Sintering of powder metals is a critical process in powder metallurgy where compacted metal powders are heated to a temperature just below their melting point. This causes the metal particles to bond together, enhancing the part's strength, hardness, and structural integrity. Sintering is a versatile and cost-effective manufacturing method that allows for the production of intricate and complex metal components, such as gears, camshafts, and cutting tools, without requiring solid-liquid phase changes. It is widely used in industries like automotive and tool manufacturing due to its flexibility and ability to retain the beneficial properties of the metal.
Key Points Explained:
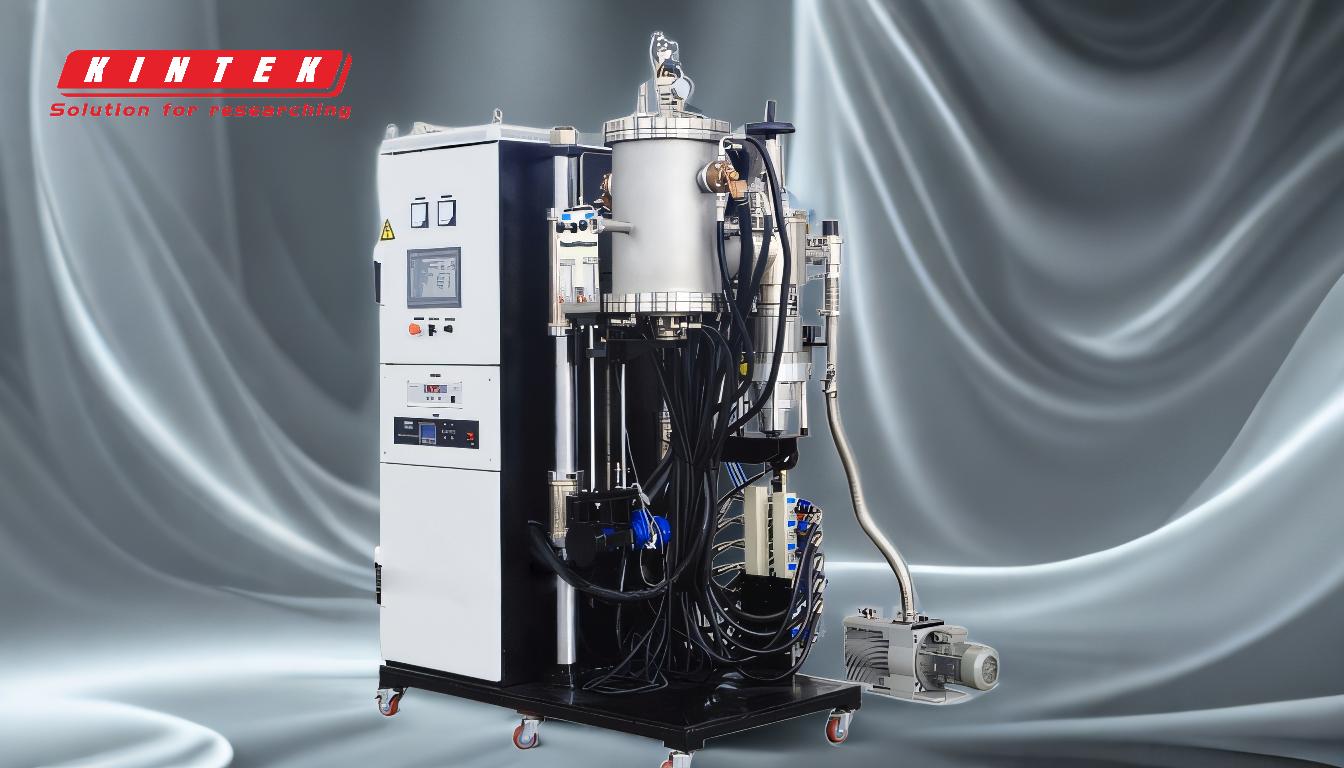
-
Definition of Sintering:
- Sintering is a heat treatment process in powder metallurgy where compacted metal powders are heated to a temperature just below their melting point.
- This process causes the metal particles to bond together through diffusion, resulting in a solid and cohesive structure.
-
Purpose of Sintering:
- Enhanced Strength and Hardness: Sintering imparts strength and integrity to the metal part by bonding the particles together.
- Shape Retention: It ensures the part retains its intended shape after compaction.
- Retention of Beneficial Properties: Unlike melting, sintering allows the metal to retain its original properties, such as porosity or specific mechanical characteristics.
-
Process Details:
- Temperature Control: Sintering occurs at temperatures below the melting point of the primary metal constituent, preventing complete liquefaction.
- Particle Bonding: The heat causes the metal particles to approach and weld together at their contact points, similar to how ice cubes fuse in water.
- Compaction Precedes Sintering: The metal powder is first compacted into the desired shape before being sintered.
-
Advantages of Sintering:
- Flexibility: Sintering can produce complex shapes and intricate parts that are difficult or impossible to achieve with traditional methods like casting or forging.
- Cost-Effectiveness: It reduces material waste and eliminates the need for extensive machining.
- Wide Material Compatibility: Sintering works with various metals and alloys, making it suitable for diverse applications.
-
Applications of Sintering:
- Automotive Industry: Used to manufacture components like gears, camshafts, and valve seats.
- Cutting Tools: Produces durable and precise tools.
- Filters and Porous Components: Creates sintered filters and other porous structures.
-
Comparison to Traditional Manufacturing:
- Unlike casting, forging, or extrusion, sintering does not involve a solid-liquid phase change, which simplifies the process and reduces energy consumption.
- It is particularly advantageous for producing small, intricate parts with high precision.
-
Mechanism of Sintering:
- Diffusion: Heat causes atoms to diffuse across particle boundaries, leading to bonding.
- Grain Growth: Over time, the particles fuse, and the material's grain structure evolves, enhancing its mechanical properties.
-
Industrial Relevance:
- Sintering is a cornerstone of powder metallurgy, enabling the production of high-performance components with minimal material waste.
- Its ability to create near-net-shape parts reduces the need for secondary processing, making it a preferred method for mass production.
By understanding sintering, manufacturers can leverage its benefits to produce durable, precise, and cost-effective metal components for a wide range of industries.
Summary Table:
Aspect | Details |
---|---|
Definition | Heat treatment process bonding metal particles below melting point. |
Purpose | Enhances strength, hardness, and shape retention. |
Process | Compaction followed by controlled heating for particle bonding. |
Advantages | Flexibility, cost-effectiveness, and compatibility with various metals. |
Applications | Automotive parts, cutting tools, and porous components. |
Industrial Relevance | Enables high-performance, near-net-shape parts with minimal material waste. |
Discover how sintering can revolutionize your manufacturing process—contact us today!