Physical Vapor Deposition (PVD) stainless steel refers to stainless steel that has undergone a specialized coating process to enhance its properties. PVD is a vacuum-based deposition method where a solid material is vaporized and then condensed onto the stainless steel surface to form a thin, durable film. This process improves the steel's corrosion resistance, wear resistance, and aesthetic appeal, offering a wide range of colors and finishes. PVD coatings are environmentally friendly, highly durable, and provide excellent adhesion to the substrate. They are commonly used in industries like aerospace, automotive, and biomedical instruments due to their ability to create high-quality, functional, and decorative coatings.
Key Points Explained:
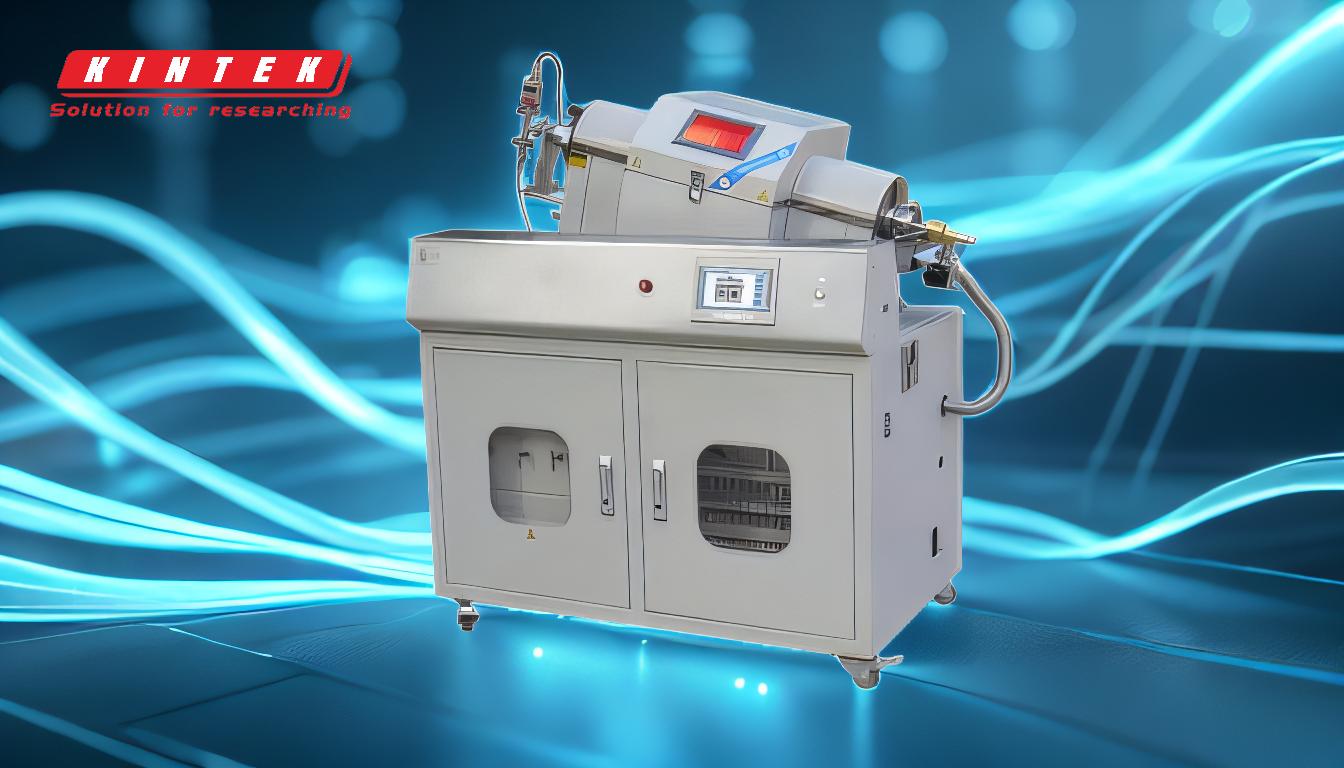
-
Definition of PVD Coating:
- PVD stands for Physical Vapor Deposition, a vacuum-based process used to apply thin films to materials like stainless steel.
- The process involves converting a solid material into vapor, transporting it in a vacuum, and condensing it onto the substrate to form a coating.
-
Process of PVD Coating:
- Step 1: Vaporization: The coating material (e.g., titanium, chromium, or gold) is vaporized using physical methods like sputtering or evaporation.
- Step 2: Transportation: The vaporized material is transported through a low-pressure environment to the stainless steel substrate.
- Step 3: Condensation: The vapor condenses on the stainless steel surface, forming a thin, uniform film.
-
Benefits of PVD Coating on Stainless Steel:
- Corrosion Resistance: PVD coatings significantly enhance the stainless steel's ability to resist corrosion and staining.
- Wear Resistance: The coatings are highly durable, making the steel more resistant to scratches and wear.
- Aesthetic Appeal: PVD allows for a wide range of colors and finishes, making it ideal for decorative applications.
- Adhesion: PVD coatings bond exceptionally well to stainless steel, ensuring long-lasting performance.
- Environmental Friendliness: The process is eco-friendly, as it does not involve harmful chemicals or produce toxic waste.
-
Applications of PVD-Coated Stainless Steel:
- Aerospace: Used for components requiring high durability and corrosion resistance.
- Automotive: Enhances the appearance and longevity of parts like trim and wheels.
- Biomedical Instruments: Provides biocompatible and wear-resistant coatings for surgical tools.
- Optics and Firearms: Improves performance and aesthetics of precision components.
-
Comparison to Other Coating Methods:
- PVD coatings are more robust and consistent than other methods like electroplating or chemical vapor deposition (CVD).
- They offer a wider operating window and produce higher-quality coatings with better adhesion and durability.
-
Technical Advantages:
- Thickness Control: PVD coatings are extremely thin, replicating the original finish without altering the substrate's dimensions.
- Multilayered Coatings: The process can create complex, multilayered coatings for enhanced performance.
- Adjustable Properties: Mechanical and aesthetic properties can be tailored to meet specific requirements.
-
Why Choose PVD for Stainless Steel?:
- PVD-coated stainless steel is ideal for applications requiring both functional and decorative properties.
- The process enhances the steel's lifespan, making it a cost-effective solution for high-performance applications.
By understanding these key points, it becomes clear why PVD-coated stainless steel is a preferred choice in industries demanding durability, aesthetics, and environmental sustainability.
Summary Table:
Aspect | Details |
---|---|
Definition | PVD (Physical Vapor Deposition) applies thin, durable coatings to stainless steel. |
Process | Vaporization → Transportation → Condensation to form a uniform film. |
Benefits | Corrosion resistance, wear resistance, aesthetic appeal, eco-friendly. |
Applications | Aerospace, automotive, biomedical instruments, optics, firearms. |
Advantages | Thin coatings, multilayered options, adjustable properties, high durability. |
Enhance your materials with PVD-coated stainless steel—contact us today to learn more!