Sputtering is a physical vapor deposition (PVD) technique used to deposit thin films onto substrates. It involves creating a plasma in a vacuum chamber by ionizing an inert gas, typically argon. The plasma generates high-energy ions that bombard a target material, dislodging atoms or molecules from its surface. These dislodged particles form a vapor stream that deposits onto a substrate, creating a thin film. Sputtering is widely used in industries like semiconductors, optics, and solar panels due to its ability to produce uniform, high-quality films with precise control over thickness and composition.
Key Points Explained:
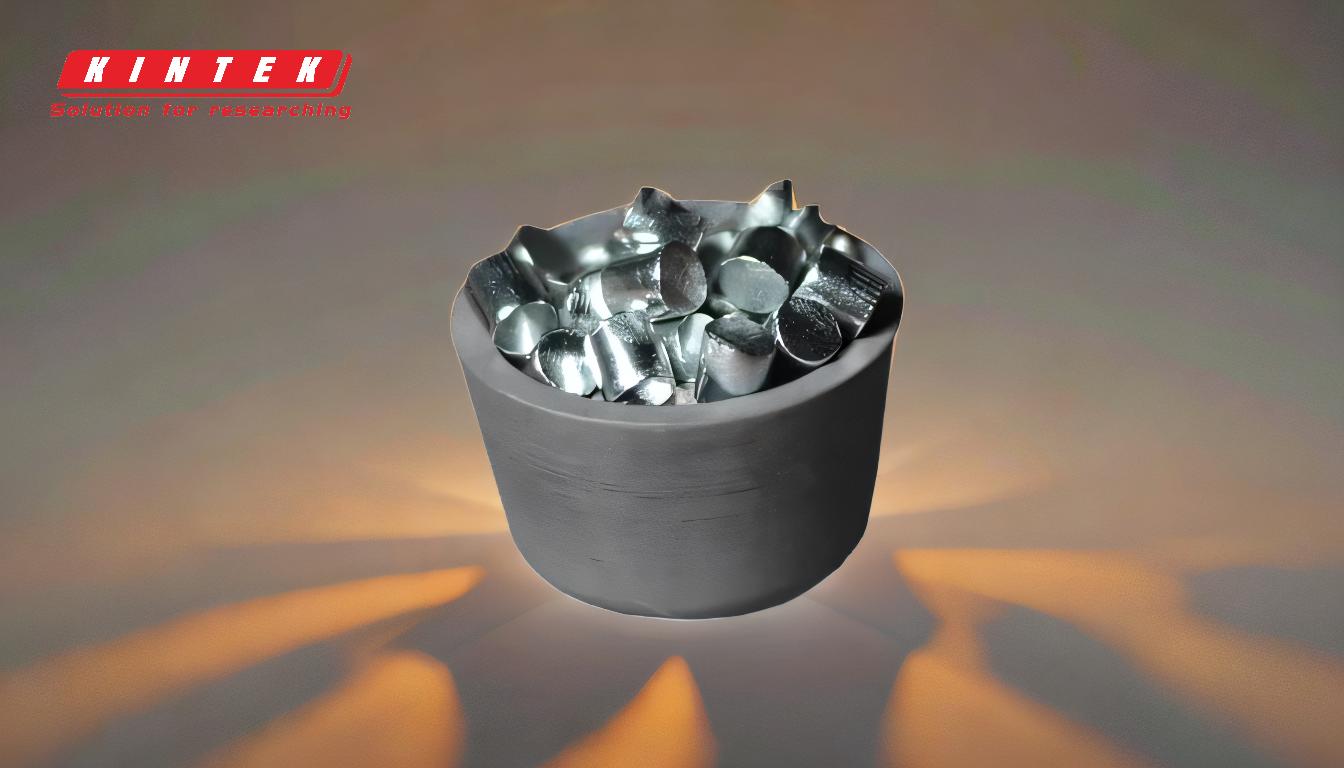
-
Basic Mechanism of Sputtering:
- Sputtering occurs in a vacuum chamber where an inert gas, usually argon, is introduced.
- A cathode is electrically energized to generate a plasma, ionizing the gas atoms.
- The positively charged argon ions are accelerated toward a target material due to the electric field.
- Upon collision, the ions dislodge atoms or molecules from the target material, creating a vapor stream.
- This vapor stream deposits onto a substrate, forming a thin film.
-
Role of Plasma and Collision Cascade:
- Plasma is a key component in sputtering, as it provides the energy needed to ionize the gas and accelerate ions toward the target.
- When the ions collide with the target, they trigger a "collision cascade," where energy is transferred through the target material, ejecting atoms from its surface.
- This process ensures that the ejected particles are atom-sized, allowing for precise and uniform deposition.
-
Advantages of Sputtering:
- Uniform Deposition: Sputtering produces highly uniform thin films, making it ideal for applications requiring consistent coating thickness.
- Low Residual Stress: The process densifies the deposited film and reduces residual stress, especially at lower deposition temperatures.
- Precise Control: Film thickness can be precisely controlled by adjusting deposition time and other parameters.
- Versatility: Sputtering can deposit a wide range of materials, including metals, alloys, and ceramics, onto various substrates.
-
Applications of Sputtering:
- Semiconductors: Used to deposit thin films of conductive and insulating materials on silicon wafers.
- Optics: Applied in the production of anti-reflective coatings, mirrors, and optical filters.
- Solar Panels: Used to deposit thin films of photovoltaic materials for efficient energy conversion.
- Decorative Coatings: Employed to create durable and aesthetically pleasing coatings on consumer products.
-
Key Components of a Sputtering System:
- Vacuum Chamber: Maintains a controlled environment free of contaminants.
- Target Material: The source of the material to be deposited.
- Substrate: The surface onto which the thin film is deposited.
- Inert Gas (Argon): Provides the ions necessary for the sputtering process.
- Power Supply: Generates the electric field to ionize the gas and accelerate ions.
-
Process Optimization:
- Gas Pressure: Optimal gas pressure ensures efficient ionization and collision rates.
- Power Input: Higher power increases the energy of the ions, improving deposition rates but requiring careful control to avoid damaging the target or substrate.
- Substrate Temperature: Lower temperatures reduce residual stress, while higher temperatures can improve film adhesion and crystallinity.
-
Comparison with Other Thin Film Deposition Techniques:
- Sputtering is often compared to evaporation, another PVD technique. While evaporation is simpler and faster, sputtering offers better control over film composition and uniformity, especially for complex materials.
- Sputtering is also more suitable for depositing materials with high melting points, as it does not require heating the target to vaporization temperatures.
-
Challenges and Considerations:
- Target Erosion: Continuous bombardment can erode the target material, requiring periodic replacement.
- Contamination: Impurities in the gas or chamber can affect film quality, necessitating high-purity materials and cleanroom environments.
- Cost: Sputtering systems can be expensive due to the need for vacuum equipment and precise controls.
By understanding these key points, equipment and consumable purchasers can make informed decisions about sputtering systems, ensuring they select the right components and parameters for their specific applications.
Summary Table:
Aspect | Details |
---|---|
Mechanism | Plasma ionizes inert gas, dislodging target atoms to form a thin film. |
Key Advantages | Uniform deposition, low residual stress, precise control, and versatility. |
Applications | Semiconductors, optics, solar panels, decorative coatings. |
Key Components | Vacuum chamber, target material, substrate, inert gas, power supply. |
Optimization Factors | Gas pressure, power input, substrate temperature. |
Challenges | Target erosion, contamination, and high costs. |
Ready to integrate sputtering into your process? Contact our experts today for tailored solutions!