Slow and fast pyrolysis are two distinct thermal decomposition processes used to convert biomass into valuable products. Slow pyrolysis is a prolonged process taking several hours, primarily yielding biochar, a solid carbon-rich material. Fast pyrolysis, in contrast, is a rapid process completed in seconds, producing a higher yield of bio-oil (60%), along with biochar (20%) and syngas (20%). Fast pyrolysis requires high heating rates, finely ground feedstock, controlled temperatures around 500°C, and rapid cooling of vapors. It is more efficient in terms of energy input relative to output and is favored for biofuel production, while slow pyrolysis is ideal for biochar generation.
Key Points Explained:
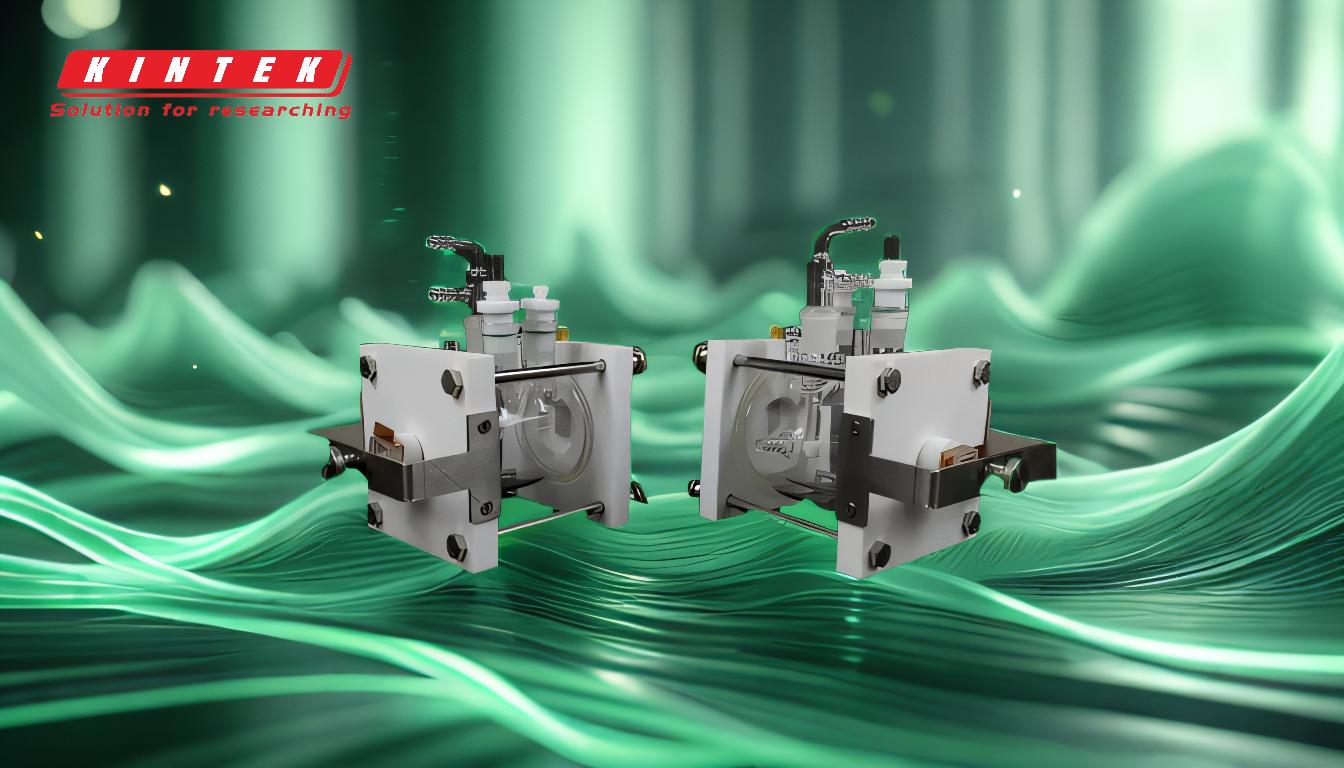
-
Definition and Purpose:
- Slow Pyrolysis: A thermal decomposition process that occurs over several hours, primarily aimed at producing biochar. It is a slower, more controlled process that maximizes the yield of solid carbonaceous material.
- Fast Pyrolysis: A rapid thermal decomposition process completed in seconds, designed to maximize the production of bio-oil, a liquid fuel, along with biochar and syngas. It is optimized for high yields of biofuel.
-
Process Duration:
- Slow Pyrolysis: Takes several hours to complete, allowing for a slower breakdown of biomass and favoring the formation of biochar.
- Fast Pyrolysis: Completes in seconds, requiring very high heating rates and rapid cooling to maximize the yield of bio-oil.
-
Primary Products:
- Slow Pyrolysis: Primarily produces biochar, a solid carbon-rich material used in soil amendment, carbon sequestration, and as a fuel.
- Fast Pyrolysis: Yields 60% bio-oil, 20% biochar, and 20% syngas. The bio-oil can be used as a renewable fuel or further refined into chemicals.
-
Temperature and Heating Rates:
- Slow Pyrolysis: Operates at lower heating rates and temperatures, typically below 500°C, allowing for a more gradual decomposition of biomass.
- Fast Pyrolysis: Requires very high heating and heat transfer rates, with controlled reaction temperatures around 500°C. The rapid heating ensures the biomass is quickly converted into vapors, which are then rapidly cooled to form bio-oil.
-
Feedstock Preparation:
- Slow Pyrolysis: Can handle a wider range of feedstock sizes, including larger particles, due to the slower process.
- Fast Pyrolysis: Requires finely ground feed to ensure uniform heating and efficient conversion into bio-oil.
-
Energy Efficiency:
- Slow Pyrolysis: Generally requires more energy input relative to the energy output, as the process is slower and less efficient in converting biomass into usable energy.
- Fast Pyrolysis: More energy-efficient, with less energy input required relative to the energy output, making it a more sustainable option for biofuel production.
-
Applications:
- Slow Pyrolysis: Ideal for applications where biochar is the desired product, such as in agriculture for soil improvement or in carbon sequestration projects.
- Fast Pyrolysis: Preferred for biofuel production, where the goal is to maximize the yield of liquid fuels like bio-oil, which can be used directly or further processed into transportation fuels.
-
Residence Time:
- Slow Pyrolysis: The residence time is significantly longer, allowing for a more complete conversion of biomass into biochar.
- Fast Pyrolysis: The residence time is extremely short, around 5 seconds, which is crucial for maximizing the yield of bio-oil.
-
Cooling Requirements:
- Slow Pyrolysis: Less emphasis on rapid cooling, as the primary product is a solid.
- Fast Pyrolysis: Requires rapid cooling of pyrolysis vapors to condense them into bio-oil, which is a critical step in the process.
-
Environmental Impact:
- Slow Pyrolysis: Produces a stable form of carbon (biochar) that can be used to sequester carbon in soils, reducing greenhouse gas emissions.
- Fast Pyrolysis: Produces renewable fuels that can replace fossil fuels, reducing overall carbon emissions and contributing to a more sustainable energy system.
In summary, slow and fast pyrolysis are tailored for different end products and applications. Slow pyrolysis is best suited for biochar production, while fast pyrolysis is optimized for bio-oil and biofuel production. Each method has its unique requirements and benefits, making them suitable for different industrial and environmental applications.
Summary Table:
Aspect | Slow Pyrolysis | Fast Pyrolysis |
---|---|---|
Process Duration | Several hours | Seconds |
Primary Products | Biochar (solid carbon-rich material) | Bio-oil (60%), Biochar (20%), Syngas (20%) |
Temperature | Below 500°C | Around 500°C |
Heating Rates | Lower | Very high |
Feedstock Preparation | Handles larger particles | Requires finely ground feedstock |
Energy Efficiency | Less efficient (higher energy input relative to output) | More efficient (lower energy input relative to output) |
Applications | Biochar production (soil amendment, carbon sequestration) | Biofuel production (bio-oil for renewable fuels) |
Residence Time | Longer (hours) | Extremely short (seconds) |
Cooling Requirements | Less emphasis on rapid cooling | Requires rapid cooling of vapors |
Environmental Impact | Carbon sequestration, reduces greenhouse gas emissions | Produces renewable fuels, reduces fossil fuel dependency |
Discover the best pyrolysis solution for your needs—contact our experts today!