Magnetron sputtering is a versatile and widely used physical vapor deposition (PVD) technique with applications spanning multiple industries. It is primarily employed for thin film deposition, offering high speed, low temperature, and low damage characteristics. This technology is utilized in sectors such as electronics, optics, defense, medical devices, renewable energy, and manufacturing. Key applications include creating functional films with specific properties, improving durability in electronic components, producing anti-reflective coatings, and developing wear-resistant or corrosion-resistant coatings. Its ability to deposit precise, high-quality thin films makes it indispensable in modern technology and industrial processes.
Key Points Explained:
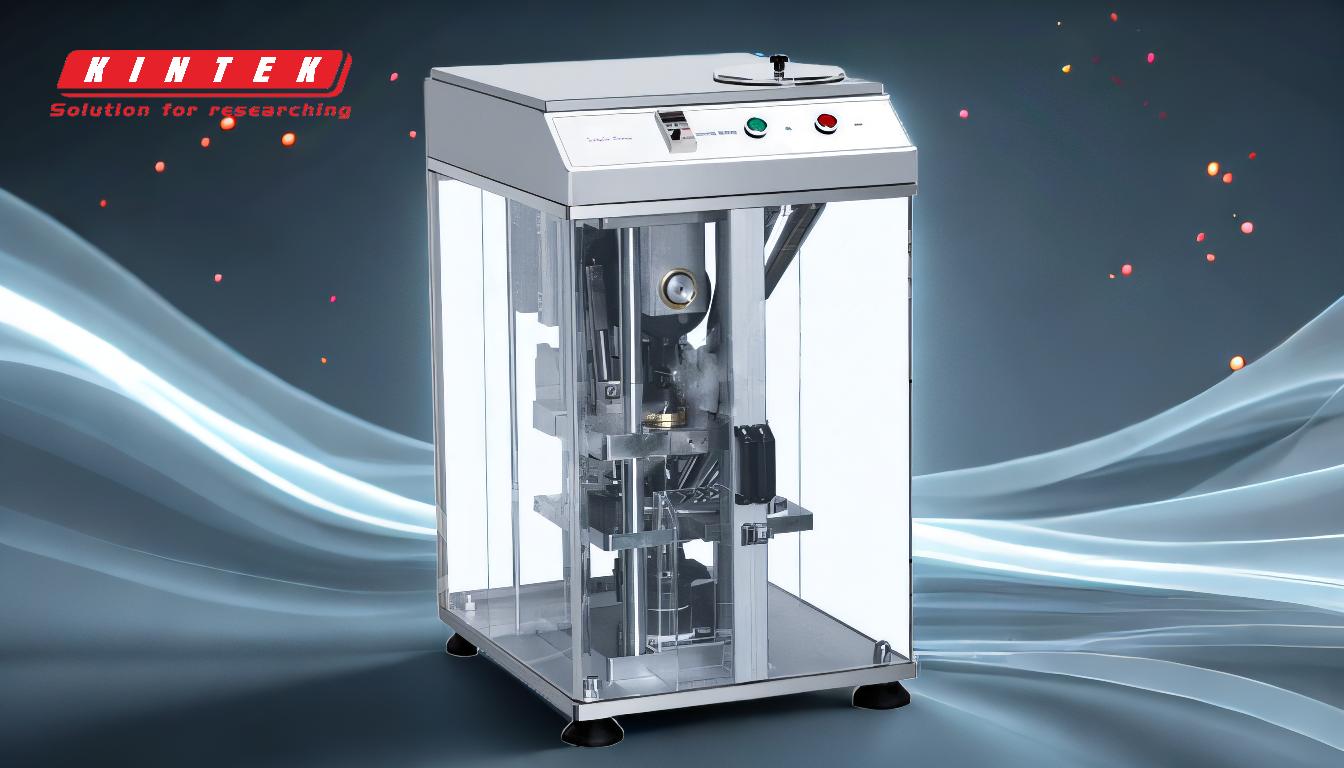
-
Fundamentals of Magnetron Sputtering:
- Magnetron sputtering is a PVD process where a target material is bombarded with ions in a vacuum environment, causing atoms to be ejected and deposited as a thin film onto a substrate.
- It is known for its high deposition rates, low substrate temperatures, and ability to produce uniform and high-quality coatings.
-
Applications in Electronics:
- Used to manufacture gate dielectrics, passive thin-film components, and interlayer dielectrics.
- Enhances the durability of electronic parts, such as printed circuit boards and surface acoustic wave devices.
- Enables the production of sensors and other microelectronic components.
-
Optical Applications:
- Produces anti-reflective coatings for displays, lenses, and optical filters.
- Used in laser lenses, achromatic lenses, and spectroscopy equipment.
- Enhances transmission, reflection, and polarization properties in optical devices.
-
Defense and Aerospace Applications:
- Manufactures night vision equipment and mirrors for x-ray telescopes.
- Deposits corrosion-resistant and wear-resistant coatings on aerospace components.
- Used in the production of superconductor materials and magnesium alloys for lightweight, high-strength applications.
-
Medical and Dental Applications:
- Creates anti-rejection coatings for medical devices to prevent allergic reactions.
- Used in the manufacture of angioplasty devices, radiation capsules, and dental implants.
- Ensures biocompatibility and durability in medical applications.
-
Renewable Energy and Solar Technology:
- Deposits thin-film layers for solar cells, improving efficiency and durability.
- Used in thin-film batteries and LED lighting.
- Applies barrier layers for OLEDs and solar control coatings on glass.
-
Industrial and Manufacturing Applications:
- Produces wear-resistant, low-friction, and corrosion-resistant coatings for machine parts.
- Used in the machining industry for decorative and functional coatings.
- Deposits thin films for tools, architectural glass, and photovoltaic materials.
-
Advantages of Magnetron Sputtering:
- High deposition rates and precise control over film thickness.
- Low-temperature process suitable for heat-sensitive substrates.
- Ability to deposit a wide range of materials, including metals, alloys, and ceramics.
Magnetron sputtering is a critical technology in modern manufacturing and research, enabling the development of advanced materials and devices across diverse industries. Its ability to produce high-quality, functional thin films with specific properties makes it an essential tool for innovation and industrial progress.
Summary Table:
Industry | Applications |
---|---|
Electronics | Gate dielectrics, sensors, durable electronic components |
Optics | Anti-reflective coatings, laser lenses, spectroscopy equipment |
Defense & Aerospace | Night vision equipment, corrosion-resistant coatings, superconductor materials |
Medical & Dental | Anti-rejection coatings, angioplasty devices, dental implants |
Renewable Energy | Solar cells, thin-film batteries, LED lighting |
Manufacturing | Wear-resistant coatings, decorative films, photovoltaic materials |
Unlock the potential of magnetron sputtering for your industry—contact our experts today!