Plasma-assisted deposition techniques are advanced methods used to deposit thin films on substrates by utilizing plasma to activate chemical reactions or liberate atoms from a target material. These techniques, such as Plasma-Enhanced Chemical Vapor Deposition (PECVD), operate at relatively low temperatures (around 200 °C), making them suitable for temperature-sensitive substrates. They offer numerous advantages, including uniform film thickness, dense film structure, strong adhesion, and versatility in depositing various materials like metals, inorganic compounds, and organic films. These methods are scalable for industrial applications and provide energy-efficient, cost-effective solutions for producing high-quality thin films with excellent physical properties, such as hardness and scratch resistance.
Key Points Explained:
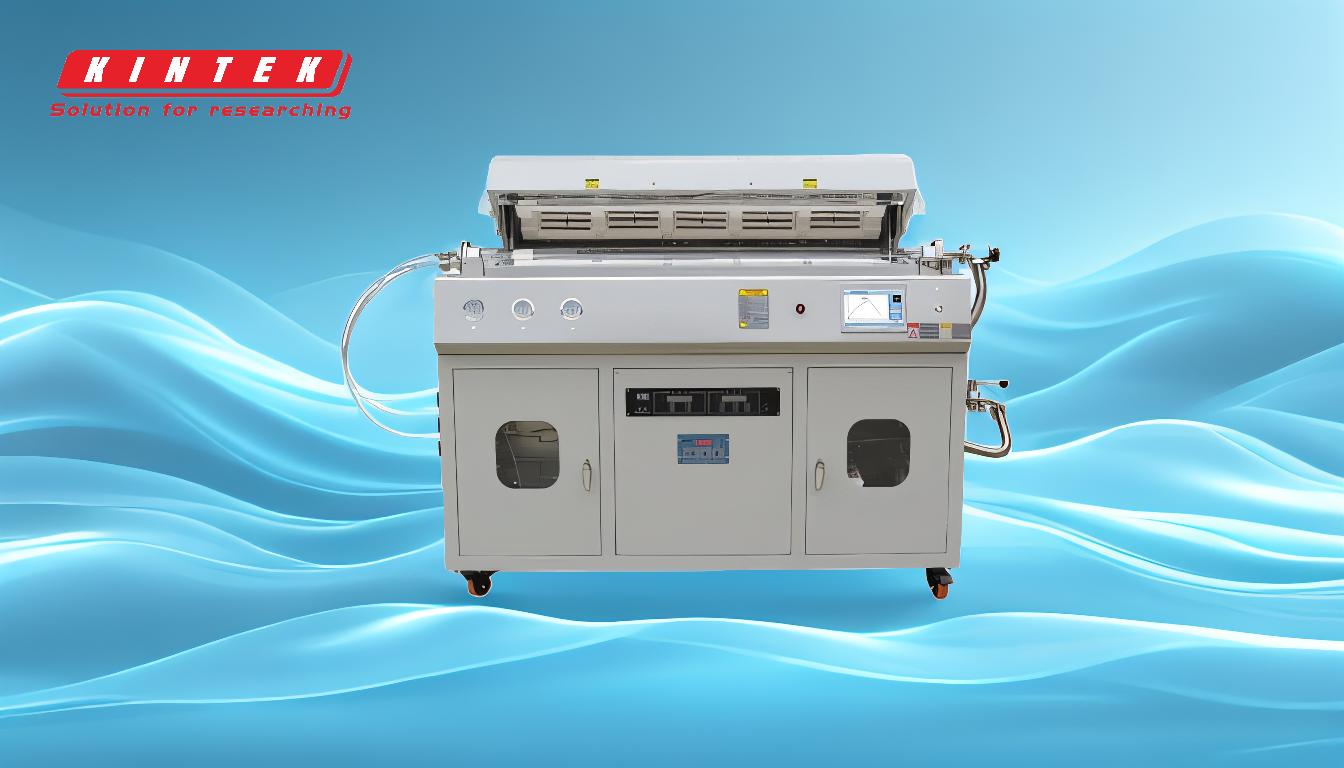
-
Definition and Mechanism of Plasma-Assisted Deposition:
- Plasma-assisted deposition techniques involve the use of plasma to activate chemical reactions or liberate atoms from a target material.
- In methods like Plasma-Enhanced Chemical Vapor Deposition (PECVD), plasma excites and ionizes gas-phase precursors, enabling deposition at low temperatures (as low as 200 °C).
- High-energy charged particles in the plasma liberate neutral atoms from the target material, which then deposit onto the substrate to form a thin film.
-
Types of Plasma-Assisted Deposition Techniques:
- Plasma-Enhanced Chemical Vapor Deposition (PECVD): Uses plasma to activate chemical reactions at low temperatures.
- Microwave Plasma CVD: Utilizes microwave energy to generate plasma.
- Remote Plasma-Enhanced CVD: Plasma is generated remotely from the substrate to minimize damage.
- Low-Energy Plasma-Enhanced CVD: Operates with lower energy levels to reduce substrate impact.
- Atomic Layer CVD: Deposits films layer by layer with atomic precision.
- Combustion CVD: Combines combustion processes with plasma activation.
- Hot Filament CVD: Uses a heated filament to generate plasma.
-
Advantages of Plasma-Assisted Deposition:
- Low Deposition Temperature: Suitable for temperature-sensitive substrates, preserving their structural and physical properties.
- Uniform Film Thickness and Composition: Ensures consistent film quality across large substrate areas.
- Dense Film Structure: Produces films with minimal pinholes, enhancing durability and performance.
- Strong Adhesion: Films adhere well to substrates, improving longevity.
- Versatility: Capable of depositing a wide range of materials, including metals, inorganic compounds, and organic films.
- Scalability: Suitable for industrial-scale applications with the potential for high throughput.
-
Applications of Plasma-Assisted Deposition:
- Microelectronics: Used for shallow bath isolation filling, sidewall isolation, and metal-linked media isolation.
- Optical Coatings: Produces films with excellent optical properties for lenses and mirrors.
- Protective Coatings: Creates hard, scratch-resistant coatings for tools and components.
- Biomedical Devices: Deposits biocompatible films for medical implants and devices.
- Energy Storage: Used in the fabrication of thin-film batteries and supercapacitors.
-
Operational Benefits:
- Energy Efficiency: Low reaction temperatures reduce energy consumption.
- Cost Reduction: Lower operational costs due to reduced energy and material usage.
- High Throughput: Enables rapid deposition rates, increasing production efficiency.
- Controllability: Precise control over film thickness, down to a few nanometers, and composition.
-
Physical Properties of Deposited Films:
- Hardness and Scratch Resistance: Films exhibit outstanding mechanical properties, making them suitable for demanding applications.
- Thickness Control: Ability to deposit ultra-thin films with precise thickness control.
- Purity and Density: High-purity, dense films with minimal defects enhance performance and reliability.
-
Industrial Scale-Up:
- Plasma-assisted deposition methods are scalable for industrial applications, with the potential for using more powerful reactors to increase production capacity.
- Uniform film deposition over larger substrate areas makes these techniques suitable for mass production.
In summary, plasma-assisted deposition techniques are versatile, efficient, and scalable methods for producing high-quality thin films with excellent physical properties. Their low-temperature operation, uniform deposition, and strong adhesion make them ideal for a wide range of applications in microelectronics, optics, protective coatings, and biomedical devices.
Summary Table:
Aspect | Details |
---|---|
Definition | Uses plasma to activate chemical reactions or liberate atoms for deposition. |
Key Techniques | PECVD, Microwave Plasma CVD, Remote Plasma-Enhanced CVD, Atomic Layer CVD. |
Advantages | Low temperature, uniform thickness, strong adhesion, scalability. |
Applications | Microelectronics, optical coatings, biomedical devices, energy storage. |
Operational Benefits | Energy-efficient, cost-effective, high throughput, precise control. |
Physical Properties | Hardness, scratch resistance, ultra-thin films, high purity. |
Unlock the potential of plasma-assisted deposition for your projects—contact us today to learn more!