Vacuum hardening, particularly when using a vacuum hardening furnace, offers numerous benefits that make it a preferred method for heat treatment in various industries. This process provides a clean and controlled environment, ensuring high-quality and ultra-clean components. It enhances the mechanical properties of materials, such as hardness, strength, and wear resistance, while maintaining dimensional stability. Vacuum hardening is also energy-efficient, environmentally friendly, and versatile, supporting a range of heat treatment processes. Additionally, it offers precise temperature control and uniform heating, which are critical for consistent and repeatable results.
Key Points Explained:
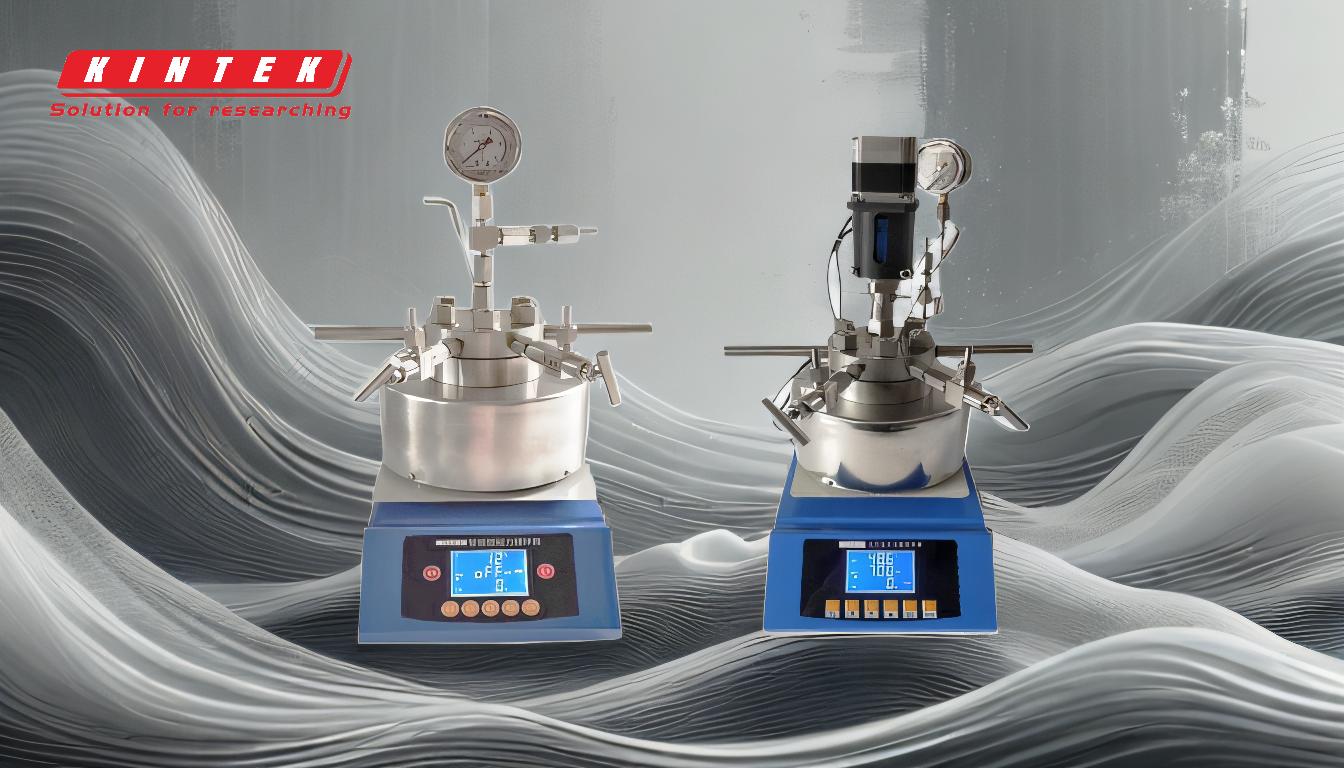
-
Clean and Controlled Environment:
- Vacuum hardening takes place in a vacuum furnace, which eliminates exposure to impurities and reactive gases. This ensures that the treated materials are free from contamination, resulting in high-quality and ultra-clean components. The absence of oxygen and other reactive gases prevents oxidation and decarburization, which are common issues in traditional heat treatment methods.
-
Enhanced Mechanical Properties:
- The process significantly improves the mechanical properties of metals, including hardness, strength, and wear resistance. These enhancements are achieved without compromising dimensional stability, making vacuum-hardened materials suitable for demanding applications. For example, vacuum hardening is particularly beneficial for components used in aerospace, automotive, and tooling industries, where high performance and durability are critical.
-
Precise Temperature Control:
- A vacuum hardening furnace provides excellent temperature uniformity and stability, ensuring consistent and repeatable results. This precision is crucial for achieving the desired metallurgical properties in the treated materials. The ability to control the temperature range between 1100-1500°C allows for tailored heat treatment processes that meet specific requirements.
-
Versatility in Heat Treatment:
- Vacuum hardening furnaces support a wide range of heat treatment processes, including annealing, brazing, sintering, tempering, and hardening. This versatility makes them suitable for various applications and materials, from steel and titanium to nickel-based superalloys. The ability to perform multiple processes in a single furnace enhances operational efficiency and reduces the need for additional equipment.
-
Energy Efficiency:
- Vacuum furnaces are designed with advanced insulation materials and control systems that minimize heat loss and optimize energy consumption. This energy efficiency not only reduces operational costs but also aligns with the growing demand for sustainable and environmentally friendly manufacturing practices.
-
Environmental Friendliness:
- Unlike traditional heat treatment methods, vacuum hardening does not use flammable gases or produce harmful by-products. This makes it a safer and more environmentally friendly option. The process does not result in pollution, making it compliant with stringent environmental regulations and contributing to a safer work environment.
-
Improved Chemical Properties:
- Vacuum hardening enhances the chemical properties of metals, such as resistance to corrosion and shear strength. These improvements expand the potential applications of the treated materials, making them suitable for more demanding uses. For instance, vacuum-hardened components are often used in environments where corrosion resistance is critical, such as in marine and chemical processing industries.
-
Rapid Cooling and Computer-Controlled Processes:
- The ability to rapidly cool (quench) materials in a vacuum furnace ensures that the desired metallurgical properties are achieved. Additionally, computer-controlled processes enhance repeatability and consistency, which are essential for high-volume production and quality assurance.
In summary, vacuum hardening using a vacuum hardening furnace offers a comprehensive range of benefits, from improved material properties and precise temperature control to environmental friendliness and energy efficiency. These advantages make it an ideal choice for industries that require high-performance materials and sustainable manufacturing practices.
Summary Table:
Benefit | Description |
---|---|
Clean & Controlled Environment | Eliminates impurities, prevents oxidation, and ensures ultra-clean components. |
Enhanced Mechanical Properties | Improves hardness, strength, and wear resistance without dimensional instability. |
Precise Temperature Control | Ensures uniform heating and consistent results with a range of 1100-1500°C. |
Versatility in Heat Treatment | Supports annealing, brazing, sintering, tempering, and hardening processes. |
Energy Efficiency | Reduces operational costs with advanced insulation and control systems. |
Environmental Friendliness | No harmful by-products, compliant with environmental regulations. |
Improved Chemical Properties | Enhances corrosion resistance and shear strength for demanding applications. |
Rapid Cooling & Automation | Ensures rapid quenching and repeatable, computer-controlled processes. |
Unlock the full potential of vacuum hardening for your industry—contact us today for expert guidance!