Physical Vapor Deposition (PVD) is a coating process used to apply thin films of material onto a substrate. The cost of PVD can vary significantly depending on several factors, including the type of PVD process, the materials used, the scale of production, and the complexity of the parts being coated. Below is a detailed breakdown of the key factors influencing PVD costs, along with an explanation of each.
Key Points Explained:
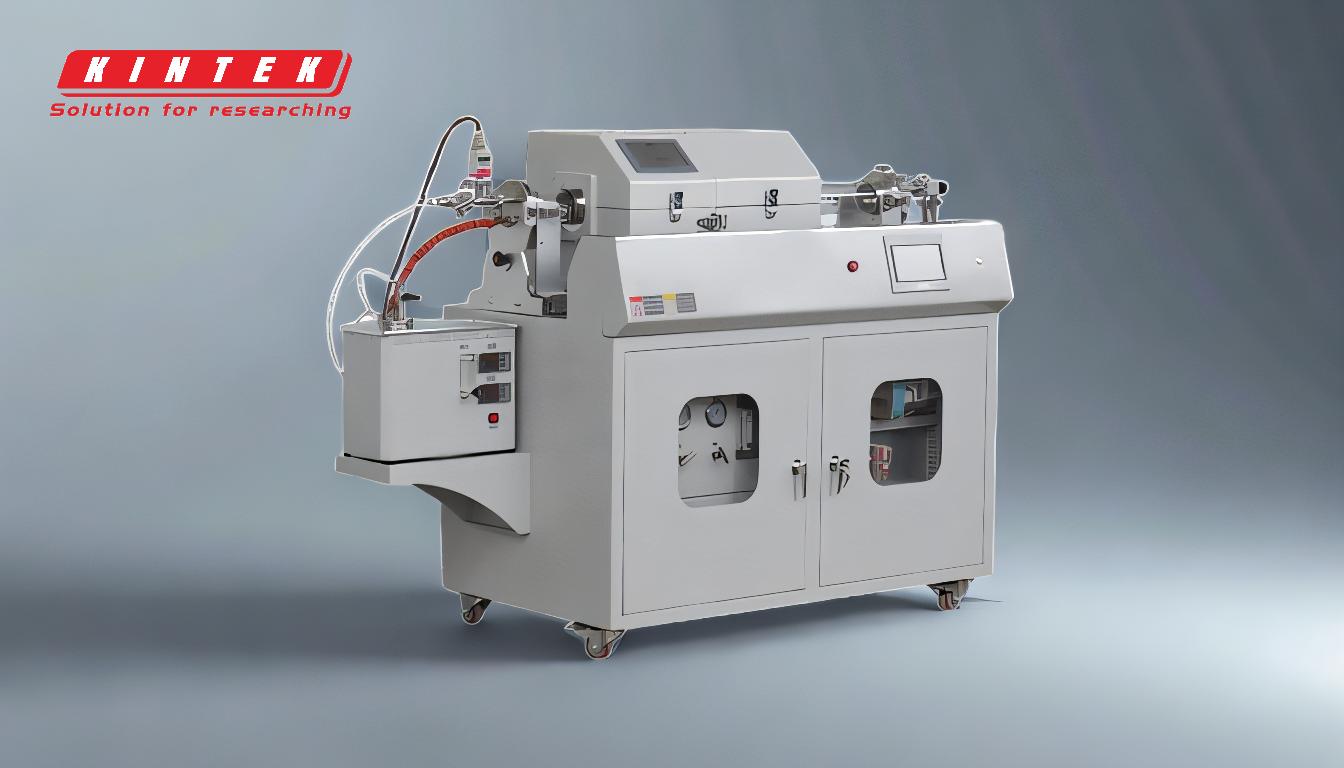
-
Type of PVD Process:
- PVD encompasses several techniques, such as sputtering, evaporation, and arc deposition. Each method has different equipment requirements, operational complexities, and material utilization efficiencies, which directly impact costs.
- For example, sputtering is often more expensive due to the need for high vacuum conditions and specialized targets, while evaporation might be cheaper but less versatile.
-
Materials Used:
- The cost of the target material (e.g., titanium, gold, or aluminum) significantly influences the overall PVD cost. Precious metals like gold are more expensive, while common metals like aluminum are relatively affordable.
- Additionally, the purity and form of the material (e.g., pellets, wires, or targets) can affect costs.
-
Scale of Production:
- Economies of scale play a crucial role. Large-scale production runs reduce the per-unit cost due to the amortization of fixed costs (e.g., equipment setup and maintenance) over a larger number of parts.
- Small-scale or custom jobs, on the other hand, tend to be more expensive per unit due to higher setup costs and lower throughput.
-
Complexity of Parts:
- The geometry and size of the parts being coated influence the cost. Complex shapes or large parts may require specialized fixtures, longer processing times, or multiple coating cycles, increasing costs.
- Surface preparation requirements (e.g., cleaning, polishing) also add to the overall expense.
-
Equipment and Maintenance Costs:
- PVD equipment is capital-intensive, with high initial investment costs. Maintenance, including regular replacement of consumables like targets and vacuum pump oils, adds to operational expenses.
- Advanced PVD systems with automation or enhanced capabilities (e.g., multi-layer coatings) are more expensive to operate.
-
Energy and Labor Costs:
- PVD processes require significant energy input, particularly for maintaining high vacuum conditions and powering deposition sources. Energy costs vary by region and can impact overall expenses.
- Skilled labor is required for operation, maintenance, and quality control, contributing to labor costs.
-
Quality and Thickness of Coating:
- Thicker coatings or multi-layer coatings require more material and longer processing times, increasing costs.
- High-quality coatings with stringent performance requirements (e.g., wear resistance, corrosion resistance) may involve additional steps, such as pre-treatment or post-treatment, further adding to expenses.
-
Market and Geographic Factors:
- Regional differences in labor rates, material availability, and energy costs can influence PVD pricing.
- Market demand for specific PVD services or materials can also drive costs up or down.
In summary, the cost of PVD is influenced by a combination of factors, including the type of process, materials, production scale, part complexity, equipment, labor, and market conditions. Understanding these factors can help purchasers make informed decisions and optimize costs for their specific needs.
Summary Table:
Factor | Impact on Cost |
---|---|
Type of PVD Process | Sputtering is costly due to high vacuum needs; evaporation is cheaper but less versatile. |
Materials Used | Precious metals (e.g., gold) are expensive; common metals (e.g., aluminum) are affordable. |
Scale of Production | Large-scale reduces per-unit costs; small-scale increases per-unit costs. |
Complexity of Parts | Complex shapes or large parts require specialized fixtures, increasing costs. |
Equipment & Maintenance | High initial investment and ongoing maintenance costs. |
Energy & Labor Costs | Significant energy input and skilled labor contribute to expenses. |
Quality & Thickness | Thicker or multi-layer coatings require more material and time, raising costs. |
Market & Geographic Factors | Regional labor rates, material availability, and energy costs influence pricing. |
Ready to optimize your PVD coating costs? Contact our experts today for tailored solutions!