Sputter coating is a physical vapor deposition (PVD) process used to apply a thin, functional coating onto a substrate. It involves creating a plasma by electrically charging a sputtering cathode, which ejects material from a target surface (often gold or other metals) and deposits it onto the substrate. This process is widely used in applications like scanning electron microscopy (SEM) to improve secondary electron emission, reduce thermal damage, and prevent charging on non-conductive specimens. Sputter coating ensures a uniform, durable, and atomic-level bond between the coating and the substrate, making it a critical technique in nanotechnology and materials science.
Key Points Explained:
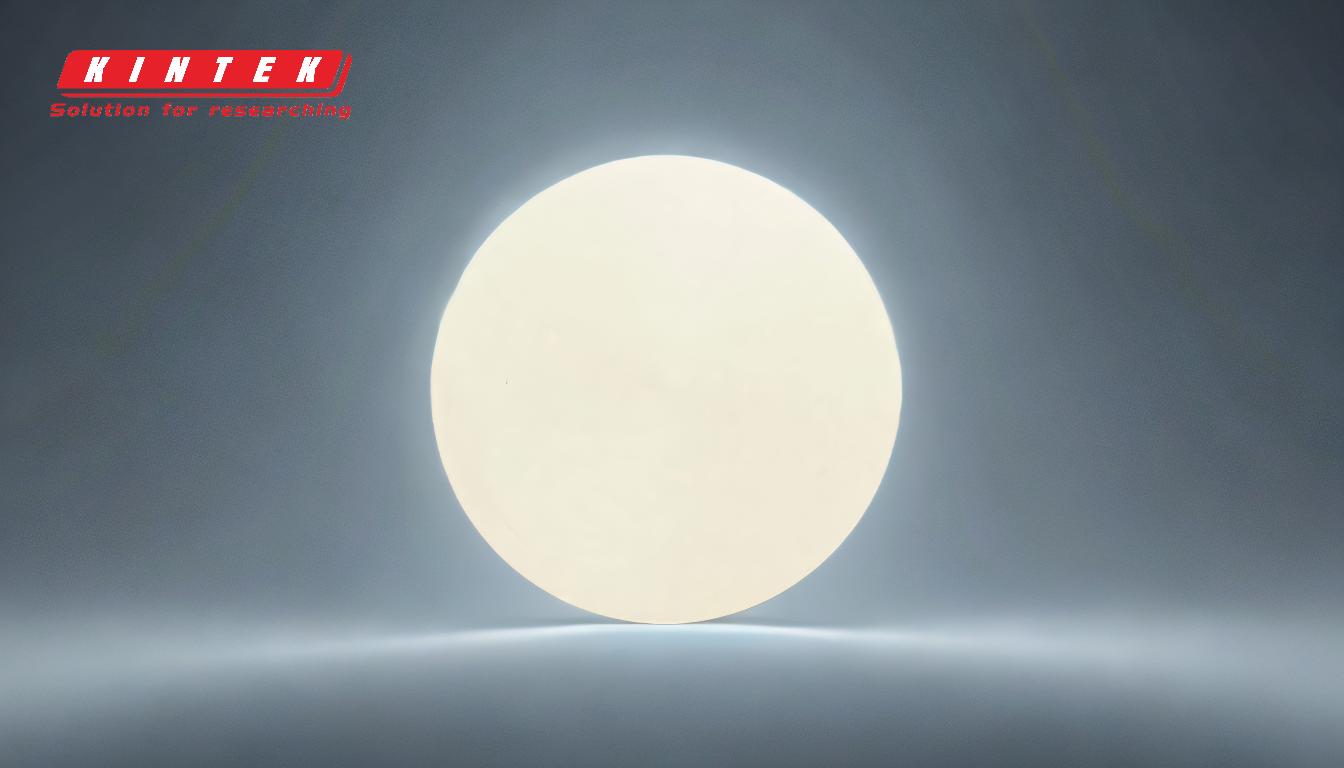
-
What is Sputter Coating?
- Sputter coating is a physical vapor deposition (PVD) process.
- It involves creating a plasma by electrically charging a sputtering cathode.
- The plasma causes material to be ejected from a target surface (e.g., gold) and deposited onto a substrate.
- The process is omni-directional, ensuring even coating across the surface.
-
How Does Sputter Coating Work?
- A glow discharge is formed between a cathode and anode using a gas (typically argon).
- Gas ions bombard the target material, causing it to erode or "sputter."
- The sputtered atoms are deposited onto the substrate in a fine, microscopic layer.
- Magnets are often used to stabilize the plasma and ensure uniform erosion of the target material.
-
Why is Sputter Coating Done?
- Improved Conductivity: Sputter coating is commonly used to coat non-conductive specimens (e.g., biological samples) with a conductive layer (e.g., gold) to prevent charging during SEM imaging.
- Enhanced Secondary Electron Emission: The coating improves the emission of secondary electrons, which is crucial for high-resolution imaging in SEM.
- Reduced Thermal Damage: The process minimizes heat transfer to the substrate, protecting sensitive materials.
- Uniform and Durable Coating: The atomic-level bond between the coating and substrate ensures a consistent and long-lasting layer.
-
Advantages of Sputter Coating:
- Uniform Deposition: The stable plasma ensures even coating across complex geometries.
- Atomic-Level Bonding: The coating becomes a permanent part of the substrate, rather than just a surface layer.
- Versatility: Can be used with a wide range of materials, including metals and insulators.
- Low Thermal Impact: The process generates minimal heat, making it suitable for heat-sensitive materials.
-
Applications of Sputter Coating:
- Scanning Electron Microscopy (SEM): Coating non-conductive specimens to improve imaging quality.
- Nanotechnology: Creating thin films for electronic devices, sensors, and optical coatings.
- Materials Science: Enhancing surface properties like wear resistance, corrosion resistance, and conductivity.
- Decorative Coatings: Applying thin, durable layers for aesthetic purposes.
-
Challenges and Limitations:
- Deposition Rate: Early methods like DC diode sputtering had low deposition rates, though modern techniques have improved this.
- Complexity: Advanced systems (e.g., DC triple or quadrupole sputtering) require specialized equipment and expertise.
- Material Limitations: Some insulating materials are difficult to sputter without modifications to the process.
-
Evolution of Sputter Coating Technology:
- Early methods like DC diode sputtering were simple but had limitations such as low deposition rates and inability to handle insulating materials.
- Modern advancements, such as DC triple and quadrupole sputtering, have improved ionization and stabilized discharge, though they are still not widely adopted in industrial settings.
In summary, sputter coating is a versatile and essential technique for creating thin, functional coatings with applications ranging from microscopy to nanotechnology. Its ability to produce uniform, durable, and atomic-level bonds makes it a valuable tool in both research and industry.
Summary Table:
Aspect | Details |
---|---|
Process | Physical vapor deposition (PVD) using plasma to eject and deposit material. |
Key Benefits | Uniform coating, atomic-level bonding, low thermal impact, versatility. |
Applications | SEM imaging, nanotechnology, materials science, decorative coatings. |
Challenges | Low deposition rates, complexity, material limitations. |
Discover how sputter coating can enhance your research or industrial processes—contact us today for expert guidance!