Magnetron sputtering is a highly advantageous thin film deposition technique widely used across industries due to its versatility, precision, and efficiency. It allows for the deposition of high-purity, uniform, and dense films on various substrates, including heat-sensitive materials. The process does not require thermal evaporation, making it suitable for materials with high melting points. Key benefits include high deposition rates, excellent film adhesion, precise control over thickness and density, and the ability to coat large areas uniformly. Additionally, it is environmentally friendly, reproducible, and adaptable for both conductive and non-conductive materials, making it a preferred choice for applications in microelectronics, wear resistance, corrosion resistance, and functional coatings.
Key Points Explained:
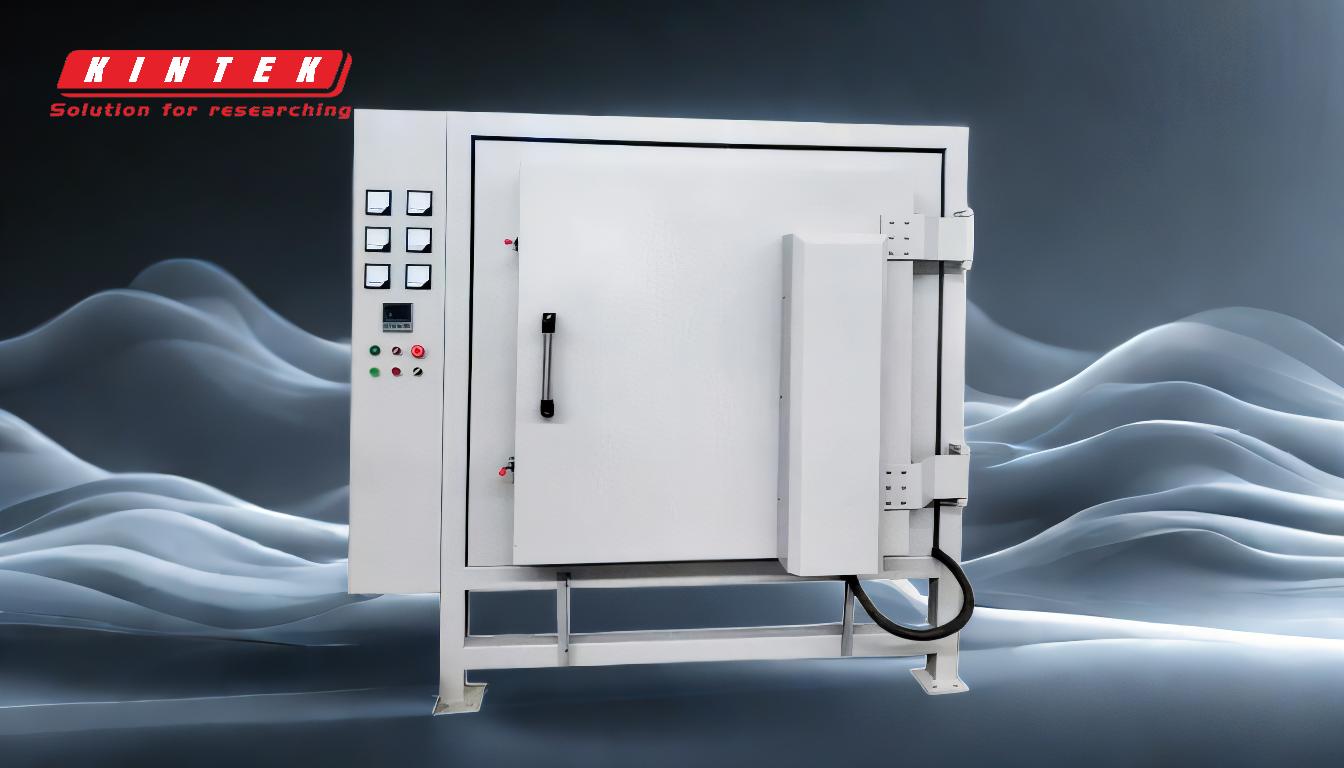
-
Versatility in Material Deposition
- Magnetron sputtering can deposit a wide range of materials, including metals, alloys, oxides, and compounds, regardless of their melting points.
- It is particularly useful for depositing dielectric and nitride films, which are critical in microelectronics and semiconductor applications.
- The process does not require thermal evaporation, heating, or melting of the target material, making it suitable for materials with high melting points or heat-sensitive substrates.
-
High-Quality Film Deposition
- The technique produces high-purity films with excellent uniformity and density, surpassing the quality achieved by evaporation methods.
- Films deposited via magnetron sputtering exhibit extremely high adhesion to substrates, ensuring durability and performance.
- It provides precise control over film thickness and density, making it ideal for applications requiring specific optical, electrical, or mechanical properties.
-
High Deposition Rates and Efficiency
- Magnetron sputtering offers high deposition rates, enabling the preparation of large quantities of films at a low cost.
- The process is efficient and reproducible, ensuring consistent results across multiple runs.
- It can be configured with multiple magnetron sources to enhance productivity and versatility.
-
Uniformity and Coverage
- The technique ensures excellent uniformity over large-area substrates, such as architectural glass, making it suitable for industrial-scale applications.
- It covers small features and complex geometries effectively, ensuring thorough material coverage.
-
Low-Temperature Process
- Magnetron sputtering operates at low temperatures, preventing damage to heat-sensitive substrates.
- This makes it ideal for applications involving polymers, plastics, or other temperature-sensitive materials.
-
Environmental and Economic Benefits
- The process is environmentally friendly, as it does not involve harmful chemicals or high-energy consumption.
- It allows for the deposition of small quantities of materials, reducing waste and cost.
- The ability to use various power systems, including RF magnetron sputtering, expands its applicability to non-conductive materials.
-
Applications Across Industries
- Magnetron sputtering is widely used in industries for wear resistance, corrosion resistance, and functional coatings.
- It is essential in microelectronics for depositing dielectric and nitride films.
- The technique is also used in optical coatings, decorative coatings, and barrier layers.
-
Ongoing Advancements
- Research and development continue to improve magnetron sputtering, enhancing its efficiency, precision, and applicability.
- Innovations in power systems and process configurations are expanding its use in emerging technologies.
In summary, magnetron sputtering stands out as a superior thin film deposition technique due to its versatility, precision, and ability to produce high-quality films efficiently and cost-effectively. Its adaptability to various materials and substrates, combined with its environmental and economic benefits, makes it a preferred choice for a wide range of industrial and technological applications.
Summary Table:
Key Advantage | Description |
---|---|
Versatility in Material Deposition | Deposits metals, alloys, oxides, and compounds, including heat-sensitive materials. |
High-Quality Film Deposition | Produces uniform, dense, and high-purity films with excellent adhesion. |
High Deposition Rates | Enables efficient, cost-effective production of large quantities of films. |
Uniformity and Coverage | Ensures excellent uniformity over large areas and complex geometries. |
Low-Temperature Process | Prevents damage to heat-sensitive substrates like polymers and plastics. |
Environmental and Economic Benefits | Eco-friendly, reduces waste, and is cost-effective for small-quantity deposition. |
Applications Across Industries | Used in microelectronics, wear resistance, corrosion resistance, and coatings. |
Ongoing Advancements | Continuous R&D improves efficiency, precision, and applicability. |
Unlock the potential of magnetron sputtering for your projects—contact our experts today!