target Material: The material to be sputtered, which can be a metal, dielectric, oxide, nitride, or other compounds.
- Substrate: The surface onto which the sputtered material is deposited to form the thin film.
- Vacuum Chamber: Provides a controlled environment free from contaminants, ensuring high-quality film deposition.
-
Advantages of Ion Beam Sputtering:
- Precision Control: The monoenergetic and highly collimated ion beam allows for precise control over film thickness, composition, and uniformity.
- Superior Film Quality: Films produced by IBS are dense, smooth, and free from defects due to the high-energy bonding process.
- Versatility: IBS can deposit a wide range of materials, including pure metals, alloys, oxides, nitrides, borides, and carbides.
- Strong Bonding: The energy bonding in IBS is approximately 100 times higher than conventional vacuum coating, ensuring a strong and durable film-substrate bond.
- Flexibility: The technique is adaptable to various target materials and compositions, making it suitable for diverse applications.
-
Comparison with Other Sputtering Techniques:
- DC Magnetron Sputtering: Used primarily for electrically conductive materials, offering high deposition rates but less precision compared to IBS.
- RF Sputtering: Suitable for insulating materials like oxides, though at lower deposition rates than DC magnetron sputtering.
- Reactive Sputtering: Involves introducing reactive gases (e.g., oxygen) during the process to form compound films, such as oxides or nitrides.
- Ion-Assisted Sputtering: Combines ion beam sputtering with additional ion bombardment to enhance film properties.
- Gas Flow Sputtering: Uses a gas flow to transport sputtered material, often for specialized applications.
-
Applications of Ion Beam Sputtering:
- Optical Coatings: IBS is widely used to produce high-quality optical films for lenses, mirrors, and filters due to its precision and uniformity.
- Semiconductor Manufacturing: The technique is employed in the fabrication of thin films for microelectronics and integrated circuits.
- Magnetic Storage Media: IBS is used to deposit thin films for hard disks and other magnetic storage devices.
- Protective Coatings: The strong bonding and durability of IBS films make them ideal for protective coatings in harsh environments.
- Research and Development: IBS is utilized in advanced material research to explore new thin film properties and applications.
-
Challenges and Considerations:
- Cost: IBS equipment and processes can be expensive due to the need for high vacuum conditions and specialized ion sources.
- Complexity: The technique requires precise control of parameters such as ion beam energy, target-substrate distance, and gas pressure.
- Material Limitations: While versatile, IBS may not be suitable for all materials, particularly those with low sputtering yields or high melting points.
-
Future Trends in Ion Beam Sputtering:
- Nanotechnology: IBS is increasingly being used to fabricate nanostructured thin films for advanced applications in electronics, photonics, and energy storage.
- Hybrid Techniques: Combining IBS with other deposition methods (e.g., chemical vapor deposition) to achieve unique film properties.
- Automation and AI: Integration of automation and artificial intelligence to optimize process parameters and improve efficiency.
In summary, ion beam sputtering is a highly advanced and versatile thin film deposition technique that offers unparalleled precision, control, and quality. Its applications span across industries, from optics and semiconductors to protective coatings and advanced research. While it comes with certain challenges, ongoing advancements in technology and process optimization continue to expand its potential.
Summary Table:
Aspect | Details |
---|---|
Definition | Physical vapor deposition (PVD) using a focused ion beam to sputter target material. |
Key Components | Ion source, target material, substrate, vacuum chamber. |
Advantages | Precision control, superior film quality, versatility, strong bonding. |
Applications | Optical coatings, semiconductors, magnetic storage, protective coatings. |
Challenges | High cost, complexity, material limitations. |
Future Trends | Nanotechnology, hybrid techniques, automation, and AI integration. |
Unlock the potential of ion beam sputtering for your projects—contact our experts today!