The best coating for metal tools depends on the specific application, environmental conditions, and performance requirements. Key factors include the type of coating process (e.g., CVD or PVD), the substrate material, and the tool's exposure to wear, corrosion, and abrasion. Tungsten carbide coatings are ideal for extreme wear conditions, while other coatings may be better suited for corrosion resistance or specific operational environments. Consulting a technical team is essential to ensure the chosen coating meets durability and performance standards.
Key Points Explained:
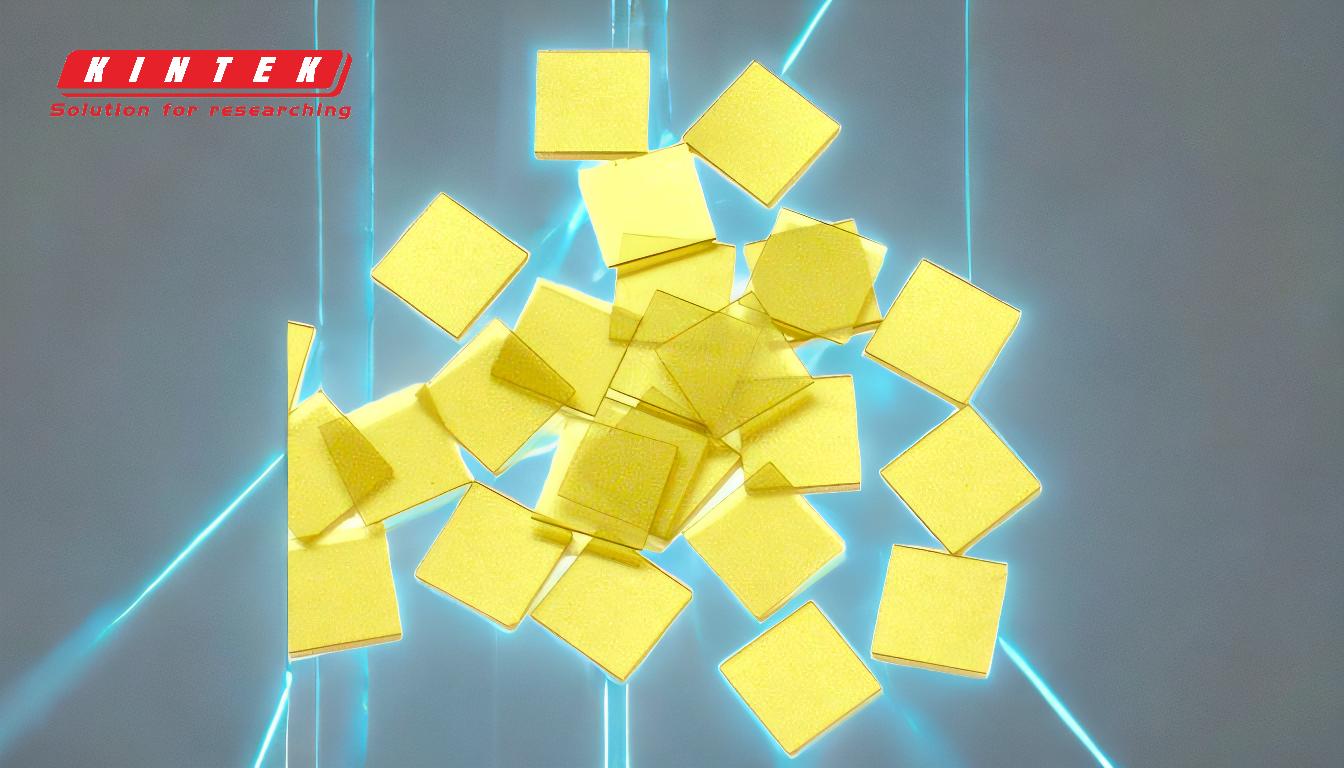
-
Coating Processes: CVD vs. PVD
-
Chemical Vapor Deposition (CVD):
- Involves a chemical reaction to deposit a coating on the tool surface.
- Produces thick, durable coatings with excellent adhesion.
- Suitable for high-temperature applications and tools exposed to extreme wear.
- Common coatings include titanium nitride (TiN) and tungsten carbide.
-
Physical Vapor Deposition (PVD):
- Uses physical methods like sputtering or evaporation to deposit coatings.
- Creates thinner, smoother coatings with high hardness and wear resistance.
- Ideal for precision tools and applications requiring fine surface finishes.
- Examples include titanium aluminum nitride (TiAlN) and diamond-like carbon (DLC).
-
Chemical Vapor Deposition (CVD):
-
Application-Specific Considerations
-
Wear Resistance:
- Tungsten carbide coatings are highly effective for tools exposed to extreme wear and abrasion.
- These coatings are often used in cutting tools, drill bits, and mining equipment.
-
Corrosion Resistance:
- Coatings like chromium nitride (CrN) or DLC are ideal for tools used in corrosive environments, such as marine or chemical processing applications.
-
Temperature Resistance:
- CVD coatings, such as TiN or aluminum oxide (Al₂O₃), perform well in high-temperature environments, making them suitable for machining or metal-forming tools.
-
Wear Resistance:
-
Substrate Compatibility
- The substrate material (e.g., steel, titanium, or carbide) plays a critical role in determining the best coating.
- For example, PVD coatings are often preferred for high-speed steel (HSS) tools due to their ability to maintain sharp edges and reduce friction.
- CVD coatings are better suited for carbide substrates, as they can withstand higher temperatures and provide superior wear resistance.
-
Environmental and Operational Factors
-
Abrasion and Erosion:
- Tools exposed to abrasive materials or high-impact conditions benefit from hard coatings like tungsten carbide or ceramic-based coatings.
-
Chemical Exposure:
- In environments with exposure to acids, alkalis, or solvents, corrosion-resistant coatings like CrN or DLC are recommended.
-
Friction and Lubrication:
- Coatings with low friction coefficients, such as DLC or molybdenum disulfide (MoS₂), are ideal for tools requiring smooth operation or reduced wear.
-
Abrasion and Erosion:
-
Consulting Technical Experts
- Choosing the best coating involves balancing multiple factors, including cost, performance, and application requirements.
- Technical teams can provide tailored recommendations based on tool design, operational conditions, and desired outcomes.
- Testing and prototyping may be necessary to validate the coating's performance under real-world conditions.
-
Examples of Common Coatings
-
Titanium Nitride (TiN):
- Offers excellent wear resistance and a gold-colored finish.
- Commonly used for cutting tools and drills.
-
Titanium Aluminum Nitride (TiAlN):
- Provides high-temperature stability and oxidation resistance.
- Ideal for high-speed machining applications.
-
Diamond-Like Carbon (DLC):
- Combines low friction with high hardness and corrosion resistance.
- Suitable for precision tools and components in harsh environments.
-
Chromium Nitride (CrN):
- Known for its corrosion resistance and durability.
- Often used in marine and chemical processing tools.
-
Titanium Nitride (TiN):
In conclusion, the best coating for metal tools depends on the specific application, substrate, and environmental conditions. Understanding the strengths and limitations of different coating processes and materials is essential for achieving optimal performance and durability. Consulting with technical experts ensures that the chosen coating meets the tool's requirements and extends its service life.
Summary Table:
Factor | Key Considerations |
---|---|
Coating Process | - CVD: Thick, durable, high-temperature resistant. PVD: Thin, smooth, precision-ready. |
Application Needs | - Wear resistance: Tungsten carbide. Corrosion resistance: CrN or DLC. |
Substrate Material | - Steel: PVD preferred. Carbide: CVD recommended. |
Environmental Factors | - Abrasion: Hard coatings. Chemical exposure: Corrosion-resistant coatings. |
Common Coatings | - TiN, TiAlN, DLC, CrN. |
Need help choosing the right coating for your metal tools? Contact our experts today for tailored solutions!