Thermal evaporation and sputtering are two widely used physical vapor deposition (PVD) techniques for creating thin films on substrates. Thermal evaporation involves heating a solid material in a high vacuum chamber until it evaporates, forming a vapor stream that deposits onto the substrate. This method is simple and effective for materials with low melting points, making it ideal for applications like OLEDs and thin-film transistors. Sputtering, on the other hand, involves bombarding a target material with high-energy particles to eject atoms or clusters, which then deposit onto the substrate. This technique is versatile and suitable for a wide range of materials, including metals, ceramics, and plastics. Both methods are essential in industries requiring precise and high-quality thin-film coatings.
Key Points Explained:
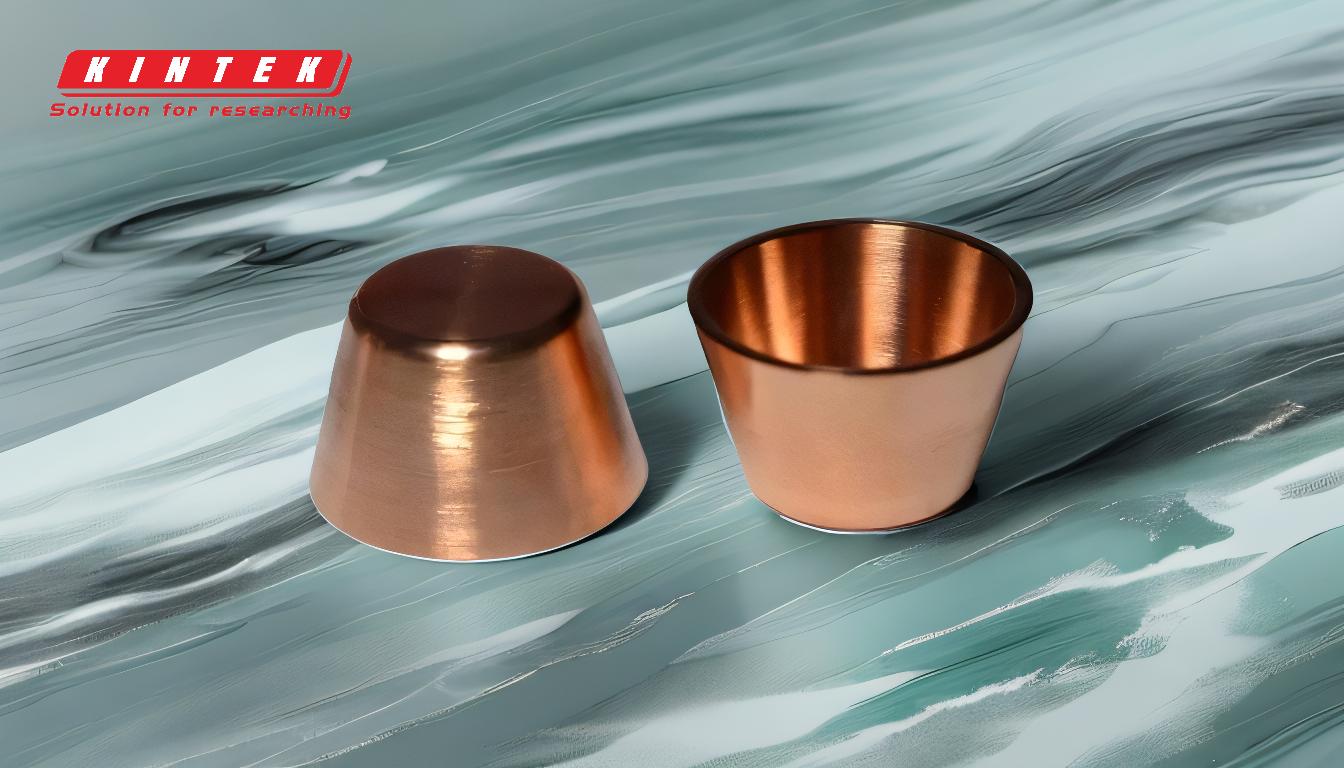
-
Thermal Evaporation Process:
- Thermal evaporation works by heating a solid material in a high vacuum chamber until it evaporates, creating a vapor stream.
- The vaporized material travels through the vacuum and deposits onto the substrate, forming a thin film.
- Heating can be achieved using an electric resistance heater or an electron beam evaporator, depending on the material's properties.
- This method is particularly effective for materials with low melting points and is commonly used in applications like OLEDs and thin-film transistors.
-
Advantages of Thermal Evaporation:
- High Deposition Rates: Thermal evaporation produces a robust vapor stream, enabling faster deposition compared to other methods.
- Simplicity: The process is straightforward, requiring only a vacuum chamber and a heating source.
- Material Compatibility: It is suitable for materials that can be easily vaporized without decomposition.
-
Sputtering Process:
- Sputtering involves bombarding a target material with high-energy particles (usually ions) to eject atoms or clusters.
- These ejected particles travel through the vacuum and deposit onto the substrate, forming a thin film.
- This method is versatile and can be used for a wide range of materials, including metals, ceramics, and plastics.
-
Advantages of Sputtering:
- Material Versatility: Sputtering can deposit a wide variety of materials, including those with high melting points.
- Uniform Coatings: The process allows for the deposition of highly uniform and dense films.
- Control and Precision: Sputtering provides excellent control over film thickness and composition, making it suitable for complex multilayer structures.
-
Comparison of Thermal Evaporation and Sputtering:
- Deposition Mechanism: Thermal evaporation relies on thermal energy to vaporize the material, while sputtering uses kinetic energy from high-energy particles.
- Material Compatibility: Thermal evaporation is better suited for materials with low melting points, whereas sputtering can handle a broader range of materials.
- Deposition Rate: Thermal evaporation generally offers higher deposition rates, making it faster for certain applications.
- Film Quality: Sputtering typically produces films with better adhesion and uniformity, especially for complex or multilayer structures.
-
Applications:
- Thermal Evaporation: Commonly used in the production of OLEDs, thin-film transistors, and other electronic devices.
- Sputtering: Widely used in the semiconductor industry, optical coatings, and decorative finishes due to its versatility and precision.
In summary, both thermal evaporation and sputtering are essential techniques in thin-film deposition, each with its own advantages and ideal applications. Thermal evaporation is simpler and faster for certain materials, while sputtering offers greater versatility and control, making it suitable for a wider range of materials and complex film structures.
Summary Table:
Aspect | Thermal Evaporation | Sputtering |
---|---|---|
Deposition Mechanism | Thermal energy vaporizes material | High-energy particles eject material atoms |
Material Compatibility | Best for low melting point materials | Suitable for a wide range of materials |
Deposition Rate | Higher deposition rates | Slower compared to thermal evaporation |
Film Quality | Good for simple applications | Superior adhesion and uniformity |
Applications | OLEDs, thin-film transistors | Semiconductors, optical coatings |
Need help choosing the right PVD technique for your project? Contact our experts today!