Sintering in hydrogen is a specialized process where materials, typically in powder form, are heated in a hydrogen-rich atmosphere to form a solid mass without reaching the material's melting point. This process is particularly beneficial for producing high-quality, dense materials with superior mechanical properties. Hydrogen sintering prevents oxidation, reduces impurities, and enhances the overall quality of the final product. It is widely used in industries requiring high-performance materials, such as aerospace, automotive, and electronics, due to its ability to produce parts with excellent surface finishes and mechanical properties.
Key Points Explained:
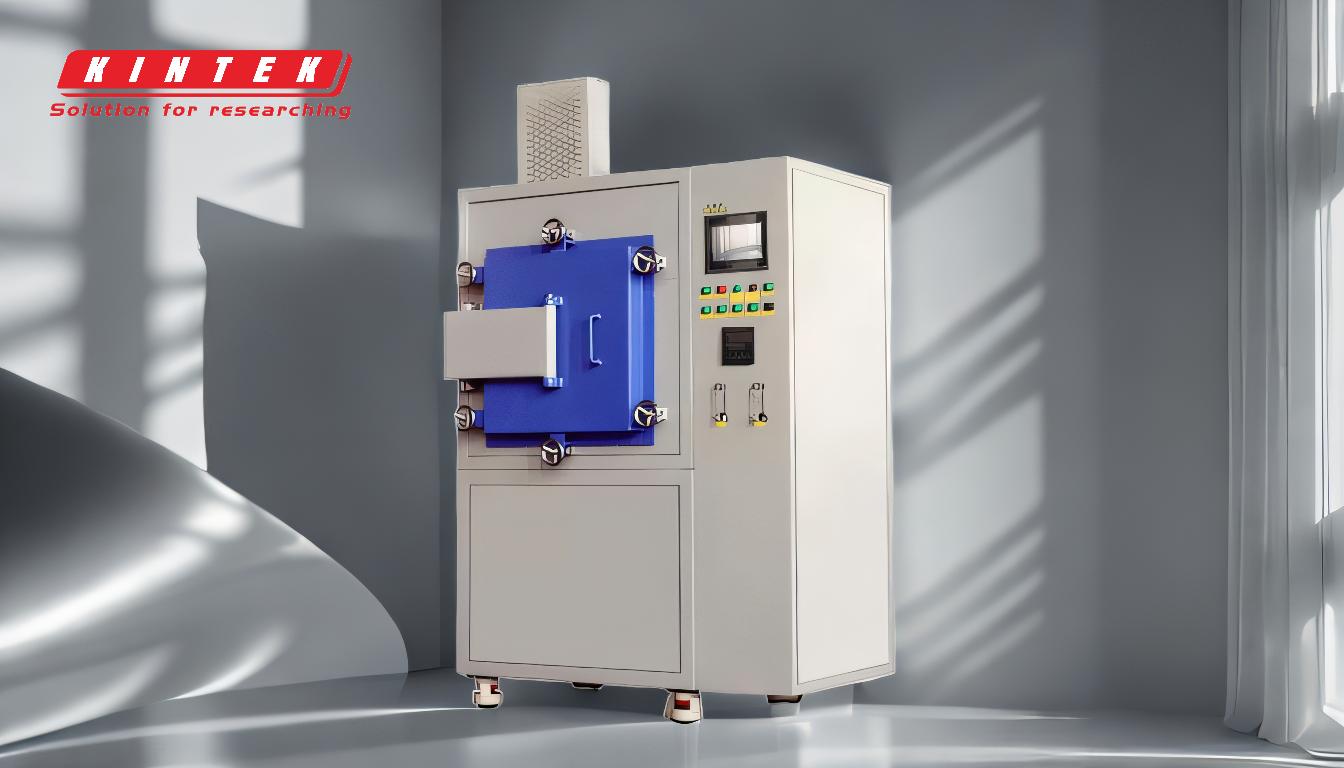
-
Definition of Sintering in Hydrogen:
- Sintering in hydrogen involves heating powdered materials in a hydrogen-rich atmosphere (pure hydrogen, hydrogen/nitrogen mixture, or dissociated ammonia) to form a solid mass.
- This process is particularly effective for materials like tungsten, molybdenum, and stainless steel, where high purity and density are critical.
-
Role of Hydrogen in the Sintering Process:
- Oxidation Prevention: Hydrogen acts as a reducing agent, preventing the oxidation of metal powders, which can otherwise lead to poor sintering results.
- Impurity Reduction: Hydrogen reacts with surface oxides and impurities like silica, effectively stripping them away from the alloy. This is crucial for achieving high-density materials with superior mechanical properties.
- Enhanced Redox Reactions: The hydrogen atmosphere facilitates redox reactions, which help in eliminating impurities and improving the overall quality of the sintered product.
-
Benefits of Using Hydrogen in Sintering:
- High Purity: Hydrogen used in sintering is typically of very high purity (>99.9995%), making it suitable for a wide range of materials, including those used in critical applications.
- Improved Mechanical Properties: The reduction of impurities and prevention of oxidation lead to sintered parts with superior mechanical qualities, such as higher strength and durability.
- Surface Finish: The use of hydrogen results in a bright, clean surface finish, which is often desirable in final products.
- Environmental and Safety Benefits: Hydrogen sintering reduces air pollution and minimizes risks to personnel, making it a safer and more environmentally friendly option compared to other sintering methods.
-
Hydrogen Sintering Furnace:
- Design and Components: A hydrogen sintering furnace typically uses molybdenum or tungsten wire as the heating element and molybdenum as the heat shield. The furnace body is usually made of stainless steel or carbon steel.
- Operation: The furnace operates under a hydrogen gas atmosphere, which is essential for high-temperature sintering of materials like tungsten and molybdenum. The hydrogen atmosphere ensures that the materials are protected from oxidation and other contaminants during the sintering process.
-
Applications of Hydrogen Sintering:
- Aerospace and Automotive Industries: Hydrogen sintering is used to produce high-performance components that require exceptional mechanical properties and durability.
- Electronics: The process is also used in the electronics industry to manufacture components with high precision and reliability.
- Medical Devices: Hydrogen sintering is employed in the production of medical devices where high purity and biocompatibility are essential.
-
Comparison with Other Sintering Methods:
- Advantages Over Air Sintering: Unlike sintering in air, which can lead to oxidation and contamination, hydrogen sintering provides a clean, reducing atmosphere that enhances the quality of the final product.
- Cost Efficiency: Although hydrogen sintering requires specialized equipment, the process can lead to substantial savings in the long run due to reduced material waste and improved product quality.
In summary, sintering in hydrogen is a highly effective process for producing high-quality, dense materials with superior mechanical properties. The use of hydrogen prevents oxidation, reduces impurities, and enhances the overall quality of the sintered product, making it an ideal choice for industries that demand high-performance materials.
Summary Table:
Aspect | Details |
---|---|
Process | Heating powdered materials in a hydrogen-rich atmosphere to form a solid mass. |
Key Benefits | Prevents oxidation, reduces impurities, enhances mechanical properties. |
Materials | Tungsten, molybdenum, stainless steel, and other high-purity alloys. |
Applications | Aerospace, automotive, electronics, and medical devices. |
Advantages Over Air | Cleaner process, higher quality, and cost-efficient in the long term. |
Learn how hydrogen sintering can elevate your material quality—contact our experts today!