Powder metallurgy (PM) is a manufacturing process that involves creating metal objects from powdered metals rather than traditional methods like casting or forging. This technique is highly efficient, reducing material waste and costs, and allows for the production of precision components with unique properties that are difficult to achieve through other methods. PM is widely used to manufacture parts such as bushings, bearings, gears, and structural components. Its ability to produce complex shapes with high accuracy makes it a critical process in modern manufacturing, particularly in industries requiring durable and precise metal parts.
Key Points Explained:
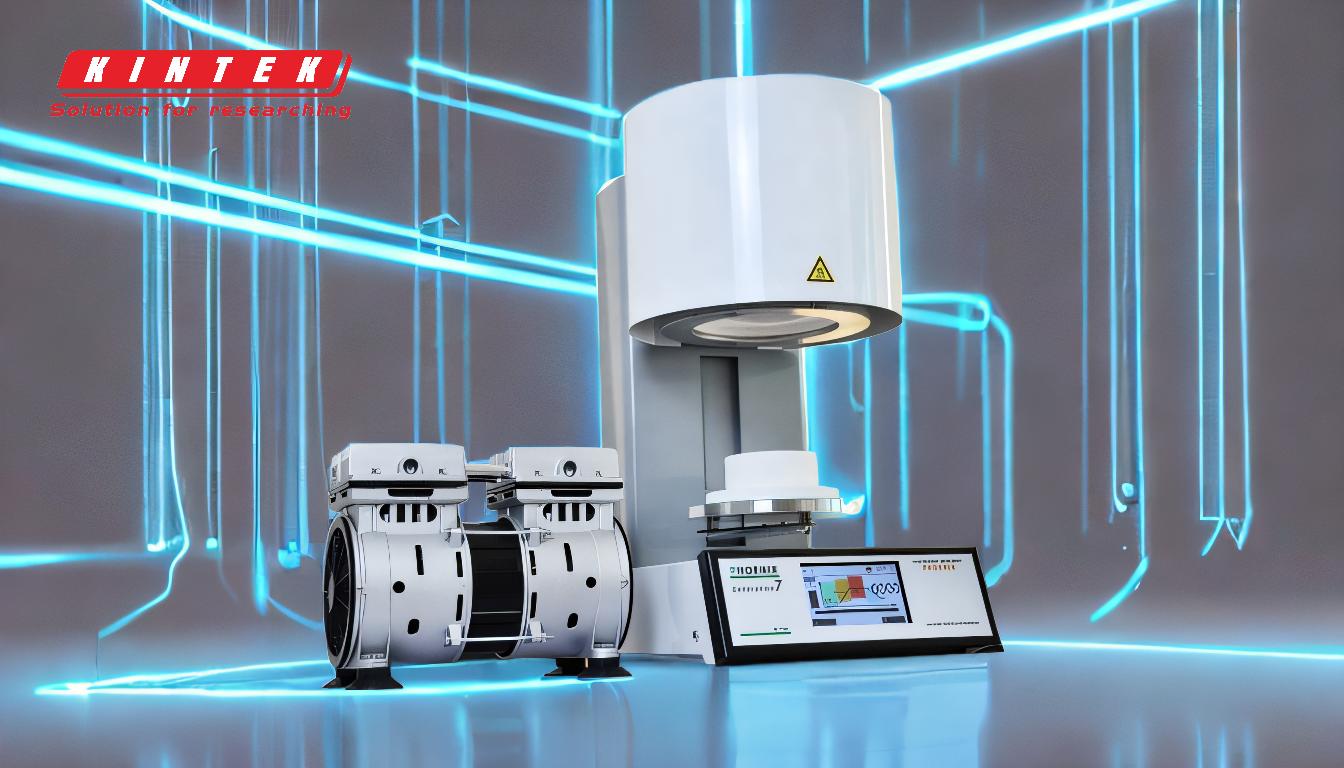
-
Definition and Process of Powder Metallurgy:
- Powder metallurgy is the process of forming metal objects from powdered metals rather than using molten metal or forging.
- The process involves pressing powdered metals or alloys into a rigid die under extreme pressure, followed by sintering (heating without melting) to bond the particles into a solid object.
-
Advantages of Powder Metallurgy:
- Material Efficiency: PM reduces or eliminates the need for subtractive processes (e.g., machining), minimizing material waste and lowering production costs.
- Precision and Accuracy: The process allows for the production of highly accurate and complex shapes with tight tolerances, making it ideal for precision components.
- Unique Material Properties: PM enables the creation of materials with specific properties, such as controlled porosity or unique alloy compositions, which are difficult or impossible to achieve through traditional methods.
-
Applications of Powder Metallurgy:
- Common Components: PM is widely used to produce bushings, bearings, gears, and structural parts, which are essential in industries like automotive, aerospace, and machinery.
- Versatility: The process is applicable to both ferrous (iron-based) and non-ferrous metals, making it suitable for a wide range of materials and applications.
-
Historical Context and Evolution:
- Powder metallurgy has ancient origins but saw significant development during the first industrial revolution.
- Its use has steadily grown over time, and it is now a critical manufacturing process for producing high-quality, durable parts.
-
Key Benefits for Equipment and Consumable Purchasers:
- Cost-Effectiveness: PM reduces material waste and machining costs, making it a cost-efficient option for producing metal parts.
- Durability and Performance: Components produced through PM often exhibit superior wear resistance, strength, and dimensional stability, ensuring long-lasting performance.
- Customization: PM allows for the creation of tailored materials and components to meet specific application requirements, offering flexibility to purchasers.
By leveraging powder metallurgy, manufacturers and purchasers can achieve high-quality, cost-effective, and customized metal components that meet the demands of modern industrial applications.
Summary Table:
Aspect | Details |
---|---|
Process | Pressing powdered metals into a die, followed by sintering to form solids. |
Advantages | Material efficiency, precision, unique properties, and cost-effectiveness. |
Applications | Bushings, bearings, gears, structural parts for automotive, aerospace, etc. |
Key Benefits | Reduced waste, superior durability, and tailored material customization. |
Unlock the potential of powder metallurgy for your manufacturing needs—contact us today!