PVD (Physical Vapor Deposition) medical coating is a specialized thin-film coating technology widely used in the medical field to enhance the performance, durability, and functionality of medical devices and instruments. It involves depositing a thin layer of material onto a substrate through a vacuum-based process, which improves properties such as wear resistance, corrosion resistance, hardness, and biocompatibility. PVD coatings are essential in applications like orthopedics, dentistry, and surgical tools, where they help prevent wear, reduce friction, and protect against biological interactions. Additionally, PVD coatings can improve the aesthetic appeal of medical devices while maintaining their functionality. Common materials used in PVD coatings for medical applications include titanium nitride and chromium nitride.
Key Points Explained:
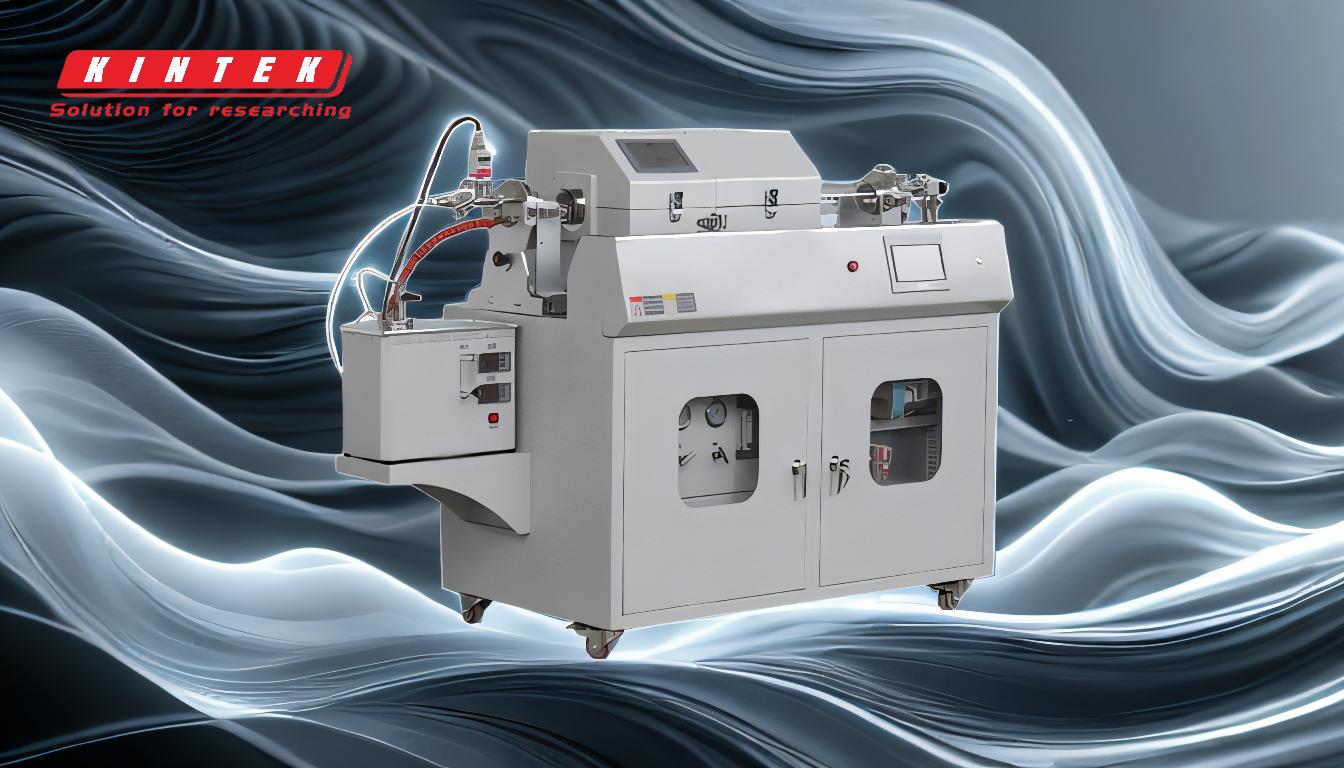
-
What is PVD Coating?
- PVD (Physical Vapor Deposition) is a vacuum-based process where a thin film of material is deposited onto a substrate.
- It is used to enhance surface properties such as hardness, wear resistance, corrosion resistance, and biocompatibility.
- The process involves vaporizing a solid material in a vacuum chamber and depositing it onto the target surface.
-
Applications in the Medical Field
- Orthopedics: PVD coatings like titanium nitride are used on prosthetics to prevent rejection by the body and improve biocompatibility.
- Dentistry: Dental instruments benefit from PVD coatings, which protect against wear and corrosion during repeated sterilization.
- Surgical Instruments: Scalpels and other tools are coated to retain sharpness and resist wear, improving their longevity and performance.
-
Key Benefits of PVD Coatings in Medical Devices
- Wear Resistance: PVD coatings significantly increase the durability of medical tools, reducing wear and extending their lifespan.
- Corrosion Resistance: The coatings protect against corrosion, which is critical for instruments exposed to biological fluids and sterilization processes.
- Biocompatibility: Materials like titanium nitride are biocompatible, making them ideal for implants and prosthetics.
- Aesthetic Appeal: PVD coatings can provide a lustrous finish or change the color of medical devices without affecting performance.
-
Common PVD Coating Materials in Medicine
- Titanium Nitride (TiN): Used for prosthetics and surgical tools due to its biocompatibility and ability to retain sharpness.
- Chromium Nitride (CrN): Applied to orthopaedic and dental instruments for its wear and corrosion resistance, especially during sterilization.
-
Advantages of PVD Coatings
- Durability: PVD coatings improve the hardness and wear resistance of medical devices, increasing tool life by up to 10 times.
- Environmental Friendliness: The process produces clean and pure materials, making it suitable for medical applications like surgical implants.
- Versatility: PVD coatings can be applied in various forms (nanostructures, multilayers, monolayers) and combined with friction-reducing layers.
- Precision: The coatings offer excellent dimensional and contour accuracy, ensuring minimal impact on the substrate's microstructure.
-
Impact on Medical Device Performance
- PVD coatings enhance the performance of medical devices by providing a protective layer that resists wear, corrosion, and biological interactions.
- They improve the cost-effectiveness of medical tools by extending their lifespan and reducing the need for frequent replacements.
- The coatings also improve the surface quality of devices, making them easier to clean and sterilize.
-
Future Trends and Innovations
- Ongoing research focuses on developing new PVD coating materials with enhanced properties for medical applications.
- Innovations in nanostructured and multilayer coatings are expected to further improve the performance and functionality of medical devices.
In summary, PVD medical coatings are a critical technology in the medical field, offering a combination of durability, biocompatibility, and aesthetic appeal. They play a vital role in enhancing the performance and longevity of medical devices, from surgical instruments to implants, while meeting the stringent requirements of the healthcare industry.
Summary Table:
Aspect | Details |
---|---|
Process | Vacuum-based deposition of thin-film materials onto substrates. |
Key Benefits | Wear resistance, corrosion resistance, biocompatibility, and aesthetic appeal. |
Applications | Orthopedics, dentistry, surgical instruments. |
Common Materials | Titanium Nitride (TiN), Chromium Nitride (CrN). |
Advantages | Durability, environmental friendliness, versatility, precision. |
Impact | Extends device lifespan, improves cost-effectiveness, enhances sterilization. |
Learn how PVD coatings can optimize your medical devices—contact our experts today!