PVD (Physical Vapor Deposition) coating on inserts is a advanced surface treatment technology that significantly enhances the performance and longevity of cutting tools, molds, and other industrial components. By depositing a thin, hard, and wear-resistant layer of material onto the surface of inserts, PVD coatings provide superior protection against abrasive wear, reduce friction, and improve resistance to corrosion and high temperatures. This process not only extends the tool life but also enhances the overall efficiency and reliability of the coated components. PVD coatings are widely used in industries such as aerospace, medical, automotive, and high-tech due to their durability, aesthetic value, and environmental benefits.
Key Points Explained:
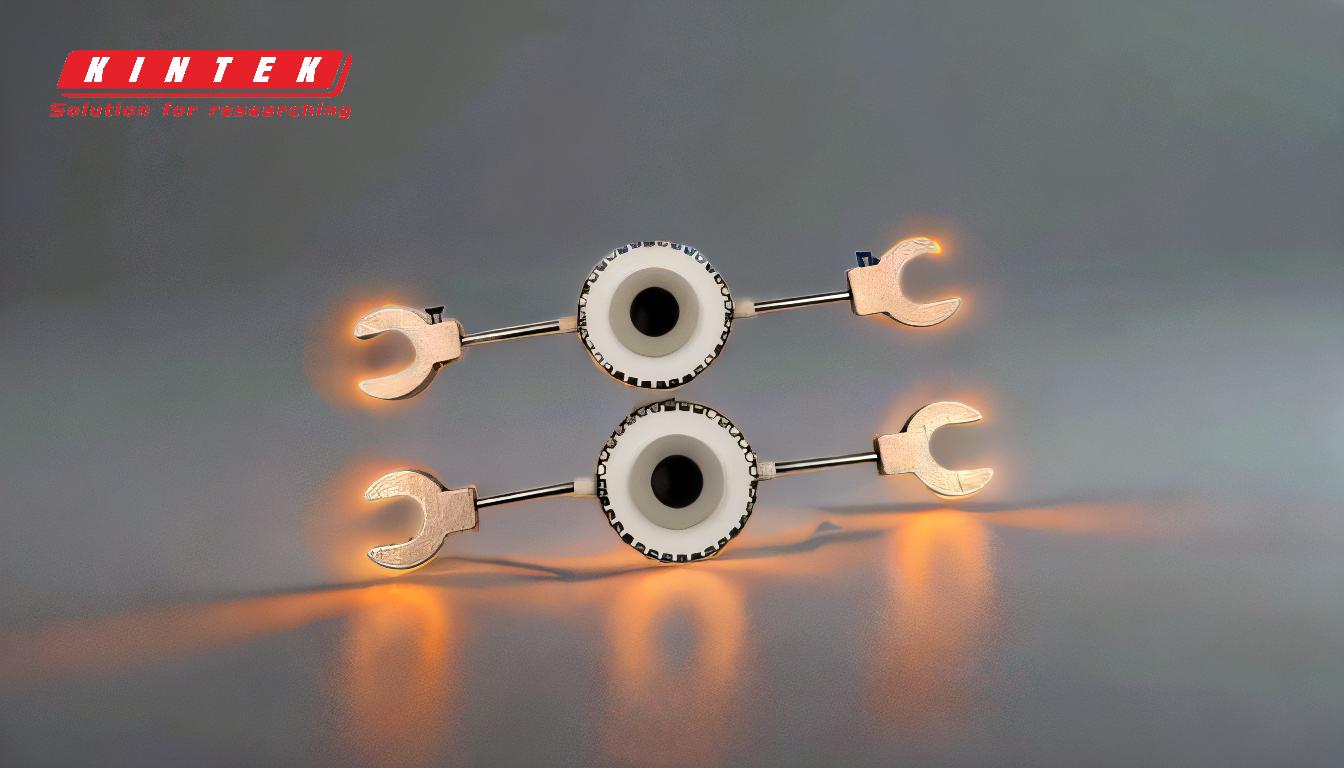
-
High Micro-Hardness and Lubricity:
- PVD coatings are known for their high micro-hardness, often exceeding 80 Rc, which provides excellent protection against abrasive wear. This hardness ensures that the coated inserts can withstand harsh working conditions and maintain their edge sharpness for longer periods.
- The low coefficient of friction offered by PVD coatings reduces resistance in forming tools, minimizes heat generation in cutting tools, and prevents material adhesion in slide wear applications. This results in improved tool performance and reduced wear.
-
Versatility in Material Deposition:
- PVD can deposit a wide range of materials, including metals, oxides, nitrides, carbides, and their mixtures. This versatility allows for the customization of coatings to meet specific application requirements.
- It can also coat substrates that are difficult to coat using other methods, such as plastics and bio substrates, expanding the range of applications for PVD coatings.
-
Thin and Uniform Coatings:
- PVD enables the deposition of extremely thin layers, down to several tens of nanometers. These thin coatings are uniform in appearance and provide exceptional protection without significantly altering the dimensions of the coated components.
- The uniformity of PVD coatings ensures consistent performance across the entire surface of the insert, reducing the likelihood of localized wear or failure.
-
Corrosion and Abrasion Resistance:
- PVD coatings offer superior corrosion resistance, making them ideal for use in harsh environments, such as marine applications. They also provide excellent abrasion resistance, which is crucial for maintaining the integrity of cutting tools and molds.
- Unlike coatings produced by electrochemical processes, PVD coatings do not fade over time and maintain their protective properties even after prolonged use.
-
Aesthetic and Environmental Benefits:
- PVD coatings improve the aesthetics of metal components by allowing the texture of the metal to remain visible and offering new color options, such as true black. This provides greater design freedom, particularly in industries like automotive design.
- The PVD process generates very little waste, requires no chemicals, and poses no explosion danger, making it an environmentally friendly coating option.
-
Durability and Longevity:
- PVD coatings are extremely tough and durable, significantly increasing the longevity of coated products and reducing maintenance costs. This durability is particularly valuable in industries where tools and components are subject to extreme conditions.
- The coatings are resistant to prolonged exposure to ultraviolet light, preventing corrosion and scratching, which further enhances their durability.
-
High-Temperature Tolerance:
- PVD coatings can tolerate high temperatures, making them suitable for applications where components are exposed to extreme heat. This property is particularly important in industries such as aerospace and high-tech, where components must perform reliably under high thermal stress.
-
In-Situ Controls for Process Stability:
- The integration of in-situ controls in PVD machines allows for real-time feedback and stability during the coating process. This ensures consistent quality and performance of the coatings, even in complex or large-scale production environments.
In summary, PVD coating on inserts is a highly effective surface treatment technology that enhances the performance, durability, and aesthetic appeal of industrial components. Its ability to provide high micro-hardness, low friction, corrosion resistance, and environmental benefits makes it a preferred choice in a wide range of industries.
Summary Table:
Key Benefits of PVD Coating | Details |
---|---|
High Micro-Hardness | Exceeds 80 Rc, protects against abrasive wear |
Low Friction | Reduces heat generation and material adhesion |
Versatile Material Deposition | Metals, oxides, nitrides, and carbides |
Thin and Uniform Coatings | Nanometer-thick, consistent protection |
Corrosion & Abrasion Resistance | Ideal for harsh environments |
Aesthetic & Environmental Benefits | Eco-friendly, enhances design options |
Durability & Longevity | Resists UV, scratches, and extreme conditions |
High-Temperature Tolerance | Suitable for aerospace and high-tech applications |
Upgrade your industrial tools with PVD coating—contact us today to learn more!