Low-Pressure Chemical Vapor Deposition (LPCVD) is a specialized form of CVD that operates at reduced pressures, offering unique advantages and disadvantages compared to standard CVD processes. LPCVD is widely used in semiconductor manufacturing and thin-film deposition due to its ability to produce high-quality, uniform films. However, it also comes with challenges such as high equipment costs and sensitivity to process parameters. Below, we explore the key advantages and disadvantages of LPCVD in detail.
Key Points Explained:
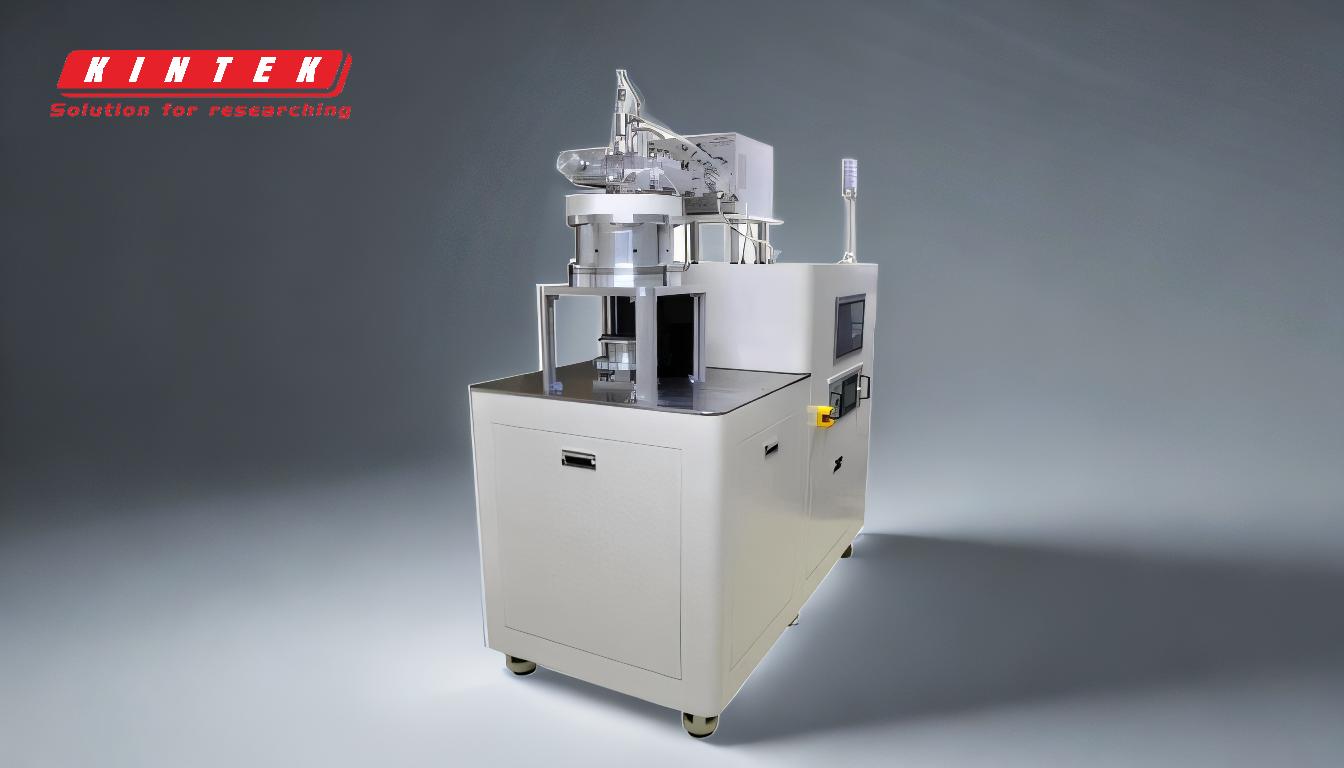
-
Advantages of LPCVD:
- Improved Film Uniformity: LPCVD operates at sub-atmospheric pressures, which minimizes unwanted gas-phase reactions and ensures better film uniformity across the wafer. This is particularly important for applications requiring precise control over film thickness and properties.
- High Purity and Density: Like traditional CVD, LPCVD produces thin films of extremely high purity and density. This makes it suitable for applications in the semiconductor industry, where material quality is critical.
- Lower Gas-Phase Reactions: The reduced pressure in LPCVD limits gas-phase reactions, which can lead to impurities or defects in the film. This results in higher-quality coatings with fewer defects.
- Versatility in Substrates: LPCVD can deposit films on a variety of substrates, including irregular surfaces, making it a flexible choice for diverse applications.
- No High-Pressure Requirements: Unlike some CVD methods, LPCVD does not require high-pressure environments, simplifying the equipment setup and reducing operational risks.
-
Disadvantages of LPCVD:
- High Equipment Costs: LPCVD systems are expensive to set up and maintain. The need for precise pressure control and specialized equipment increases the overall cost of the process.
- Toxic By-Products: The process can produce toxic gaseous by-products, which require proper handling and disposal to ensure safety and environmental compliance.
- Sensitivity to Process Parameters: LPCVD is highly sensitive to changes in parameters such as temperature, pressure, and gas flow rates. Small deviations can significantly impact film quality, making process control critical.
- Energy Consumption: Although LPCVD operates at lower pressures, it still requires significant energy input, particularly for maintaining precise temperature and pressure conditions.
- Challenges in Graphene Deposition: For applications like graphene deposition, LPCVD faces difficulties in creating uniform layers and separating graphene from the substrate without damaging its structure or properties.
-
Comparison with Other CVD Methods:
- Higher Deposition Rates: While LPCVD offers improved film quality, its deposition rates are generally lower compared to methods like Laser Chemical Vapor Deposition (LCVD), which benefits from three-dimensional diffusion paths.
- Cost-Effectiveness vs. HPHT: LPCVD is more cost-effective than High-Pressure High-Temperature (HPHT) methods for certain applications, such as diamond synthesis, due to lower equipment costs and the ability to produce larger, higher-quality crystals.
In summary, LPCVD is a powerful technique for producing high-quality, uniform thin films, particularly in the semiconductor industry. Its ability to operate at reduced pressures offers significant advantages in terms of film uniformity and purity. However, the high equipment costs, sensitivity to process parameters, and challenges in handling toxic by-products are notable disadvantages that must be carefully managed. For applications requiring precise control over film properties, LPCVD remains a preferred choice despite its limitations.
Summary Table:
Aspect | Advantages | Disadvantages |
---|---|---|
Film Uniformity | Improved uniformity due to reduced gas-phase reactions | - |
Purity and Density | High-purity, dense films ideal for semiconductors | - |
Gas-Phase Reactions | Limited reactions, fewer defects | - |
Substrate Versatility | Works on irregular surfaces | - |
Pressure Requirements | No high-pressure environment needed | - |
Equipment Costs | - | High setup and maintenance costs |
Toxic By-Products | - | Requires proper handling and disposal |
Process Sensitivity | - | Highly sensitive to temperature, pressure, and gas flow changes |
Energy Consumption | - | Significant energy input required |
Graphene Deposition | - | Challenges in creating uniform layers and separating graphene |
Discover how LPCVD can enhance your semiconductor processes—contact us today for expert guidance!