Plasma in RF sputtering is a partially ionized gas that plays a critical role in the deposition of thin films, particularly for non-conductive or low-conductivity materials. It is sustained by alternating current at a high radio frequency, which generates kinetic energy by accelerating and reversing electrons within the plasma. This process allows the plasma to operate at lower pressures compared to conventional methods like Magnetron Sputtering, as it does not rely on trapping secondary ions above the target material. Plasma's unique properties, such as responsiveness to electromagnetic fields and high kinetic energy, make it indispensable for achieving precise and pure thin film deposition at the atomic level.
Key Points Explained:
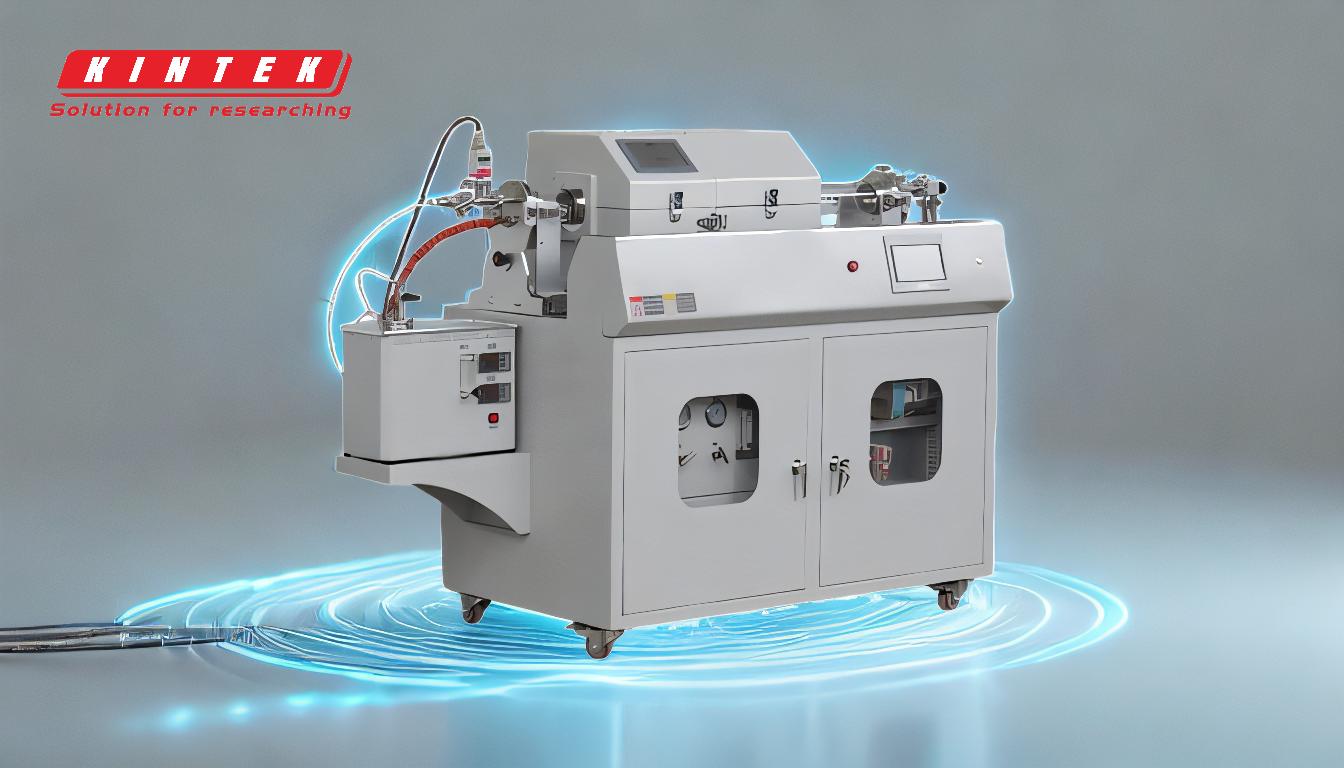
-
Definition of Plasma in RF Sputtering:
- Plasma is a partially ionized gas, often referred to as the fourth state of matter, consisting of free electrons, ions, and neutral atoms or molecules.
- In RF sputtering, plasma is sustained by applying a high-frequency alternating current, typically in the radio frequency (RF) range (e.g., 13.56 MHz).
- The alternating current causes electrons to oscillate and gain kinetic energy, which is essential for maintaining the plasma state.
-
Role of Plasma in RF Sputtering:
- Plasma provides the high kinetic energy required to dislodge atoms from the target material, a process known as sputtering.
- The energy from the plasma is much higher than normal thermal energies, enabling precise and pure thin film deposition at the atomic level.
- This high-energy environment is particularly advantageous for depositing thin films on temperature-sensitive substrates, as it allows for low-temperature processing.
-
Advantages of RF Plasma Over DC Plasma:
- RF sputtering is particularly useful for non-conductive or low-conductivity target materials, which cannot be effectively sputtered using a DC power source.
- The alternating current in RF sputtering prevents charge buildup on the target surface, a common issue with DC sputtering for insulating materials.
- RF plasma can be sustained at much lower pressures compared to DC plasma, reducing the need for secondary ion trapping and improving process efficiency.
-
Kinetic Energy Generation in RF Plasma:
- The alternating current in RF sputtering accelerates electrons back and forth, generating kinetic energy.
- This kinetic energy is transferred to the gas atoms in the plasma, ionizing them and sustaining the plasma state.
- The process is highly efficient and allows for precise control over the deposition process, making it ideal for applications requiring high-quality thin films.
-
Comparison with Conventional Magnetron Sputtering:
- In conventional Magnetron Sputtering, plasma is sustained by trapping secondary ions above the target material, which requires higher pressures.
- RF sputtering, on the other hand, does not rely on this trapping mechanism, allowing it to operate at lower pressures and with greater efficiency.
- This difference makes RF sputtering more suitable for depositing thin films on delicate or temperature-sensitive substrates.
-
Applications of RF Sputtering Plasma:
- RF sputtering is widely used in the semiconductor industry for depositing thin films of insulating materials, such as oxides and nitrides.
- It is also used in the production of optical coatings, solar cells, and other advanced materials where precise control over film properties is essential.
- The ability to deposit thin films at low temperatures makes RF sputtering a preferred method for applications involving temperature-sensitive materials.
By understanding these key points, one can appreciate the critical role that plasma plays in RF sputtering and its advantages over other sputtering methods. This knowledge is particularly valuable for equipment and consumable purchasers, as it highlights the importance of selecting the right sputtering technology for specific applications.
Summary Table:
Aspect | Details |
---|---|
Definition | Partially ionized gas maintained by high-frequency alternating current. |
Role | Provides high kinetic energy for sputtering atoms from the target material. |
Advantages Over DC Plasma | Works with non-conductive materials, prevents charge buildup, lower pressure. |
Kinetic Energy Generation | Alternating current accelerates electrons, ionizing gas atoms efficiently. |
Comparison with Magnetron | Operates at lower pressures, ideal for delicate or temperature-sensitive substrates. |
Applications | Semiconductor industry, optical coatings, solar cells, and advanced materials. |
Optimize your thin film deposition process with RF sputtering—contact our experts today!