Biomass pyrolysis is a thermochemical process that decomposes organic materials like agricultural waste, forest residues, and energy crops in the absence of oxygen. This process produces three main products: biochar, bio-oil, and combustible gases. The mechanism of pyrolysis involves three key steps: char formation, depolymerization, and fragmentation. Factors such as temperature, heating rate, residence time, and biomass composition significantly influence the yield and quality of the pyrolysis products. Higher temperatures favor gas production, while lower temperatures promote solid char formation. Optimal conditions for liquid bio-oil production include moderate temperatures, high heating rates, and short gas residence times. Understanding these mechanisms and influencing factors is crucial for optimizing pyrolysis processes for specific applications.
Key Points Explained:
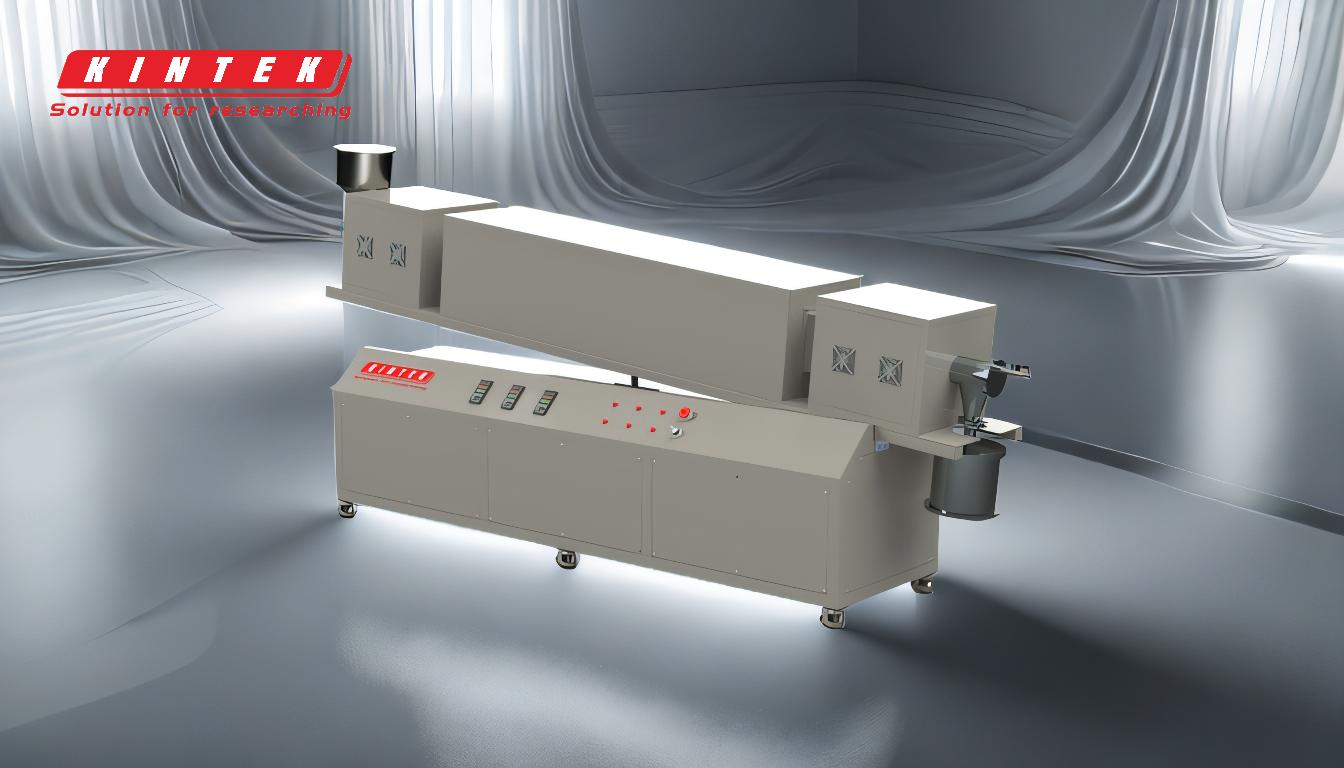
-
Definition of Biomass Pyrolysis:
- Pyrolysis is a thermochemical process that thermally decomposes organic materials like biomass in the absence of oxygen.
- It produces three main products: biochar (solid), bio-oil (liquid), and combustible gases.
-
Mechanisms of Pyrolysis:
- Char Formation: Occurs at lower temperatures and involves the solid residue left after volatile components are released.
- Depolymerization: Breaks down large polymer chains in biomass into smaller molecules, often leading to the formation of bio-oil.
- Fragmentation: Involves the breakdown of biomass into smaller molecules, contributing to the production of gases and lighter oils.
-
Key Factors Influencing Pyrolysis:
- Temperature: Higher temperatures (above 500°C) increase the production of non-condensable gases, while lower temperatures favor solid char formation.
- Heating Rate: High heating rates and short gas residence times are optimal for liquid bio-oil production.
- Residence Time: Longer residence times at high temperatures favor gas production, while shorter times are better for bio-oil.
- Biomass Composition: Different components of biomass decompose at different temperatures, affecting the yield and composition of pyrolysis products.
- Particle Size: Smaller particles decompose more quickly, leading to higher yields of pyrolysis oil.
-
Process Steps in Biomass Pyrolysis:
- Pre-treatment: Drying and crushing the biomass to prepare it for pyrolysis.
- Pyrolysis: Heating the biomass in the absence of oxygen to produce biochar, bio-oil, and gases.
- Discharging: Cooling the biochar and collecting it for further use.
- De-dusting: Cleaning the exhaust gases to reduce harmful substances before release.
-
Product Yields and Conditions:
- Char: Produced at low temperatures and low heating rates.
- Bio-oil: Optimal conditions include moderate temperatures, high heating rates, and short gas residence times.
- Gases: Produced at high temperatures, low heating rates, and long gas residence times.
-
Applications and Importance:
- Pyrolysis is a key technology for converting biomass into valuable products like biochar, bio-oil, and syngas, which can be used for energy production, soil amendment, and chemical feedstocks.
- Understanding the pyrolysis mechanism and optimizing process conditions can enhance the efficiency and sustainability of biomass utilization.
By carefully controlling the factors and understanding the mechanisms involved, the pyrolysis process can be tailored to produce the desired products efficiently, making it a versatile and valuable technology for biomass conversion.
Summary Table:
Key Aspect | Details |
---|---|
Definition | Thermochemical decomposition of biomass in the absence of oxygen. |
Main Products | Biochar (solid), bio-oil (liquid), and combustible gases. |
Mechanisms | Char formation, depolymerization, and fragmentation. |
Key Factors | Temperature, heating rate, residence time, biomass composition, particle size. |
Optimal Conditions | Moderate temps, high heating rates, and short gas residence times for bio-oil. |
Applications | Energy production, soil amendment, and chemical feedstocks. |
Optimize your biomass pyrolysis process—contact our experts today for tailored solutions!