PVD (Physical Vapor Deposition) plating is a cutting-edge coating technology used to apply thin, durable, and high-performance layers to various materials. It is widely employed in industries such as jewelry, automotive, hardware, and tools due to its ability to enhance product durability, resistance, and aesthetic appeal. The process involves vaporizing a solid material in a vacuum chamber and depositing it onto a target substrate, creating a pure and extremely thin coating. PVD plating is environmentally friendly, as it avoids toxic byproducts, and it significantly extends the lifespan of products, making it a preferred alternative to traditional plating methods like chrome plating.
Key Points Explained:
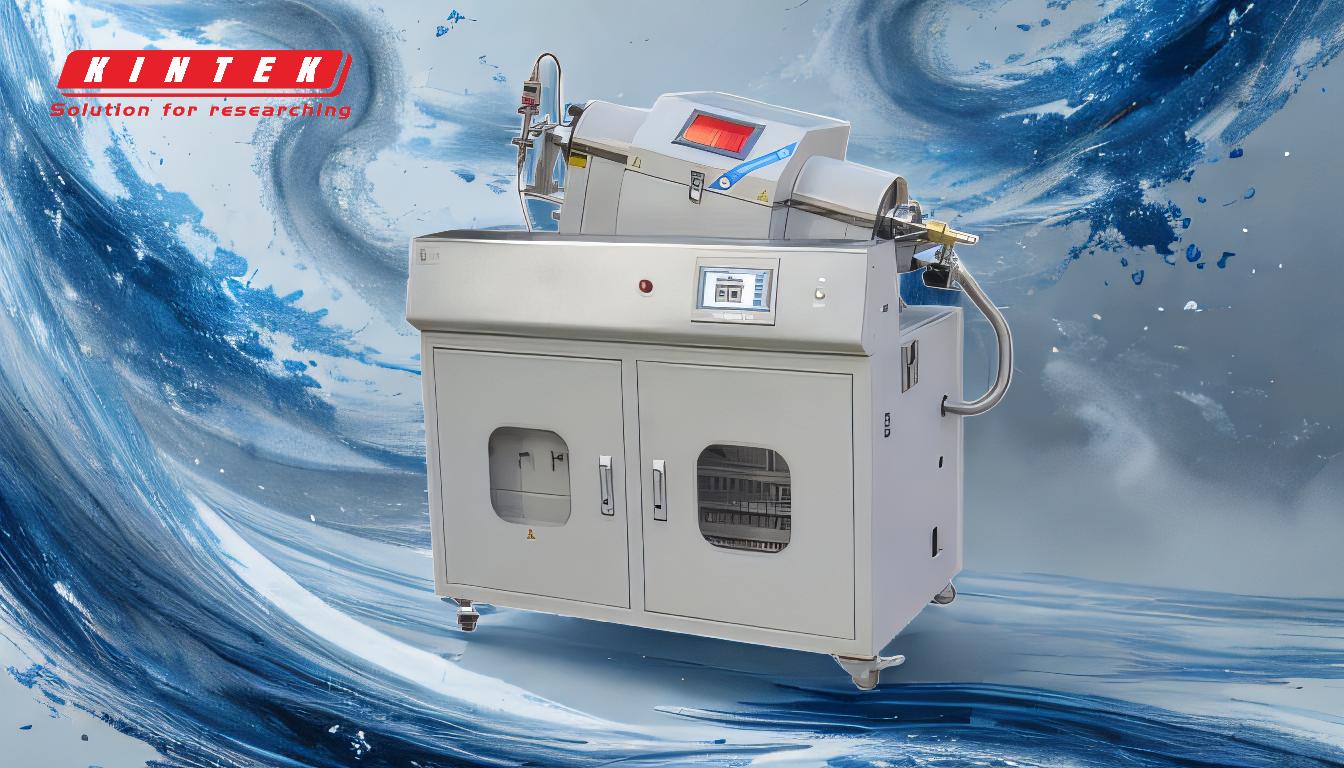
-
What is PVD Plating?
- PVD plating is a thin-film coating process conducted under vacuum conditions. It involves vaporizing a solid material and depositing it onto a substrate atom by atom. This results in a highly pure and durable coating that enhances the properties of the base material.
-
How Does the PVD Process Work?
- The PVD process consists of four main steps:
- Ablation: A solid precursor material is bombarded with a beam of electrons, releasing atoms of that material.
- Transport: The released atoms move through the vacuum chamber.
- Reaction: The atoms may react with other gases in the chamber to form compounds.
- Deposition: The atoms or compounds are deposited onto the substrate, forming a thin and uniform coating.
- The PVD process consists of four main steps:
-
Applications of PVD Plating
- PVD plating is used in a wide range of industries and applications, including:
- Decorative Coatings: Jewelry, door and window hardware, kitchen and bathroom fixtures, and lamps.
- Tribological Coatings: Automotive parts (e.g., wheels, pistons), surgical tools, drill bits, and guns.
- Functional Coatings: Glass surfaces for thermo-optical properties and innovative projects in new markets.
- PVD plating is used in a wide range of industries and applications, including:
-
Advantages of PVD Plating
- Durability: PVD coatings can extend the lifespan of products by up to ten times, with some coatings lasting more than 25 years.
- Environmental Friendliness: Unlike chrome plating, PVD does not produce toxic substances, making it a greener alternative.
- Enhanced Properties: PVD coatings improve wear resistance, hardness, oxidation resistance, and scratch resistance, making them ideal for demanding applications.
-
Comparison with Traditional Plating Methods
- PVD plating is superior to traditional methods like chrome plating in several ways:
- It produces thinner, more uniform coatings.
- It is more environmentally friendly.
- It offers better performance in terms of durability and resistance to wear and corrosion.
- PVD plating is superior to traditional methods like chrome plating in several ways:
-
Future of PVD Plating
- As industries continue to seek sustainable and high-performance solutions, PVD plating is expected to play a significant role in new markets and innovative applications. Its ability to enhance product longevity and reduce environmental impact makes it a valuable technology for the future.
In summary, PVD plating is a versatile and sustainable coating technology that offers significant advantages over traditional methods. Its applications span various industries, and its ability to enhance product performance and durability makes it a preferred choice for manufacturers worldwide.
Summary Table:
Aspect | Details |
---|---|
Definition | A thin-film coating process conducted under vacuum conditions. |
Process Steps | Ablation, Transport, Reaction, Deposition. |
Applications | Jewelry, automotive parts, hardware, tools, and more. |
Advantages | Durability, environmental friendliness, enhanced wear and scratch resistance. |
Comparison | Superior to chrome plating in thickness, uniformity, and eco-friendliness. |
Future Outlook | Expected to grow in sustainable and high-performance applications. |
Ready to enhance your products with PVD plating? Contact us today to learn more!