Sintered metal refers to metal parts created through the sintering process in powder metallurgy, where compacted metal powder is heated to fuse particles, resulting in a harder and stronger part. This process involves blending fine powdered metals, pressing them into a desired shape, and heating the compressed part in a controlled atmosphere to bond the material. Sintering is crucial for materials with high melting points, such as tungsten and molybdenum, and offers benefits like high production efficiency, cost-effectiveness, and the ability to create complex shapes. The process is divided into three main steps: blending, compaction, and sintering, and is widely used in manufacturing ceramics, glass, and steel.
Key Points Explained:
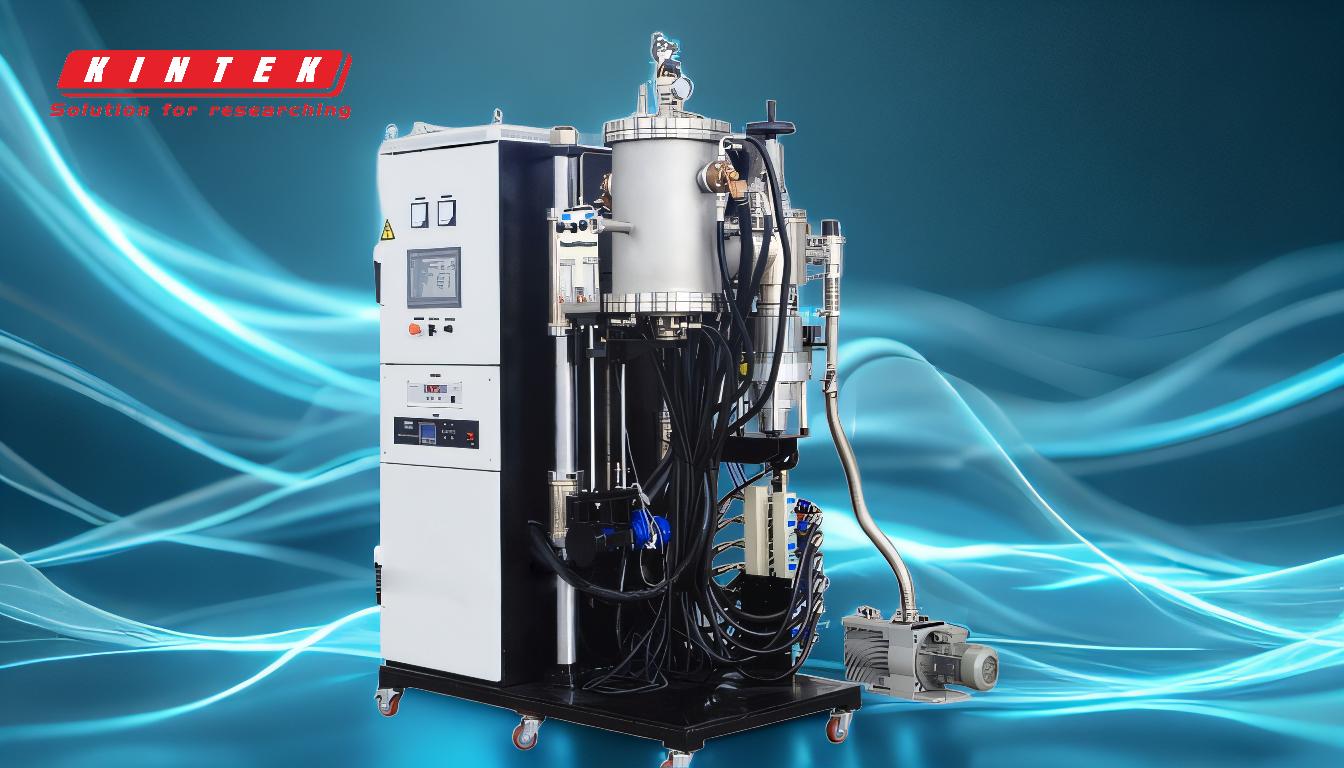
-
Definition of Sintered Metal:
- Sintered metal is produced through the sintering process in powder metallurgy.
- It involves heating compacted metal powder to fuse particles, resulting in a harder and stronger part.
-
The Sintering Process:
- Blending: Fine powdered metals are mixed to achieve the desired composition.
- Compaction: The blended powder is pressed into a desired shape using mechanical or hydraulic presses.
- Sintering: The compacted part is heated in a controlled atmosphere to bond the material, without melting it completely.
-
Materials Used:
- Sintering is often used for materials with extremely high melting points, such as tungsten and molybdenum.
- It is also used in the manufacture of ceramics, glass, and steel.
-
Benefits of Sintered Metal Products:
- Versatility: Ability to produce parts from a variety of materials.
- Efficiency: High production efficiency for both low- and high-volume production.
- Cost-Effectiveness: Lowered costs due to less material waste.
- Complexity: Ability to create highly complex parts and shapes.
- Environmental Friendliness: Reduced waste and energy consumption.
- Quality: Excellent surface finishes, good performance properties, and good tolerance control.
-
Industrial Applications:
- Steel Production: Sintering is used to produce lumps of iron from iron ore mixed with coke, which are then burned in a blast furnace to produce steel.
- Ceramics and Glass: Sintering is crucial in the manufacture of ceramics and glass, where it helps in forming solid masses from powdered materials.
-
Temperature Control:
- The sintering temperature is always below the melting point of the material to avoid complete liquefaction.
- This precise temperature control ensures that the particles fuse together without melting, maintaining the integrity and strength of the final product.
-
Environmental and Economic Impact:
- Sintering is an environmentally friendly process due to reduced material waste and energy consumption.
- It is economically beneficial as it lowers production costs and increases efficiency, making it a preferred method in various industries.
By understanding these key points, one can appreciate the significance of sintered metal in modern manufacturing and its wide-ranging applications across different industries.
Summary Table:
Aspect | Details |
---|---|
Definition | Metal parts created by sintering compacted metal powder. |
Process Steps | Blending, Compaction, Sintering. |
Materials Used | Tungsten, Molybdenum, Ceramics, Glass, Steel. |
Key Benefits | Versatility, Efficiency, Cost-Effectiveness, Complexity, Environmental Impact, Quality. |
Applications | Steel production, Ceramics, Glass manufacturing. |
Temperature Control | Below melting point to fuse particles without liquefaction. |
Interested in sintered metal solutions for your industry? Contact our experts today to learn more!