Sputtering is a Physical Vapor Deposition (PVD) process used to deposit thin films of material onto a substrate. It involves the creation of a plasma in a vacuum chamber, where high-energy ions (typically argon) bombard a target material, causing atoms to be ejected from the target surface. These ejected atoms then travel through the plasma and deposit onto a substrate, forming a thin, uniform film. The process is widely used in industries such as semiconductors, optics, and coatings due to its ability to produce high-quality, dense films with excellent adhesion and reduced residual stress, even at relatively low deposition temperatures.
Key Points Explained:
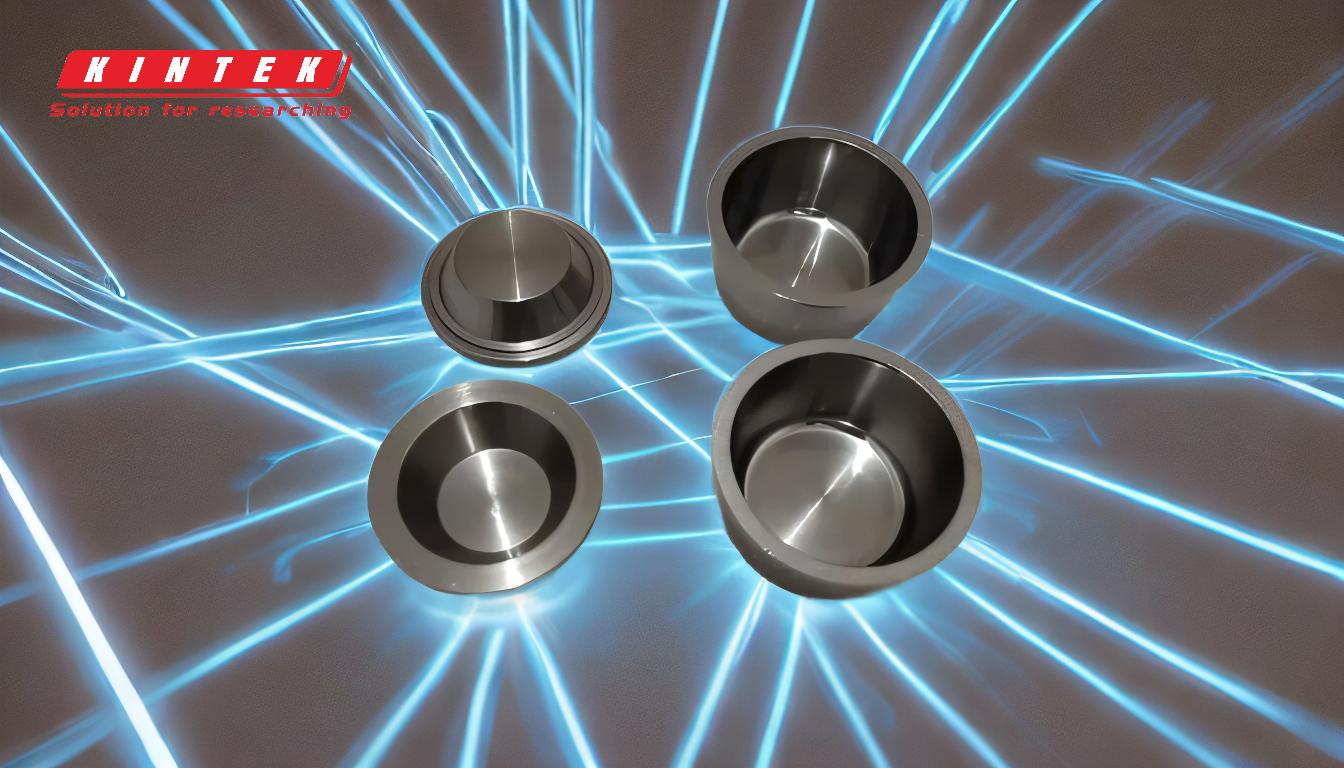
-
Definition and Mechanism of Sputtering:
- Sputtering is a PVD technique where atoms are ejected from a target material when it is bombarded by high-energy ions, usually from a plasma.
- The ejected atoms travel through the plasma and deposit onto a substrate, forming a thin film.
- This process is driven by the transfer of kinetic energy from the ions to the target material.
-
Key Components of the Sputtering Process:
- Vacuum Chamber: The process occurs in a vacuum chamber to eliminate contaminants and control the environment.
- Inert Gas (Argon): Argon is commonly used because it is chemically inert and easily ionized.
- Target Material: The material to be deposited, which acts as the cathode in the system.
- Substrate: The surface onto which the ejected atoms are deposited.
- Plasma Generation: A plasma is created by ionizing the argon gas using a high voltage or electromagnetic excitation.
-
Steps in the Sputtering Process:
- Creating a Vacuum: The chamber is evacuated to a low pressure (~1 Pa) to remove moisture and impurities.
- Introducing Inert Gas: Argon is pumped into the chamber to create a low-pressure atmosphere.
- Heating the Chamber: The chamber is heated to temperatures ranging from 150–750°C, depending on the material being deposited.
- Generating Plasma: A high voltage (3–5 kV) is applied to ionize the argon gas, creating a plasma.
- Bombarding the Target: Positively charged argon ions are accelerated toward the negatively charged target, ejecting atoms from its surface.
- Deposition on Substrate: The ejected atoms travel through the plasma and deposit onto the substrate, forming a thin film.
-
Role of Plasma and Magnetic Fields:
- Plasma is essential for ionizing the argon gas and creating the high-energy ions needed to sputter the target.
- Magnetic fields are often used to confine and focus the plasma, increasing the efficiency of the sputtering process. This is known as magnetron sputtering.
-
Advantages of Sputtering:
- High-Quality Films: Sputtering produces dense, uniform films with excellent adhesion and low residual stress.
- Low-Temperature Deposition: Films can be deposited at temperatures below 150°C, making it suitable for temperature-sensitive substrates.
- Versatility: A wide range of materials, including metals, alloys, and compounds, can be deposited using sputtering.
- Precision: The process allows for precise control over film thickness and composition.
-
Applications of Sputtering:
- Semiconductors: Used for depositing thin films in integrated circuits and microelectronics.
- Optics: Applied in the production of anti-reflective coatings, mirrors, and optical filters.
- Coatings: Used for wear-resistant, decorative, and functional coatings on tools, automotive parts, and consumer goods.
- Energy: Utilized in the fabrication of solar cells and battery components.
-
Challenges and Considerations:
- Contamination: Residual gases or impurities in the chamber can affect film quality.
- Target Utilization: Non-uniform erosion of the target material can reduce efficiency.
- Cost: The equipment and process can be expensive, particularly for large-scale or specialized applications.
-
Comparison to Other PVD Techniques:
- Sputtering is often compared to evaporation, another PVD method. While evaporation is simpler and faster, sputtering offers better film quality, especially for complex materials and multi-layer structures.
- Sputtering is also more suitable for depositing materials with high melting points, which are difficult to evaporate.
By understanding these key points, equipment and consumable purchasers can better evaluate the suitability of sputtering PVD for their specific applications, ensuring optimal performance and cost-effectiveness.
Summary Table:
Aspect | Details |
---|---|
Process | Physical Vapor Deposition (PVD) using plasma to eject target material atoms. |
Key Components | Vacuum chamber, argon gas, target material, substrate, plasma generation. |
Steps | Create vacuum, introduce argon, heat chamber, generate plasma, deposit film. |
Advantages | High-quality films, low-temperature deposition, versatility, precision. |
Applications | Semiconductors, optics, coatings, energy (solar cells, batteries). |
Challenges | Contamination, target utilization, cost. |
Discover how sputtering can enhance your thin film applications—contact our experts today!