Chemical Vapor Deposition (CVD) is a widely used technique in materials science and engineering for depositing thin films or coatings on substrates. It involves the use of gaseous precursors that react or decompose at high temperatures to form a solid material on the substrate surface. CVD is versatile, scalable, and capable of producing high-purity, uniform coatings. It has applications in various fields, including semiconductor manufacturing, diamond film synthesis, and graphene production. The process can be enhanced using plasma, such as in microwave plasma chemical vapor deposition (MPCVD), which allows for lower deposition temperatures and better control over material properties.
Key Points Explained:
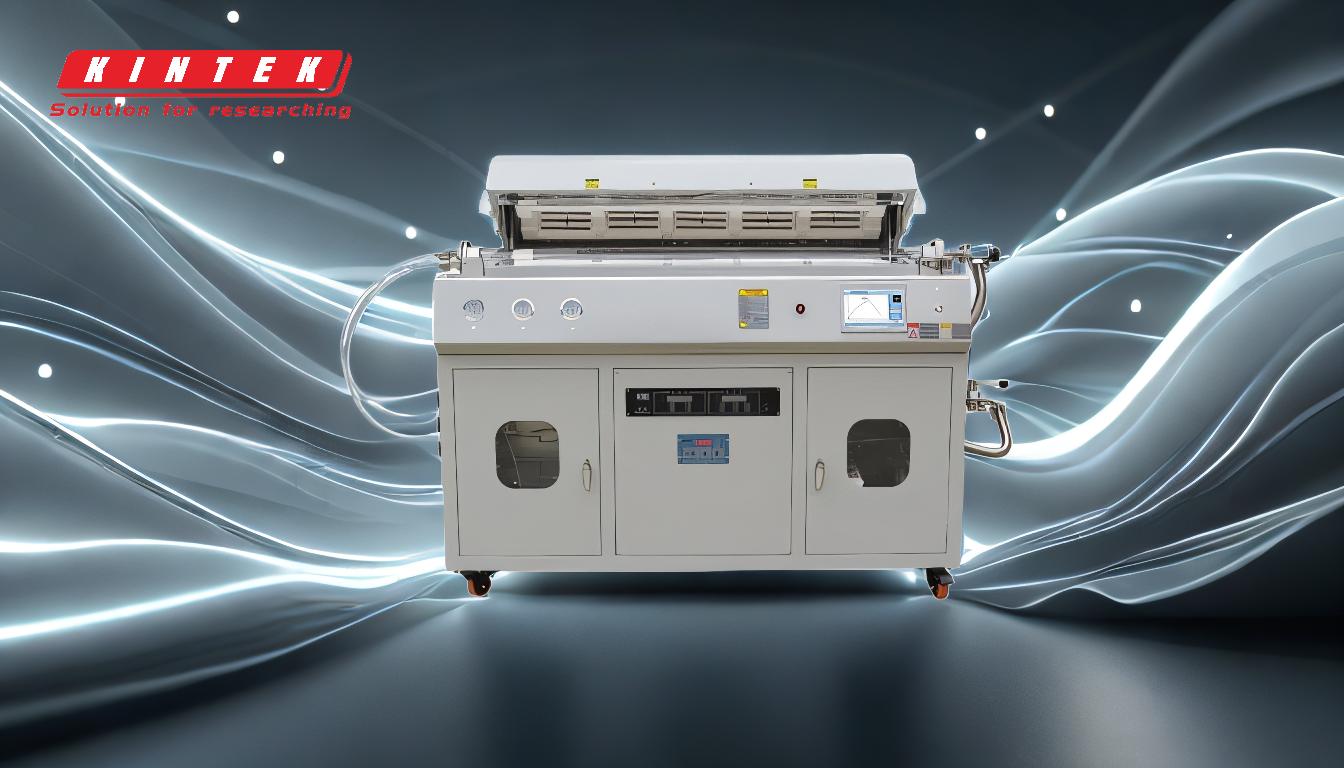
-
Definition of Chemical Vapor Deposition (CVD):
- CVD is a process where gaseous precursors are introduced into a chamber and react or decompose at high temperatures to form a solid material on a substrate. This method is widely used for depositing thin films or coatings with high purity and uniformity.
-
Process Mechanism:
- The process involves injecting a volatile precursor gas into a chamber under vacuum or controlled atmosphere. The gas is then heated to a reaction temperature, causing it to decompose or react, forming the desired coating material. This material bonds to the substrate surface, building up evenly over time.
-
Temperature and Pressure Conditions:
- CVD typically operates at high temperatures, often above 500°C, and can be performed at subatmospheric pressures. These conditions facilitate the decomposition of precursor gases and the deposition of the coating material.
-
Types of CVD:
- Thermal CVD: Uses heat to initiate the chemical reaction.
- Plasma-Enhanced CVD (PECVD): Utilizes plasma to excite the precursor gases, allowing deposition at lower temperatures.
- Microwave Plasma CVD (MPCVD): A specialized form of PECVD that uses microwave energy to generate plasma, enabling precise control over the deposition process and producing high-quality materials like diamonds.
-
Advantages of CVD:
- High Purity and Uniformity: CVD can produce coatings with excellent purity and uniformity, making it suitable for applications requiring precise material properties.
- Versatility: It can deposit a wide range of materials, including metals, ceramics, and polymers, on various substrates.
- Scalability: CVD processes can be scaled up for industrial production, making it a cost-effective method for large-scale manufacturing.
-
Applications of CVD:
- Semiconductor Industry: CVD is used to deposit thin films of silicon, silicon dioxide, and other materials in the fabrication of integrated circuits.
- Diamond Synthesis: CVD, particularly microwave plasma chemical vapor deposition, is used to produce synthetic diamonds for industrial and gemstone applications.
- Graphene Production: CVD is a leading method for producing large-area, high-quality graphene, which has applications in electronics, energy storage, and composites.
- Protective Coatings: CVD is used to apply wear-resistant, hard, and oxidation-resistant coatings on tools, automotive parts, and other components.
-
Comparison with Other Deposition Techniques:
- CVD vs. PVD (Physical Vapor Deposition): While PVD involves the physical transfer of material from a source to a substrate, CVD relies on chemical reactions. CVD generally offers better step coverage and can deposit more complex materials.
- CVD vs. Sputtering and Evaporation: CVD provides better film uniformity and purity compared to sputtering and evaporation techniques, which are more limited in terms of material options and scalability.
-
Future Prospects:
- CVD continues to evolve with advancements in precursor chemistry, reactor design, and process control. The development of new CVD techniques, such as atomic layer deposition (ALD) and hybrid CVD-PVD methods, is expanding the range of applications and improving the quality of deposited materials.
In summary, Chemical Vapor Deposition is a powerful and versatile technique for depositing thin films and coatings with high purity and uniformity. Its ability to operate at high temperatures and subatmospheric pressures, combined with the use of plasma enhancement, makes it suitable for a wide range of applications, from semiconductor manufacturing to diamond synthesis and graphene production. The continuous advancements in CVD technology promise even broader applications and improved material properties in the future.
Summary Table:
Aspect | Details |
---|---|
Definition | CVD uses gaseous precursors to form solid coatings on substrates. |
Process Mechanism | Precursor gases decompose at high temperatures, bonding to the substrate. |
Temperature Range | Typically above 500°C, often under subatmospheric pressure. |
Types of CVD | Thermal CVD, Plasma-Enhanced CVD (PECVD), Microwave Plasma CVD (MPCVD). |
Advantages | High purity, uniformity, versatility, and scalability. |
Applications | Semiconductors, diamond synthesis, graphene production, protective coatings. |
Comparison with PVD | CVD offers better step coverage and material complexity than PVD. |
Future Prospects | Advancements in ALD and hybrid CVD-PVD methods expand applications. |
Discover how CVD can revolutionize your material processes—contact our experts today!