Physical Vapor Deposition (PVD) is a sophisticated method used to create thin films and coatings of nanomaterials. It involves converting a solid target material into a vapor phase, which then condenses onto a substrate to form a thin, durable, and high-quality coating. PVD is widely used in industries requiring precise, high-performance coatings, such as electronics, optics, and aerospace. The process is divided into sub-methods like sputtering and evaporation, each offering unique advantages in terms of material compatibility, adhesion, and film quality. PVD is particularly valued for its ability to handle materials with high melting points and produce coatings with excellent corrosion resistance and thermal stability.
Key Points Explained:
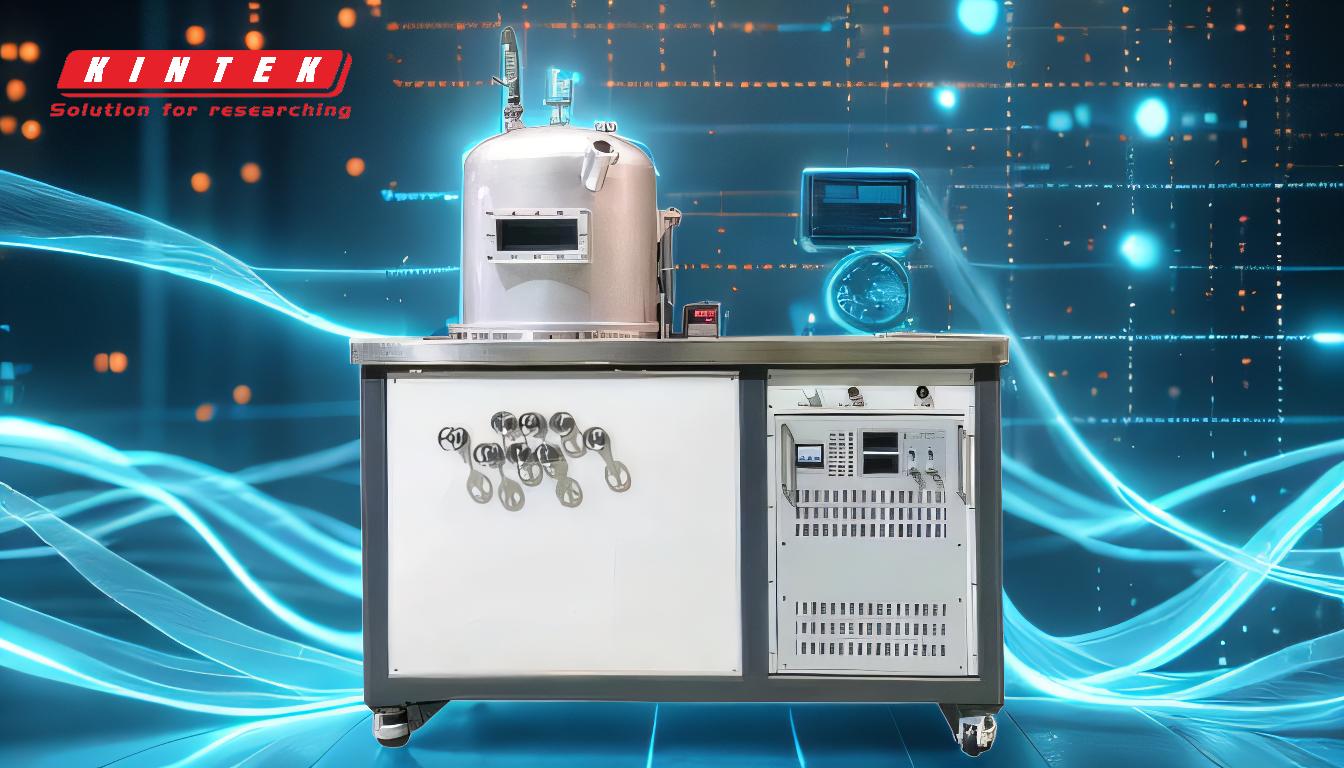
-
Basic Principle of PVD:
- PVD involves the transition of a solid material into a vapor phase, which is then deposited onto a substrate.
- The process typically occurs in a low-pressure chamber to minimize interference from background gases.
- The vaporized material travels through the chamber and condenses on the substrate, forming a thin film.
-
Key Steps in the PVD Process:
- Vaporization: The solid target material is converted into a vapor phase using methods such as thermal evaporation, sputtering, or laser ablation.
- Transport: The vaporized atoms or molecules travel through the reaction chamber.
- Deposition: The vapor condenses onto the substrate, forming a thin film or coating.
-
Sub-Methods of PVD:
- Sputtering: Involves bombarding the target material with high-energy ions to dislodge atoms, which then deposit onto the substrate. This method is suitable for a wide range of materials and produces films with excellent adhesion.
- Evaporation: The target material is heated until it evaporates, and the vapor condenses onto the substrate. This method is ideal for materials with high melting points and produces high-purity films.
- Thermal Evaporation: A specific type of evaporation where the target material is heated using resistive or electron beam heating.
- Laser Ablation: Uses a high-power laser to vaporize the target material, often used for complex or multi-component materials.
-
Advantages of PVD:
- High-Quality Coatings: PVD produces thin films with excellent adhesion, uniformity, and density.
- Material Versatility: PVD can handle materials with high melting points and is compatible with a wide range of substrates.
- Durability: Coatings produced by PVD are highly durable, corrosion-resistant, and capable of withstanding high temperatures.
- Precision: The process allows for precise control over film thickness and composition, often monitored using quartz crystal rate monitors.
-
Applications of PVD:
- Electronics: Used for depositing conductive and insulating layers in semiconductor devices.
- Optics: Produces anti-reflective and protective coatings for lenses and mirrors.
- Aerospace: Creates wear-resistant and thermal barrier coatings for engine components.
- Medical Devices: Provides biocompatible and corrosion-resistant coatings for implants and surgical tools.
-
Comparison with Chemical Vapor Deposition (CVD):
- PVD is a physical process, whereas CVD involves chemical reactions to deposit materials.
- PVD generally operates at lower temperatures, making it suitable for heat-sensitive substrates.
- PVD coatings tend to have better adhesion and are more environmentally friendly due to the absence of chemical byproducts.
-
Challenges and Considerations:
- Line-of-Sight Limitation: PVD is a line-of-sight process, meaning it may not coat complex geometries uniformly.
- Cost: The equipment and energy requirements for PVD can be expensive.
- Process Control: Achieving consistent film quality requires precise control over parameters like pressure, temperature, and deposition rate.
-
Future Trends in PVD:
- Hybrid Processes: Combining PVD with other techniques like CVD to enhance coating properties.
- Nanostructured Coatings: Developing advanced nanomaterials with tailored properties for specific applications.
- Sustainability: Reducing energy consumption and waste in PVD processes to make them more environmentally friendly.
In summary, Physical Vapor Deposition is a versatile and precise method for creating high-quality thin films and coatings. Its ability to handle a wide range of materials, produce durable and high-performance coatings, and operate at relatively low temperatures makes it a valuable technique in various industries. However, challenges such as line-of-sight limitations and cost must be addressed to further expand its applications.
Summary Table:
Aspect | Details |
---|---|
Basic Principle | Converts solid material into vapor, condensing it onto a substrate. |
Key Steps | Vaporization, Transport, Deposition. |
Sub-Methods | Sputtering, Evaporation, Thermal Evaporation, Laser Ablation. |
Advantages | High-quality coatings, material versatility, durability, precision. |
Applications | Electronics, optics, aerospace, medical devices. |
Challenges | Line-of-sight limitation, cost, process control. |
Future Trends | Hybrid processes, nanostructured coatings, sustainability improvements. |
Ready to enhance your materials with PVD coatings? Contact our experts today to learn more!