Sintered metal is a type of material created through the process of sintering, which involves compacting and heating metal powders below their melting point to form a solid structure. Unlike soldering, which uses a melted alloy to join metal parts, sintering relies on pressure and heat to bond metal particles without fully melting them. This process results in a durable, porous, and lightweight material with unique properties, making it suitable for various industrial applications.
Key Points Explained:
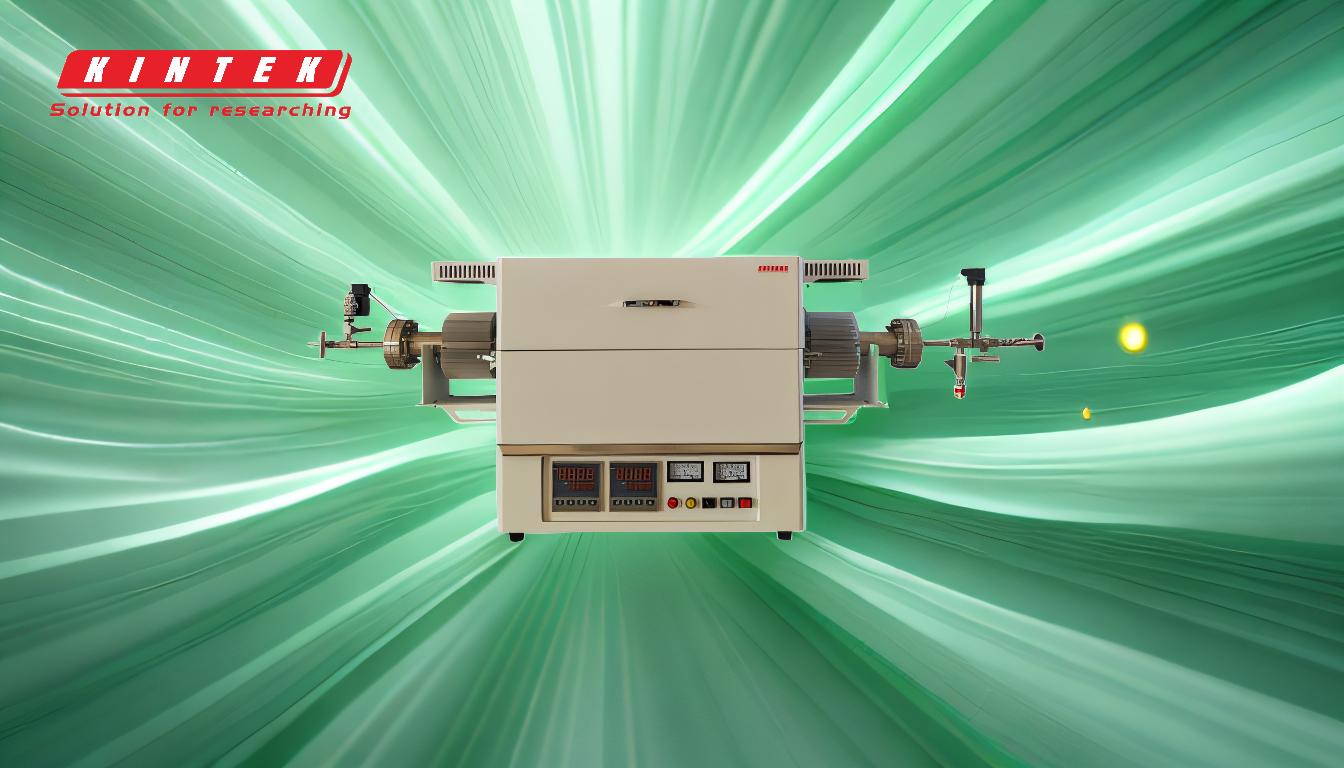
-
Definition of Sintered Metal:
- Sintered metal is produced by compacting metal powders into a desired shape and then heating them at temperatures below their melting point. This process fuses the particles together, creating a solid yet porous structure.
-
Sintering vs. Soldering:
- Sintering: Combines pressure and heat to bond metal powders without melting them. This process is used to create complex shapes and structures with controlled porosity.
- Soldering: Uses a melted alloy to join two metal parts together. It does not require pressure and typically results in a fully dense joint.
-
Process of Sintering:
- Compaction: Metal powders are pressed into a mold under high pressure to form a "green" part, which is fragile and requires further processing.
- Heating: The green part is heated in a controlled environment (often in a muffle furnace) at temperatures below the metal's melting point. This causes the particles to bond through diffusion, creating a solid structure.
- Cooling: The sintered part is cooled slowly to ensure stability and strength.
-
Properties of Sintered Metal:
- Porosity: The sintering process leaves small voids between particles, making the material lightweight and suitable for applications like filters or bearings.
- Strength: Despite its porosity, sintered metal can be highly durable, especially when alloyed or infiltrated with other materials.
- Customizability: Sintering allows for the creation of complex shapes and tailored material properties, such as controlled density and permeability.
-
Applications of Sintered Metal:
- Automotive Industry: Used for gears, bearings, and engine components due to its strength and wear resistance.
- Aerospace: Lightweight sintered parts are ideal for aircraft components.
- Medical Devices: Sintered metals are used in implants and surgical instruments because of their biocompatibility and precision.
- Filtration: Porous sintered metals are used in filters for liquids and gases.
-
Advantages of Sintered Metal:
- Cost-Effective: Sintering reduces material waste and allows for mass production of complex parts.
- Material Efficiency: The process uses nearly all the raw material, minimizing scrap.
- Design Flexibility: Sintering enables the production of intricate shapes that are difficult to achieve with traditional machining.
-
Limitations of Sintered Metal:
- Porosity: While beneficial in some applications, porosity can limit the material's strength and durability in high-stress environments.
- Size Constraints: The size of sintered parts is often limited by the size of the sintering furnace.
- Post-Processing: Some sintered parts may require additional treatments, such as infiltration or coating, to enhance their properties.
In summary, sintered metal is a versatile material created through a unique process that combines pressure and heat to bond metal powders. Its properties, such as porosity and customizability, make it suitable for a wide range of applications across industries. While it has some limitations, its advantages in cost-effectiveness and design flexibility make it a valuable material in modern manufacturing.
Summary Table:
Aspect | Details |
---|---|
Definition | Sintered metal is formed by compacting and heating metal powders below their melting point. |
Process | Compaction → Heating (below melting point) → Cooling. |
Properties | Porous, lightweight, durable, customizable, and strong. |
Applications | Automotive, aerospace, medical devices, and filtration. |
Advantages | Cost-effective, material-efficient, and design-flexible. |
Limitations | Porosity, size constraints, and potential need for post-processing. |
Curious about how sintered metal can benefit your industry? Contact us today to learn more!