RF sputtering, or radio frequency sputtering, is a specialized technique used to deposit thin films, particularly for non-conductive (dielectric) materials. Unlike DC sputtering, which is suitable for conductive targets, RF sputtering uses an alternating current (AC) power source at radio frequencies (typically 13.56 MHz) to prevent charge buildup on insulating targets. This process involves alternating electrical potentials in a vacuum environment, where positive ions are generated from an inert gas and directed toward the target material. The alternating cycles of positive and negative voltage ensure continuous ion bombardment and prevent surface charging, making RF sputtering ideal for creating high-quality thin films in industries like semiconductors and computer manufacturing.
Key Points Explained:
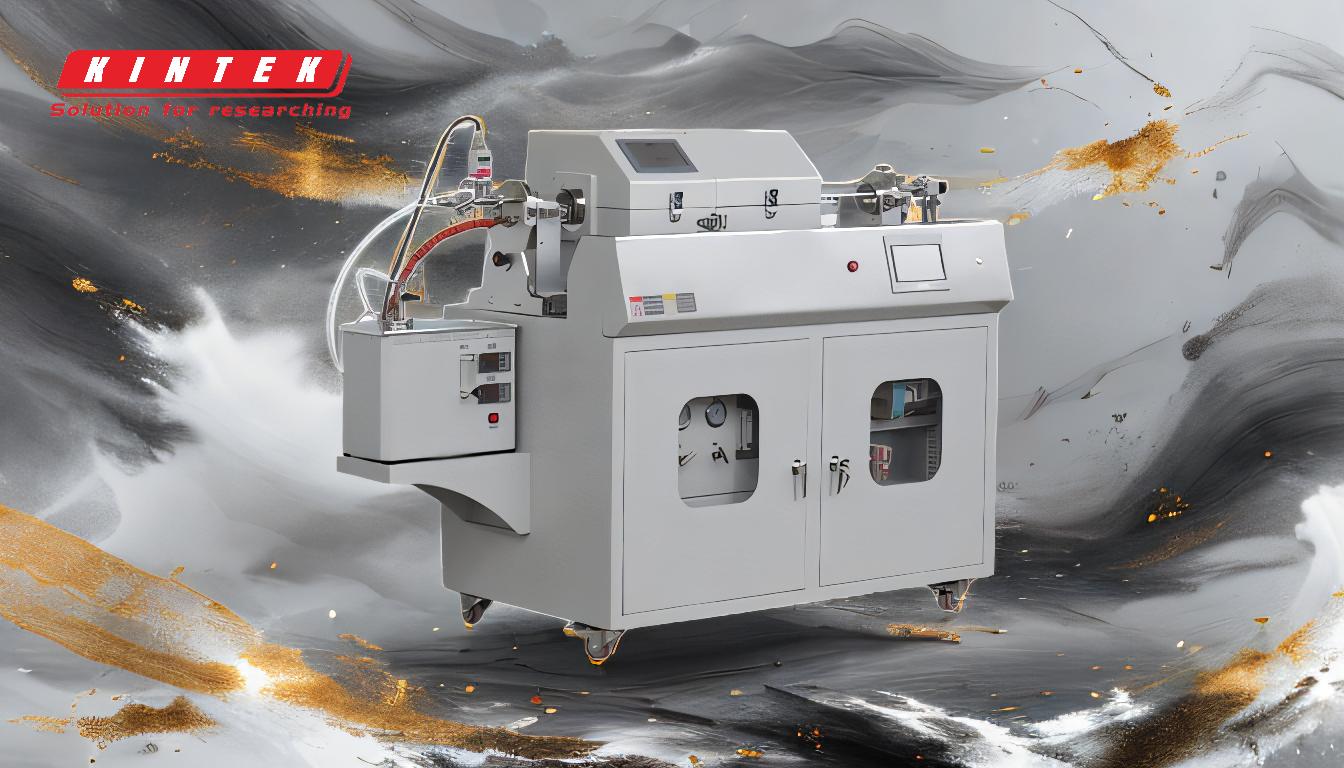
-
Definition and Purpose of RF Sputtering:
- RF sputtering is a thin-film deposition technique used primarily for non-conductive (insulating) materials.
- It is essential in industries like semiconductors and computer manufacturing, where precise and high-quality thin films are required.
-
How RF Sputtering Works:
- The process uses an AC power source operating at radio frequencies (typically 13.56 MHz).
- In a vacuum environment, an inert gas (e.g., argon) is ionized to create positive ions.
- These ions are directed toward the target material, causing it to break into fine particles that coat the substrate.
-
Positive and Negative Cycles:
- Positive Cycle: Electrons are attracted to the cathode, creating a negative bias on the target surface. This helps neutralize any positive charge buildup.
- Negative Cycle: Positive ions bombard the target material, enabling the sputtering process to continue without interruption.
-
Preventing Charge Buildup:
- Insulating materials tend to accumulate surface charges when bombarded with positive ions, which can repel further ions and halt the sputtering process.
- RF sputtering overcomes this by alternating the electrical potential, ensuring that the target surface remains neutral and sputtering continues.
-
Advantages Over DC Sputtering:
- DC sputtering is cost-effective for conductive materials but ineffective for non-conductive targets due to surface charging.
- RF sputtering is specifically designed for non-conductive materials, making it versatile for a wider range of applications.
-
Applications of RF Sputtering:
- Commonly used in the semiconductor industry to create thin films for integrated circuits and microelectronics.
- Also employed in the production of optical coatings, solar cells, and other advanced materials requiring precise deposition.
-
Technical Considerations:
- A matching network is used to optimize power delivery at the fixed radio frequency (13.56 MHz).
- The alternating electrical potential ensures consistent ion bombardment and prevents arcing, which could compromise film quality.
-
Challenges and Quality Control:
- Maintaining a stable plasma environment is critical to avoid arcing and ensure uniform film deposition.
- Proper calibration of the RF power source and matching network is essential for consistent results.
By understanding these key points, a purchaser of equipment or consumables can better evaluate the suitability of RF sputtering for their specific needs, ensuring high-quality thin-film deposition for non-conductive materials.
Summary Table:
Key Aspect | Details |
---|---|
Definition | Thin-film deposition technique for non-conductive (dielectric) materials. |
Power Source | AC power at 13.56 MHz to prevent charge buildup. |
Process | Alternating electrical potentials in a vacuum environment. |
Advantages | Ideal for insulating materials; prevents surface charging. |
Applications | Semiconductors, optical coatings, solar cells, and microelectronics. |
Technical Considerations | Matching network for power optimization; stable plasma environment required. |
Need RF sputtering solutions for your project? Contact us today to get started!