Low-Pressure Chemical Vapor Deposition (LPCVD) is a specialized variant of Chemical Vapor Deposition (CVD) that operates at reduced pressures, typically between 0.1 and 10 Torr, and temperatures ranging from 200 to 800°C. This process involves introducing reactants into a vacuum chamber using a precursor delivery system, where they undergo chemical reactions to form thin films on a substrate. The low-pressure environment increases the mean free path of molecules and enhances gas diffusion, leading to faster mass transfer and reaction rates. LPCVD is known for its ability to produce high-quality, uniform coatings with excellent step coverage, making it ideal for applications in semiconductor manufacturing and other precision industries.
Key Points Explained:
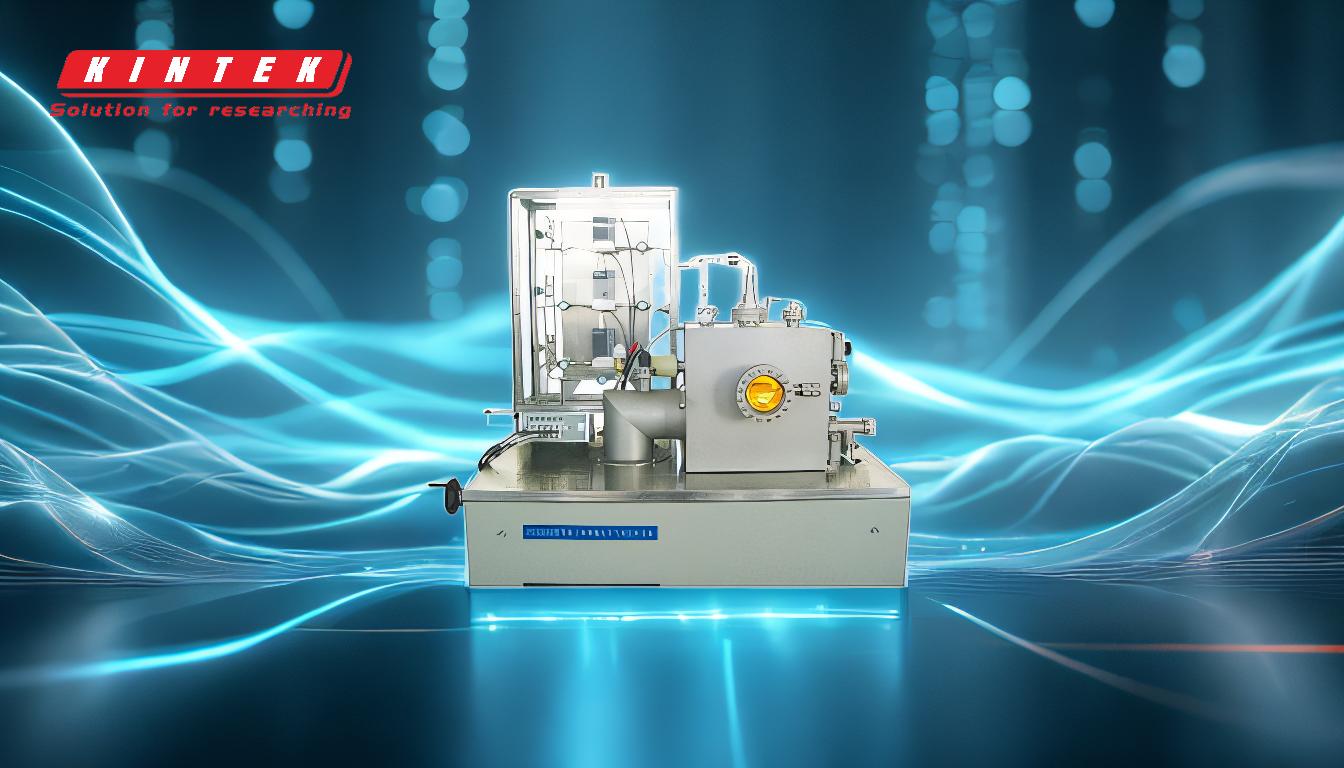
-
Definition and Purpose of LPCVD:
- LPCVD is a type of CVD process that operates at significantly reduced pressures (0.1–10 Torr) and moderate temperatures (200–800°C).
- The primary goal is to deposit thin films of materials onto substrates through controlled chemical reactions in a vacuum environment.
-
Operating Conditions:
- Pressure: LPCVD operates at pressures between 0.1 and 10 Torr, which is much lower than standard atmospheric pressure (760 Torr). This low-pressure environment increases the mean free path of gas molecules, enhancing the efficiency of the deposition process.
- Temperature: The process typically occurs at temperatures between 200 and 800°C, which are sufficient to activate the chemical reactions needed for film deposition without damaging the substrate.
-
Process Mechanism:
- Reactants are introduced into the chamber using a specialized precursor delivery system, often equipped with a showerhead to ensure uniform distribution.
- The substrate is heated to promote surface reactions, where the reactants decompose or react to form a solid film.
- By-products of the reaction are removed from the chamber using vacuum pumps, maintaining the low-pressure environment.
-
Advantages of LPCVD:
- Enhanced Mass Transfer: The low-pressure environment increases the gas diffusion coefficient, accelerating the mass transfer rate of reactants and by-products.
- Uniform Coatings: LPCVD provides excellent step coverage, ensuring uniform deposition even on complex geometries.
- High Purity: The process yields high-purity films with minimal contamination, making it suitable for applications requiring precise material properties.
- Versatility: LPCVD can be used with a wide range of materials, including non-silicon substrates, and is compatible with various deposition rates.
-
Applications:
- Semiconductor Manufacturing: LPCVD is widely used in the production of integrated circuits, where it deposits thin films of silicon dioxide, silicon nitride, and polysilicon.
- Optoelectronics: The process is employed in the fabrication of optical coatings and devices.
- Microelectromechanical Systems (MEMS): LPCVD is used to create thin-film structures in MEMS devices, where precision and uniformity are critical.
-
Comparison with Other CVD Techniques:
- Atmospheric Pressure CVD (APCVD): Operates at atmospheric pressure, which can lead to faster deposition rates but may result in less uniform coatings compared to LPCVD.
- Plasma-Enhanced CVD (PECVD): Uses plasma to enhance chemical reactions at lower temperatures, but LPCVD typically offers better step coverage and film quality.
-
Equipment and Consumables:
- Precursor Delivery System: A critical component that ensures precise and uniform introduction of reactants into the chamber.
- Vacuum Pumps: Essential for maintaining the low-pressure environment and removing by-products.
- Heating Elements: Used to heat the substrate to the required temperature for deposition.
LPCVD is a highly controlled and efficient process that leverages low-pressure conditions to produce high-quality thin films with excellent uniformity and purity. Its versatility and precision make it a cornerstone technology in industries requiring advanced material deposition techniques.
Summary Table:
Aspect | Details |
---|---|
Definition | A CVD process operating at low pressures (0.1–10 Torr) and moderate temps. |
Purpose | Deposits thin films on substrates via controlled chemical reactions. |
Operating Conditions | Pressure: 0.1–10 Torr; Temperature: 200–800°C. |
Advantages | Enhanced mass transfer, uniform coatings, high purity, versatility. |
Applications | Semiconductors, optoelectronics, MEMS. |
Key Equipment | Precursor delivery system, vacuum pumps, heating elements. |
Interested in leveraging LPCVD for your precision manufacturing needs? Contact us today to learn more!