Isostatic pressing is a manufacturing process that applies uniform pressure from all directions to a product, ensuring consistent density and strength regardless of its shape or size. It is divided into two main types: cold isostatic pressing (CIP) and hot isostatic pressing (HIP). CIP is performed at or slightly above room temperature using a liquid medium, while HIP operates at elevated temperatures and is used for densification and improving material properties. CIP is further categorized into wet bag and dry bag methods, each suited for different applications based on part complexity and size. This process is widely used in industries requiring high-density and uniform materials, such as ceramics, metals, and advanced battery technologies.
Key Points Explained:
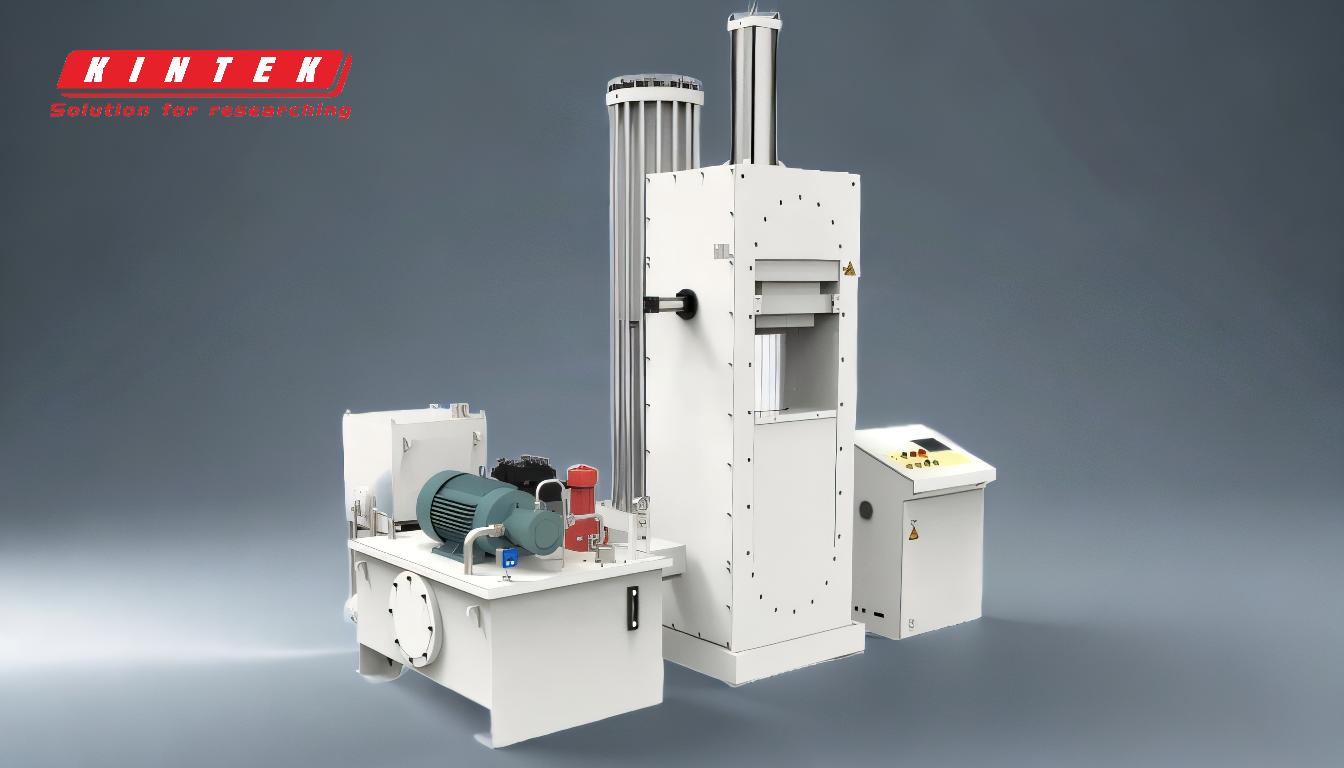
-
What is Isostatic Pressing?
- Isostatic pressing is a technique that applies equal pressure uniformly from all directions to a material, ensuring consistent density and strength. This makes it ideal for producing complex shapes and large parts without compromising structural integrity.
-
Cold Isostatic Pressing (CIP):
- CIP is performed at or slightly above room temperature (typically <93°C) using a liquid medium such as water, oil, or a glycol mixture.
- It is used to form "raw" parts with sufficient strength for handling and further processing. These parts are later sintered to achieve final density and strength.
- CIP is divided into two methods:
- Wet Bag Method: The mold is removed and refilled after each pressure cycle, making it suitable for large and complex parts.
- Dry Bag Method: The mold is an integral part of the vessel, allowing for faster production of simpler and smaller parts. Modern cold isostatic pressing machines used in this method offer advanced features like pressure curve control, multi-pressure section processes, and data exporting.
-
Hot Isostatic Pressing (HIP):
- HIP is performed at high temperatures and pressures, typically used for densification and improving the mechanical properties of materials.
- It is commonly applied to castings, metal powders, and other components to eliminate porosity and enhance strength.
-
Applications of Isostatic Pressing:
- CIP: Used in industries like ceramics, advanced batteries (e.g., solid-state batteries), and powder metallurgy to produce uniform, high-density parts.
- HIP: Applied in aerospace, medical implants, and high-performance alloys to achieve near-net-shape components with superior mechanical properties.
-
Advantages of Isostatic Pressing:
- Uniform density and strength across complex geometries.
- Ability to produce large and intricate parts.
- Enhanced material properties, such as reduced porosity and improved mechanical performance.
-
Comparison of CIP and HIP:
- Temperature: CIP operates at low temperatures, while HIP requires high temperatures.
- Purpose: CIP is used for forming raw parts, whereas HIP focuses on densification and material enhancement.
- Applications: CIP is ideal for ceramics and powders, while HIP is suited for metals and high-performance alloys.
By understanding these key points, equipment and consumable purchasers can make informed decisions about which isostatic pressing method best suits their manufacturing needs.
Summary Table:
Aspect | Cold Isostatic Pressing (CIP) | Hot Isostatic Pressing (HIP) |
---|---|---|
Temperature | Low (≤93°C) | High (elevated temperatures) |
Medium | Liquid (water, oil, glycol) | High-pressure gas |
Purpose | Forms raw parts for further processing | Densification and material enhancement |
Methods | Wet Bag (for large/complex parts), Dry Bag (for simpler/smaller parts) | N/A |
Applications | Ceramics, advanced batteries, powder metallurgy | Aerospace, medical implants, high-performance alloys |
Advantages | Uniform density, strength for complex shapes, ideal for large parts | Eliminates porosity, improves mechanical properties, near-net-shape components |
Discover the right isostatic pressing solution for your needs—contact our experts today!