PVD (Physical Vapor Deposition) coating is a advanced surface treatment technology used to apply thin, durable, and highly functional coatings to tooling and other metal substrates. It involves the deposition of metal vapors onto the substrate, forming a thin, pure metal or alloy layer that enhances the tool's performance. PVD coatings are widely used in industries such as construction, electronics, automotive, and machinery due to their ability to improve wear resistance, corrosion resistance, and surface hardness. These coatings also offer aesthetic benefits, environmental friendliness, and compatibility with various materials, making them a preferred choice for extending tool life, reducing maintenance, and improving productivity.
Key Points Explained:
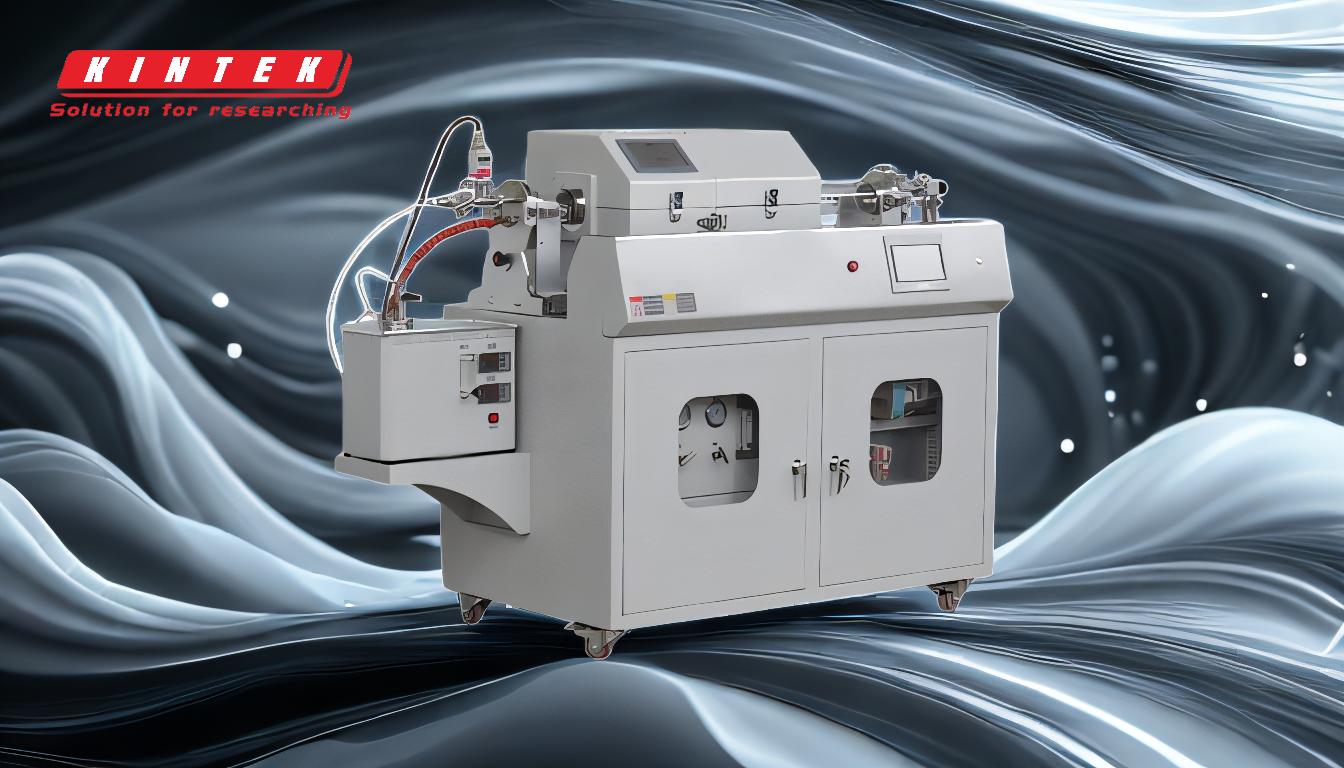
-
What is PVD Coating?
- PVD stands for Physical Vapor Deposition, a process where metal vapors are deposited onto a substrate to form a thin, pure metal or alloy coating.
- The process is used to create abrasion-resistant and wear-resistant coatings on tools and other metal components.
- It is widely applied in industries such as construction, electronics, automotive, and machinery.
-
Key Benefits of PVD Coating for Tooling:
- Enhanced Wear Resistance: PVD coatings significantly increase the wear resistance of tools, allowing them to withstand high temperatures, pressures, and mechanical stresses.
- Improved Corrosion Resistance: The coatings protect tools from oxidation and chemical degradation, extending their lifespan.
- Increased Surface Hardness: PVD coatings enhance the surface hardness of tools, making them more durable and less prone to deformation.
- Aesthetic Value: The coatings can provide a lustrous finish or change the color of the metal, improving the tool's appearance.
- Environmental Friendliness: PVD coatings are non-toxic and environmentally safe, making them a sustainable choice for surface treatment.
-
Technical Advantages of PVD Coatings:
- Uniform Coating: The process ensures a consistent and uniform coating thickness, even on complex geometries.
- Strong Adhesion: PVD coatings exhibit excellent adhesion to the substrate, ensuring long-lasting performance.
- Dimensional Accuracy: The coatings maintain the dimensional accuracy and contour precision of the tool, without altering its microstructure.
- Customizable Properties: PVD coatings can be tailored with variable layer structures (e.g., nanostructures, multilayers) to meet specific application requirements.
-
Applications in Tooling:
- Cutting Tools: PVD coatings are commonly used on cutting tools to enhance their wear and oxidation resistance, enabling longer or faster operation.
- Molds and Dies: The coatings improve the durability and performance of molds and dies, reducing maintenance and downtime.
- Industrial Machinery: PVD-coated components in machinery benefit from reduced friction, lower wear, and improved corrosion resistance.
-
Economic and Operational Benefits:
- Extended Tool Life: By protecting tools from wear, corrosion, and thermal shock, PVD coatings significantly extend their operational lifespan.
- Reduced Maintenance: The durability of PVD-coated tools reduces the need for frequent maintenance and replacement.
- Improved Productivity: Enhanced tool performance allows for faster and more efficient operations, boosting overall productivity.
-
Environmental and Safety Considerations:
- Non-Toxic Process: PVD coating is a clean and safe process that does not harm the human body or the environment.
- Sustainable Solution: The long-lasting nature of PVD coatings reduces waste and resource consumption, contributing to sustainability.
In summary, PVD coating is a versatile and highly effective surface treatment technology that offers numerous benefits for tooling applications. By enhancing wear resistance, corrosion resistance, and surface hardness, PVD coatings extend tool life, reduce maintenance, and improve productivity. Their environmental friendliness and aesthetic appeal further make them a preferred choice in various industries.
Summary Table:
Key Benefits | Technical Advantages | Applications |
---|---|---|
Enhanced wear resistance | Uniform coating thickness | Cutting tools |
Improved corrosion resistance | Strong adhesion | Molds and dies |
Increased surface hardness | Dimensional accuracy | Industrial machinery |
Aesthetic value | Customizable properties | |
Environmental friendliness |
Ready to enhance your tool performance with PVD coatings? Contact us today to learn more!