Physical Vapor Deposition (PVD) is a critical nanotechnology process used to deposit thin films of materials onto substrates, enhancing their mechanical, optical, chemical, or electronic properties. It involves converting a solid material into a vapor phase, transporting it through a vacuum or low-pressure gas environment, and then condensing it back into a solid film on a target surface. PVD is widely used in industries such as microelectronics, aerospace, decorative coatings, and nanocomposite synthesis due to its ability to produce highly reliable, durable, and functional coatings. Its applications range from improving substrate resistance to high temperatures and oxidation to creating thin films for semiconductors, solar panels, and decorative hardware.
Key Points Explained:
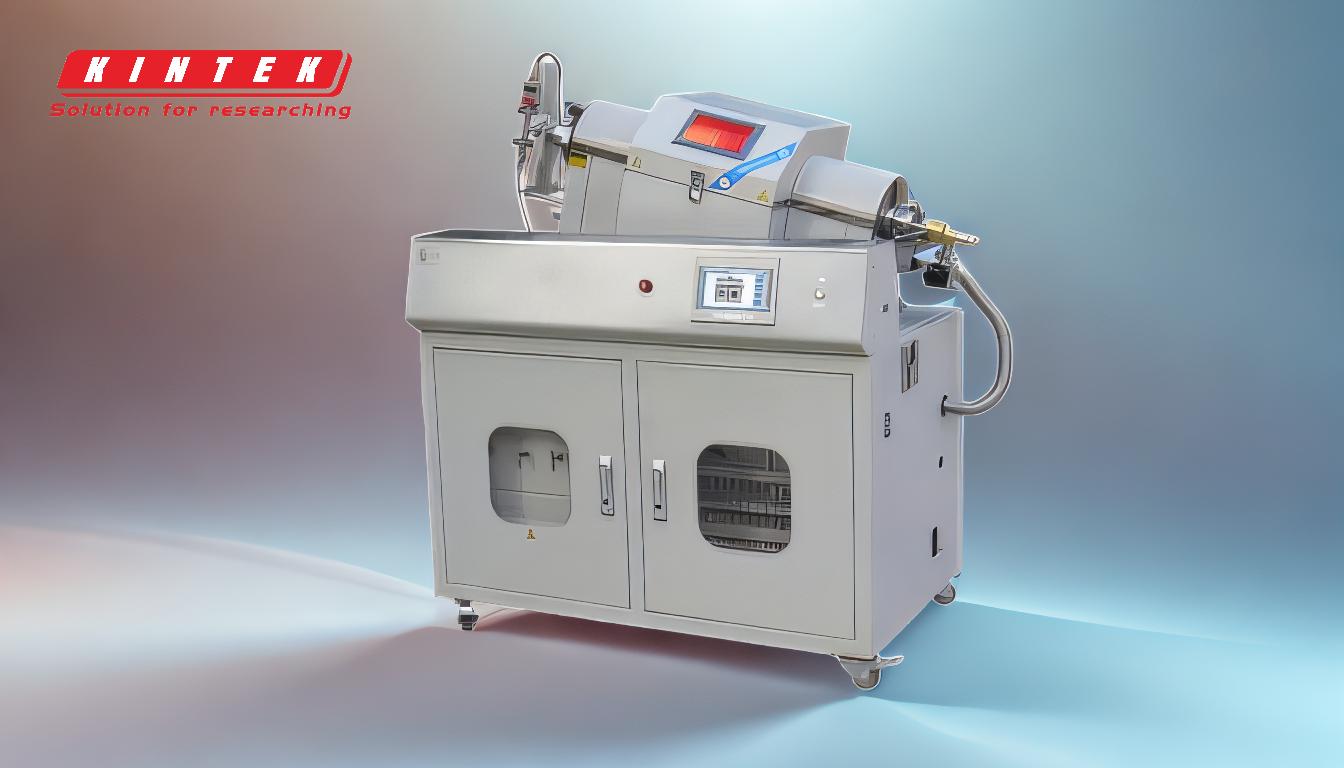
-
Definition and Process of PVD:
- PVD is a vacuum-based coating process where a solid material is vaporized and then deposited onto a substrate as a thin film.
- The process involves three main stages:
- Vaporization: The solid material is vaporized using methods like sputtering, evaporation, or arc vaporization.
- Transport: The vaporized atoms or molecules travel through a vacuum or low-pressure gas environment.
- Condensation: The vapor condenses onto the substrate, forming a thin, uniform film.
-
Applications of PVD in Nanotechnology:
- Microelectronics: PVD is essential for depositing thin films in semiconductor devices, which are foundational to most microelectronic products. It is highly reliable and cost-effective, making it a preferred method in this industry.
- Aerospace: PVD coatings improve the resistance of substrates to high temperatures and ablation, making them suitable for aerospace components.
- Decorative Coatings: PVD is widely used in decorative applications, such as door and window hardware, jewelry, and lamps, due to its ability to produce durable and aesthetically pleasing finishes.
- Optical and Mechanical Functions: PVD is used to create thin films for optical coatings (e.g., anti-reflective coatings) and mechanical applications (e.g., wear-resistant coatings).
-
Advantages of PVD:
- Durability: PVD coatings are highly durable and resistant to wear, corrosion, and oxidation.
- Aesthetic Quality: The coatings reflect surfaces well and do not require additional polishing to achieve a metallic luster.
- Versatility: PVD can deposit a wide range of materials, including metals, alloys, and ceramics, making it suitable for diverse applications.
- Environmental Friendliness: PVD is a clean process that produces minimal waste compared to other coating methods.
-
PVD in Nanocomposite Synthesis:
- PVD is used to create nanocomposites by reinforcing ceramic matrices with nanoparticles. For example, it has been used to deposit AlSiTiN nanoparticles into a Si3N4 matrix, enhancing the mechanical properties of the coating.
- The process involves creating a high DC voltage to vaporize the cathode material, which then combines with process gases to form nanocomposites on the target surface.
-
Industries Utilizing PVD:
- Microelectronics: The largest market for PVD equipment, driven by the demand for thin-film deposition in semiconductor manufacturing.
- Solar Energy: PVD is used to produce thin-film solar panels, which are lightweight and cost-effective.
- Decorative Hardware: PVD coatings are popular in the hardware industry for their durability and aesthetic appeal.
- Aerospace and Automotive: PVD coatings improve the performance and longevity of components exposed to extreme conditions.
-
Future Trends and Innovations:
- The demand for PVD is expected to grow with advancements in nanotechnology, particularly in areas like flexible electronics, energy storage, and biomedical devices.
- Innovations in PVD techniques, such as hybrid PVD-CVD (Chemical Vapor Deposition) processes, are expanding its applications and improving coating performance.
In summary, PVD is a versatile and essential nanotechnology process with broad applications across multiple industries. Its ability to produce high-quality, functional, and durable coatings makes it a cornerstone of modern manufacturing and innovation.
Summary Table:
Aspect | Details |
---|---|
Definition | Vacuum-based process to deposit thin films on substrates. |
Key Stages | Vaporization, Transport, Condensation. |
Applications | Microelectronics, Aerospace, Decorative Coatings, Nanocomposite Synthesis. |
Advantages | Durability, Aesthetic Quality, Versatility, Environmental Friendliness. |
Industries | Microelectronics, Solar Energy, Decorative Hardware, Aerospace & Automotive. |
Future Trends | Growth in flexible electronics, energy storage, and biomedical devices. |
Discover how PVD can transform your materials—contact our experts today for tailored solutions!