Vapour deposition is a process used to create thin films or coatings on solid surfaces by transforming a material into a gaseous or vapor state and then depositing it onto a substrate. This technique is widely used in industries to produce coatings with precise thickness, uniformity, and purity. The process typically occurs in a vacuum or low-pressure environment to minimize contamination and ensure controlled deposition. Vapour deposition can involve thermal, chemical, or plasma-based methods, depending on the material and application. The resulting coatings can range from a few nanometers to millimeters in thickness, making it a versatile technology for applications in electronics, optics, and surface engineering.
Key Points Explained:
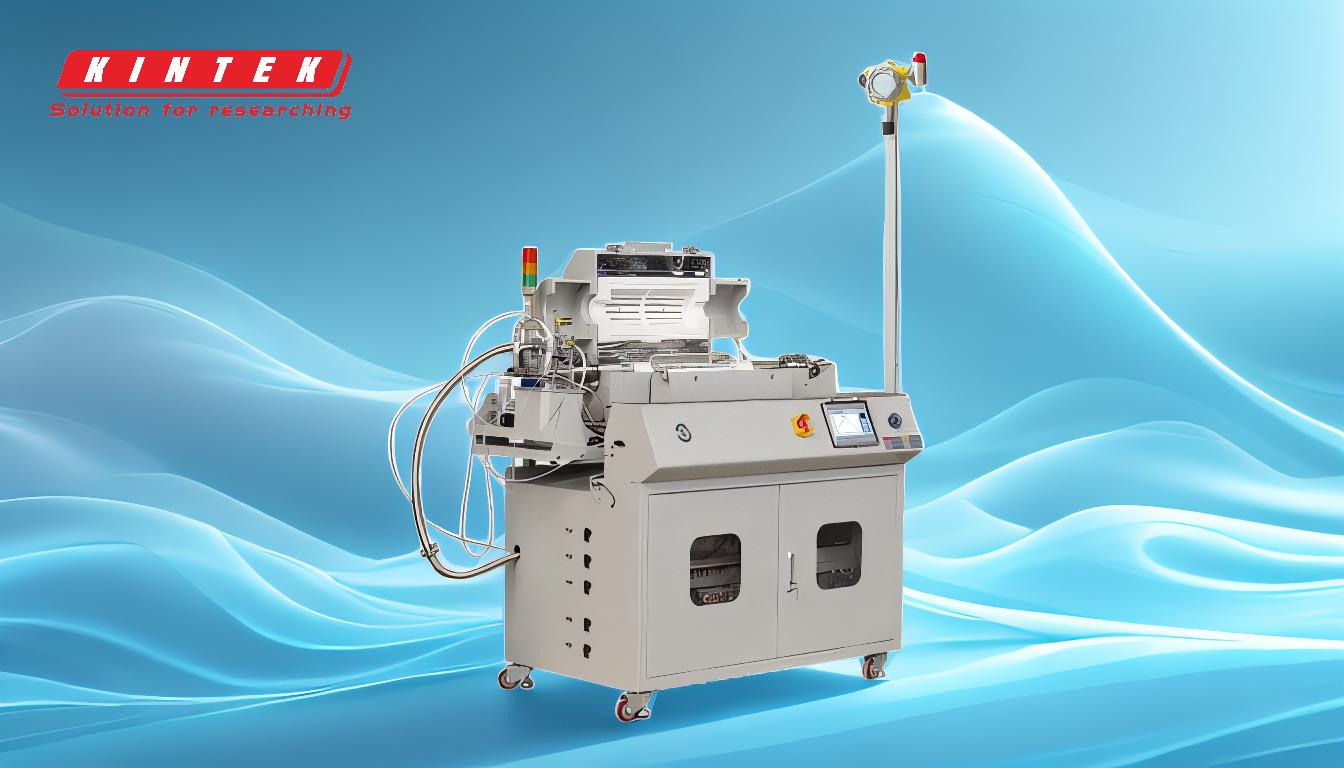
-
Definition and Purpose of Vapour Deposition:
- Vapour deposition is a process where a material is transformed into a gaseous or vapor state and then deposited onto a substrate to form a thin film or coating.
- The primary purpose is to create coatings with controlled thickness, uniformity, and purity, often used in industries like electronics, optics, and surface engineering.
-
Types of Vapour Deposition:
- Thermal Vapour Deposition: Involves heating a solid material in a high vacuum chamber to produce vapor pressure. The material is heated to temperatures between 250 to 350 degrees Celsius, turning it into a vapor that coats the substrate.
- Chemical Vapour Deposition (CVD): Uses chemical reactions to produce a vapor that deposits onto the substrate. This method is often used for creating high-purity and high-performance coatings.
- Plasma-Enhanced Vapour Deposition: Utilizes plasma to energize the gas or vapor, enhancing the deposition process and allowing for lower temperature operations.
-
Process Environment:
- Vapour deposition typically occurs in a vacuum or low-pressure environment to minimize the presence of gas molecules that could interfere with the deposition process.
- The vacuum environment ensures a clean and controlled deposition, allowing for precise control over the thickness and quality of the coating.
-
Material Transformation:
- The source material is heated or energized to transform it from a solid or liquid state into a vapor or gas.
- In thermal vapour deposition, an electric heater is often used to heat the material until it vaporizes.
- The vaporized material then travels through the vacuum chamber and deposits onto the substrate.
-
Deposition Mechanism:
- The vaporized material spreads out evenly in the vacuum chamber, creating a uniform coating on the substrate.
- The deposition occurs at the atomic or molecular level, allowing for extremely thin and precise coatings, often in the nanometer range.
-
Applications of Vapour Deposition:
- Electronics: Used to create thin films for semiconductors, integrated circuits, and other electronic components.
- Optics: Applied in the production of anti-reflective coatings, mirrors, and optical filters.
- Surface Engineering: Used to enhance the durability, corrosion resistance, and aesthetic properties of materials.
-
Advantages of Vapour Deposition:
- Precision: Allows for the creation of coatings with precise thickness and uniformity.
- Purity: The vacuum environment minimizes contamination, resulting in high-purity coatings.
- Versatility: Can be used with a wide range of materials, including metals, semiconductors, and ceramics.
-
Equipment and Systems:
- Vapour deposition systems typically consist of a vacuum chamber, a heat source, and a substrate holder.
- These systems are designed to control the temperature, pressure, and deposition rate to achieve the desired coating properties.
-
Challenges and Considerations:
- Cost: The equipment and process can be expensive, particularly for high-vacuum systems.
- Complexity: The process requires precise control over various parameters, making it complex and requiring skilled operators.
- Material Limitations: Not all materials are suitable for vapour deposition, and some may require specific conditions or modifications.
-
Future Trends:
- Nanotechnology: Increasing use of vapour deposition in nanotechnology for creating ultra-thin films and nanostructures.
- Sustainability: Development of more energy-efficient and environmentally friendly vapour deposition processes.
- Advanced Materials: Exploration of new materials and composites that can be deposited using vapour deposition techniques.
In summary, vapour deposition is a highly versatile and precise technology used to create thin films and coatings on solid surfaces. It involves transforming a material into a vapor or gas and depositing it onto a substrate in a controlled environment. The process offers numerous advantages, including precision, purity, and versatility, making it essential in various industries. However, it also presents challenges such as cost and complexity, which are areas of ongoing research and development.
Summary Table:
Aspect | Details |
---|---|
Definition | Process of transforming materials into vapor for thin film deposition. |
Types | Thermal, Chemical (CVD), Plasma-Enhanced. |
Environment | Vacuum or low-pressure to minimize contamination. |
Applications | Electronics, optics, surface engineering. |
Advantages | Precision, purity, versatility. |
Challenges | High cost, complexity, material limitations. |
Future Trends | Nanotechnology, sustainability, advanced materials. |
Discover how vapour deposition can elevate your projects—contact our experts today!