Sintering is a critical process in the steel industry, where powdered materials, such as iron ore, are compacted and heated below their melting point to form dense, strong, and porous materials. This process enhances the mechanical properties of the materials, reduces porosity, and improves their suitability for use in blast furnaces. Sintering involves mixing iron ore powder with coke and lime, igniting the mixture, and drawing air through it to create a combustion reaction. The resulting sintered ore is used as clinker in ironmaking, improving blast furnace efficiency and reducing costs. Sintering is also used in other industries, such as ceramics and additive manufacturing, to create complex shapes and high-performance materials.
Key Points Explained:
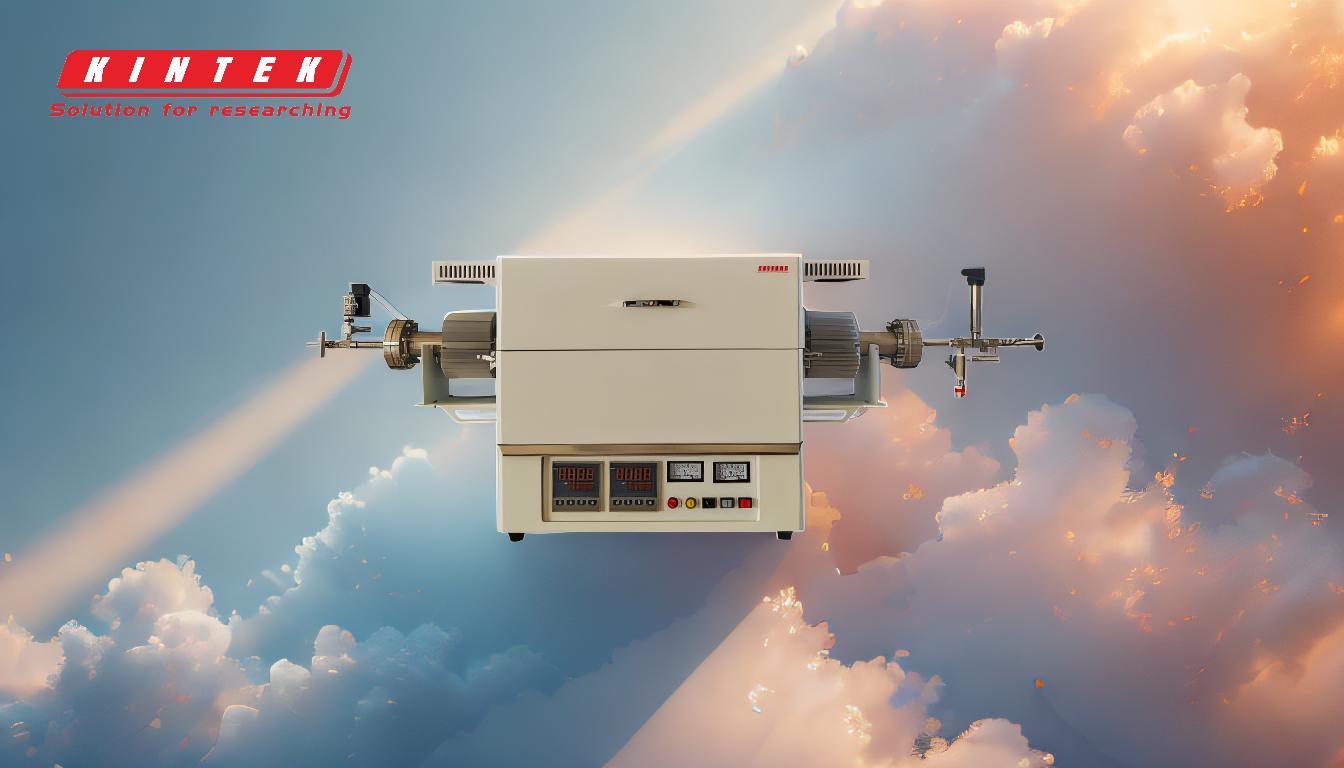
-
Definition and Purpose of Sintering:
- Sintering is a process that compacts and fuses powdered materials, such as iron ore, using heat and pressure below the material's melting point.
- The primary purpose is to enhance the material's mechanical properties, such as strength, toughness, and porosity, making it suitable for industrial applications like steel production.
-
Materials Used in Sintering:
- In the steel industry, sintering typically involves a mixture of iron ore powder, coke (a form of coal), and lime.
- These materials are combined in specific ratios to ensure the sintered product has the desired strength and granularity.
-
The Sintering Process:
- The mixture is placed on a traveling grate and ignited using a gas burner.
- Air is drawn through the bed to initiate a combustion reaction, generating high heat.
- This heat causes the tiny metal particles to fuse together, forming lumps or clinker.
- The sintered product is then cooled and crushed to the appropriate size for use in blast furnaces.
-
Role in Steel Production:
- Sintered ore serves as a key raw material in blast furnaces for ironmaking.
- It improves the utilization coefficient of blast furnaces, reduces the coking ratio, and enhances furnace permeability, ensuring smooth and efficient operation.
- By using sintered ore, steel producers can achieve cost savings and better control over the quality of the final product.
-
Benefits of Sintering:
- Enhanced Material Properties: Sintering reduces porosity and improves strength, toughness, and thermal conductivity.
- Cost Efficiency: The process allows for the use of lower-cost raw materials and reduces energy consumption compared to melting.
- Versatility: Sintering can be used to create complex shapes and intricate geometries that are difficult to achieve with traditional manufacturing methods.
- Environmental Benefits: By improving blast furnace efficiency, sintering helps reduce carbon emissions and waste.
-
Applications Beyond Steel:
- Sintering is also used in the production of ceramics, glass, and refractory metals like tungsten and molybdenum.
- In additive manufacturing (3D printing), sintering is used to create high-performance metal parts with precise dimensions and intricate designs.
-
Comparison with Other Processes:
- Unlike melting, sintering does not require the material to reach its melting point, making it suitable for materials with high melting temperatures.
- It is a more energy-efficient process compared to melting and casting, as it operates at lower temperatures.
-
Challenges and Considerations:
- The sintering process requires precise control over temperature, pressure, and material composition to ensure consistent quality.
- Dust and emissions generated during sintering must be managed to meet environmental regulations.
By understanding the sintering process, steel manufacturers can optimize their operations, improve product quality, and reduce costs, making it a vital component of modern industrial production.
Summary Table:
Aspect | Details |
---|---|
Definition | Compacts and fuses powdered materials using heat and pressure below melting. |
Materials Used | Iron ore powder, coke, and lime. |
Process | Mixture ignited, air drawn through, particles fuse to form clinker. |
Role in Steel Production | Improves blast furnace efficiency and reduces costs. |
Benefits | Enhanced strength, cost efficiency, versatility, environmental benefits. |
Applications | Steel, ceramics, glass, refractory metals, additive manufacturing. |
Challenges | Requires precise control of temperature, pressure, and dust management. |
Optimize your steel production with sintering—contact our experts today for tailored solutions!