Sputtering in plasma treatment is a physical vapor deposition (PVD) technique used to create thin films on substrates. It involves bombarding a target material with high-energy ions, typically from an inert gas like argon, to eject atoms from the target. These ejected atoms then deposit onto a substrate, forming a thin, uniform coating. Sputtering is widely used in applications such as semiconductor manufacturing, optical coatings, and scanning electron microscopy (SEM) for coating specimens with conductive films. It is particularly advantageous for heat-sensitive materials and complex geometries due to its low-temperature process and ability to coat three-dimensional surfaces uniformly.
Key Points Explained:
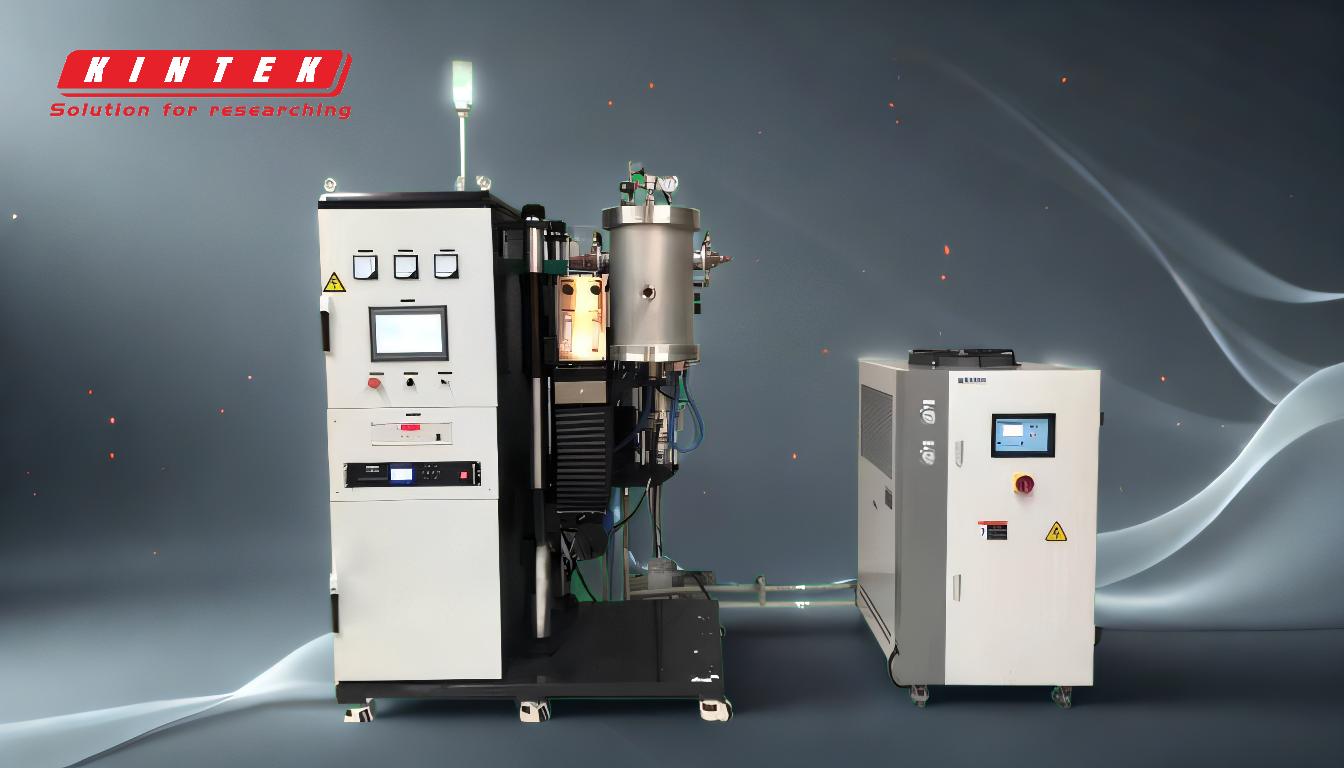
-
Mechanism of Sputtering:
- Sputtering involves bombarding a target material with high-energy ions, usually from an inert gas like argon.
- The ions collide with the target atoms, transferring enough energy to dislodge them from the surface. These ejected atoms are then deposited onto a substrate to form a thin film.
- This process is driven by a plasma, which is created when a high voltage is applied to the target, ionizing the gas and accelerating the ions toward the target.
-
Role of Plasma in Sputtering:
- Plasma is essential for sputtering as it provides the high-energy ions needed to bombard the target.
- The plasma glow observed during sputtering is caused by the recombination of positively charged ions with free electrons, releasing energy in the form of light.
- The plasma ensures a controlled environment where the ions can effectively eject atoms from the target without reacting with the substrate.
-
Applications of Sputtering:
- SEM Specimen Coating: Sputtering is extensively used in SEM to coat non-conductive specimens with a thin, conductive metal film, enabling high-resolution imaging.
- Thin Film Deposition: It is widely used in semiconductor manufacturing, optical coatings, and protective coatings due to its ability to deposit uniform, high-quality films.
- Heat-Sensitive Materials: Sputtering is ideal for coating heat-sensitive materials, such as biological samples, because the process occurs at low temperatures.
-
Advantages of Sputtering:
- Uniform Coatings: Sputtering can coat complex, three-dimensional surfaces uniformly, making it suitable for intricate geometries.
- Low-Temperature Process: The low-temperature nature of sputtering makes it compatible with heat-sensitive materials.
- Versatility: It can deposit a wide range of materials, including metals, alloys, and insulators, with precise control over film thickness and composition.
-
Types of Sputtering:
- Magnetron Sputtering: This variant uses magnetic fields to trap electrons near the target surface, increasing the ionization of the gas and enhancing the sputtering rate. It is highly efficient and widely used in industrial applications.
- RF Sputtering: Used for insulating materials, RF sputtering applies an alternating current to the target, preventing charge buildup and enabling the deposition of non-conductive films.
-
Process Conditions:
- Inert Gas Requirement: The gas used for sputtering must be inert (e.g., argon) to avoid chemical reactions with the substrate or target material.
- Pressure and Distance: Sputtering requires a controlled vacuum environment with low but not extremely low pressure. The substrate must be placed close to the target to ensure effective deposition.
-
Material Compatibility:
- Sputtering is effective for materials with extremely high melting points, such as carbon and silicon, as well as alloys and compounds.
- It can deposit a wide range of materials, from metals to ceramics, making it a versatile technique for various industries.
By understanding these key points, one can appreciate the versatility and precision of sputtering in plasma treatment, making it a critical process in modern manufacturing and research applications.
Summary Table:
Aspect | Details |
---|---|
Mechanism | Bombarding target material with high-energy ions to eject atoms for deposition. |
Role of Plasma | Provides high-energy ions and ensures a controlled environment. |
Applications | SEM specimen coating, semiconductor manufacturing, optical coatings. |
Advantages | Uniform coatings, low-temperature process, versatile material compatibility. |
Types | Magnetron sputtering, RF sputtering. |
Process Conditions | Requires inert gas, controlled vacuum, and precise substrate placement. |
Material Compatibility | Metals, alloys, insulators, ceramics, and high-melting-point materials. |
Discover how sputtering can enhance your manufacturing or research processes—contact our experts today!