Physical Vapor Deposition (PVD) is a set of techniques used to deposit thin films of material onto a substrate. It involves the physical transfer of material from a source to a substrate in a vacuum environment. PVD is widely used in various industries for applications such as improving surface properties like hardness, wear resistance, and oxidation resistance. The primary methods of PVD include thermal evaporation, sputtering, and electron-beam evaporation. These techniques are essential for creating coatings with specific properties tailored to industrial needs, such as decorative coatings, tribological coatings, and functional coatings for tools and automotive parts.
Key Points Explained:
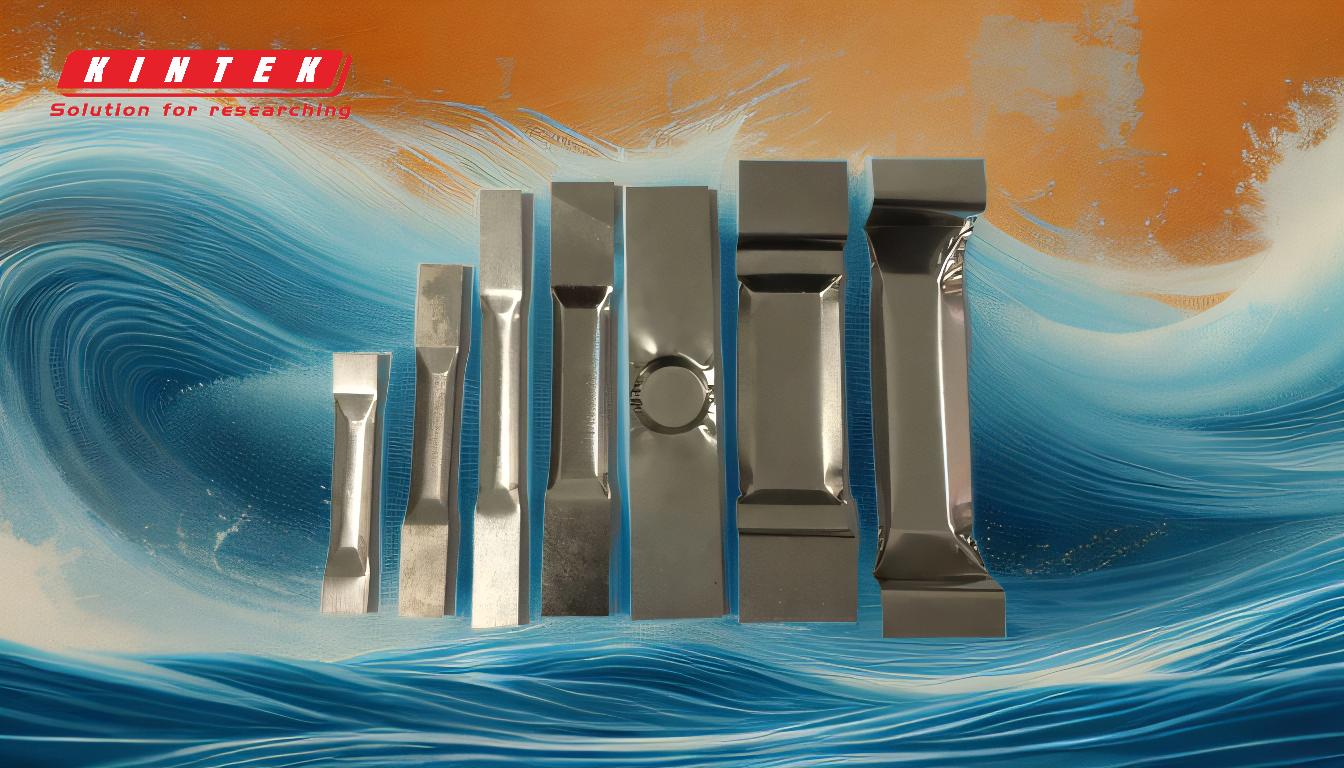
-
Definition and Purpose of PVD:
- PVD is a process where materials are physically transferred from a source to a substrate in a vacuum environment.
- It is used to create thin films with specific properties like wear resistance, hardness, and oxidation resistance.
- Common applications include decorative coatings, tribological coatings for automotive parts, and functional coatings for tools.
-
Primary Methods of PVD:
- Thermal Evaporation: This method involves heating the source material in a vacuum until it vaporizes. The vapor then condenses on the substrate to form a thin film.
- Sputtering: In this technique, a plasma is generated, and ions (usually argon) bombard the source material, causing it to eject atoms that deposit onto the substrate.
- Electron-Beam Evaporation (E-Beam Evaporation): This method uses a focused electron beam to heat and vaporize the source material, which then deposits onto the substrate.
-
Applications of PVD:
- Decorative Coatings: PVD is widely used for coating jewelry, door and window hardware, lamps, and handicrafts to enhance their appearance and durability.
- Tribological Coatings: These coatings are applied to automotive parts, cutting tools, and forming tools to reduce friction and improve wear resistance.
- Functional Coatings: PVD is used to coat glass surfaces for thermo-optical properties and in innovative projects in new markets.
-
Advantages of PVD:
- Enhanced Surface Properties: PVD coatings improve hardness, wear resistance, and oxidation resistance of substrates.
- Versatility: PVD can be used with a wide range of materials and substrates, making it suitable for various industries.
- High-Quality Coatings: The vacuum environment ensures that the coatings are free from contaminants and have excellent adhesion to the substrate.
-
Comparison with Chemical Vapor Deposition (CVD):
- Process Differences: PVD involves physical transfer of material, while CVD involves chemical reactions to deposit material on the substrate.
- Operating Conditions: PVD typically operates in a vacuum, whereas CVD can operate at atmospheric or low pressures.
- Material Suitability: PVD is more suitable for metals and alloys, while CVD is often used for depositing compounds like oxides, nitrides, and carbides.
-
Industrial Relevance:
- PVD technology is crucial in industries like automotive, aerospace, electronics, and decorative hardware.
- Leading manufacturers are continuously developing PVD products for mass production, making it a key technology in modern manufacturing.
By understanding these key points, one can appreciate the versatility and importance of PVD techniques in modern industrial applications. Whether for enhancing the durability of tools or improving the aesthetic appeal of decorative items, PVD offers a reliable and effective solution for a wide range of coating needs.
Summary Table:
Aspect | Details |
---|---|
Definition | Physical transfer of material in a vacuum to create thin films. |
Primary Methods | Thermal Evaporation, Sputtering, Electron-Beam Evaporation. |
Applications | Decorative, Tribological, and Functional Coatings. |
Advantages | Enhanced hardness, wear resistance, oxidation resistance, and versatility. |
Comparison with CVD | PVD uses physical transfer; CVD uses chemical reactions. |
Industrial Relevance | Automotive, aerospace, electronics, and decorative hardware industries. |
Interested in learning how PVD can benefit your industry? Contact us today for expert advice!