Sintering is a critical process in additive manufacturing (AM) that involves compacting and bonding powdered materials into solid structures using heat and pressure, without melting the material completely. This process is essential for creating complex, high-precision components with enhanced mechanical properties such as hardness, toughness, and durability. In AM, sintering techniques like selective laser sintering (SLS) and electron beam sintering (EBS) are used to layer and fuse powdered materials based on digital designs, enabling the production of intricate 3D objects. Sintering is particularly valuable for materials with high melting points, such as metals and ceramics, and is widely used in industries like aerospace, automotive, and healthcare for producing functional, dense, and cost-effective parts.
Key Points Explained:
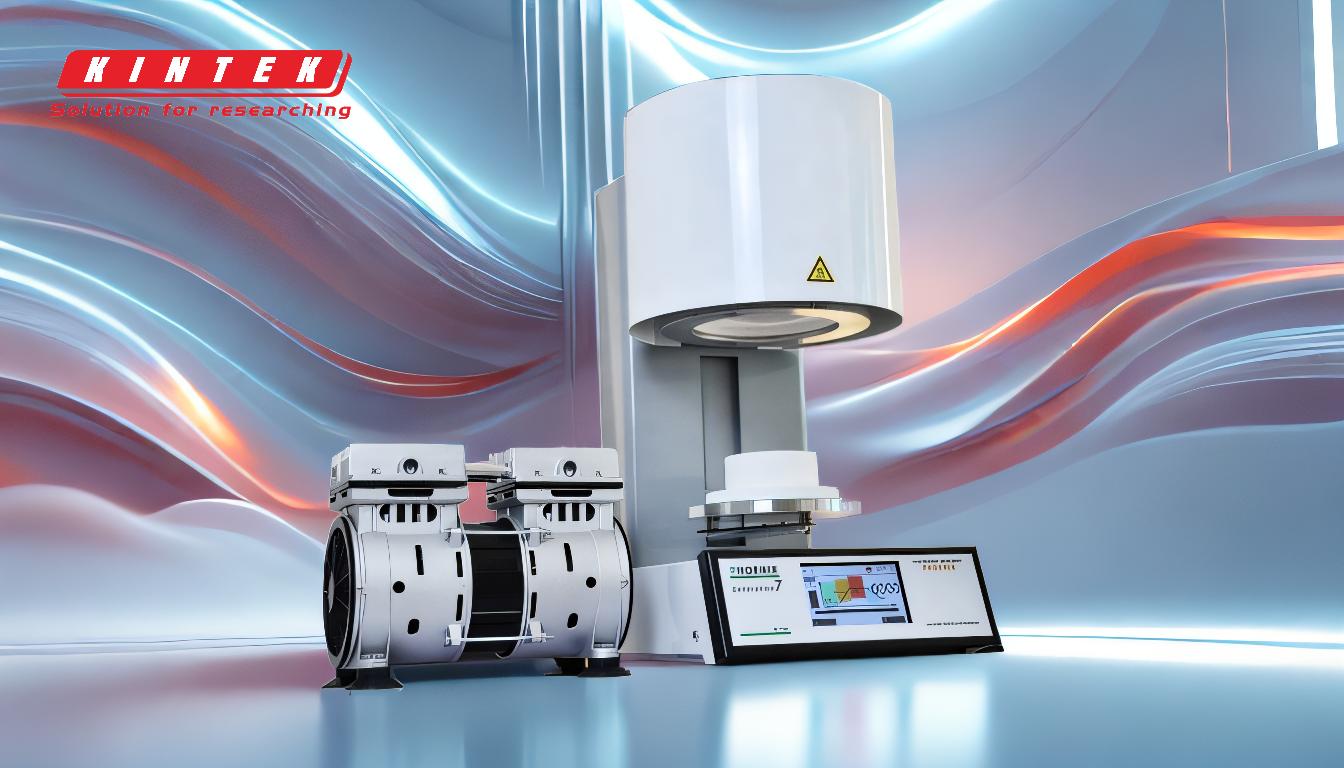
-
Definition and Purpose of Sintering:
- Sintering is a manufacturing process that compacts and bonds powdered materials into solid structures by applying heat and pressure, without fully melting the material.
- It enhances the mechanical properties of materials, such as hardness, toughness, and durability, making it ideal for producing high-performance components.
- The process is widely used in powder metallurgy, ceramics, and additive manufacturing to create complex shapes and geometries that are difficult to achieve with traditional methods.
-
How Sintering Works:
- During sintering, heat and pressure cause the atoms in the powdered material to diffuse across particle boundaries, fusing them together into a solid mass.
- The temperature used is below the material's melting point, ensuring that the material retains its shape while becoming denser and stronger.
- This process is particularly useful for materials with extremely high melting points, such as tungsten and molybdenum, which are challenging to process using conventional methods.
-
Role of Sintering in Additive Manufacturing:
- In additive manufacturing, sintering is used in techniques like selective laser sintering (SLS) and electron beam sintering (EBS) to create 3D objects layer by layer.
- A digital design guides the selective sintering of powdered materials, enabling the production of intricate and precise components.
- Sintering in AM allows for the consolidation of powdered materials into fully dense and functional parts, making it suitable for rapid prototyping and mass production.
-
Advantages of Sintering in Additive Manufacturing:
- Complex Geometries: Sintering enables the creation of intricate shapes and internal structures that are difficult or impossible to achieve with traditional manufacturing methods.
- Material Efficiency: The process minimizes material waste, as unused powder can often be recycled for future builds.
- Cost-Effectiveness: Sintering reduces the need for expensive tooling, making it a cost-effective solution for producing complex parts.
- Enhanced Properties: The resulting parts exhibit improved mechanical properties, such as strength, wear resistance, and thermal stability.
-
Applications of Sintering in Additive Manufacturing:
- Aerospace: Sintered components are used in aircraft and spacecraft due to their high strength-to-weight ratio and ability to withstand extreme conditions.
- Automotive: Sintering is employed to produce lightweight, durable parts for engines, transmissions, and other critical systems.
- Healthcare: The process is used to create customized medical implants and prosthetics with precise geometries and biocompatible materials.
- Electronics: Sintering is utilized to manufacture components like heat sinks, connectors, and sensors with high thermal and electrical conductivity.
-
Challenges and Limitations:
- Material Constraints: Not all materials are suitable for sintering, and the process may require specialized powders with specific properties.
- Surface Finish: Sintered parts may have a rough surface finish, requiring post-processing to achieve the desired quality.
- Dimensional Accuracy: Achieving high dimensional accuracy can be challenging, especially for complex geometries.
- Energy Consumption: The process can be energy-intensive due to the high temperatures required.
-
Future Trends in Sintering for Additive Manufacturing:
- Advanced Materials: Research is ongoing to develop new materials and powders optimized for sintering, expanding its applications.
- Hybrid Processes: Combining sintering with other manufacturing techniques, such as machining or coating, to enhance part performance and functionality.
- Automation and AI: Integrating automation and artificial intelligence to improve process control, reduce waste, and increase production efficiency.
- Sustainability: Developing more energy-efficient sintering methods and using recycled materials to reduce the environmental impact.
In conclusion, sintering is a transformative process in additive manufacturing, enabling the production of complex, high-performance components with enhanced mechanical properties. Its applications span various industries, and ongoing advancements in materials and technology promise to further expand its capabilities and efficiency.
Summary Table:
Aspect | Details |
---|---|
Definition | Compacts and bonds powdered materials using heat and pressure. |
Key Techniques | Selective Laser Sintering (SLS), Electron Beam Sintering (EBS). |
Advantages | Complex geometries, material efficiency, cost-effectiveness, enhanced properties. |
Applications | Aerospace, automotive, healthcare, electronics. |
Challenges | Material constraints, surface finish, dimensional accuracy, energy consumption. |
Future Trends | Advanced materials, hybrid processes, automation, sustainability. |
Discover how sintering can revolutionize your manufacturing process—contact us today!