The best material for induction heating depends on several factors, including the application's requirements, the material's electrical conductivity, resistivity, and thermal properties. Induction heating is most effective with electrically conductive materials, typically metals, due to their ability to generate heat through eddy currents and hysteresis losses. The efficiency of heating is influenced by the material's resistivity, size, shape, and the frequency of the alternating current. For non-conductive materials like plastics, indirect heating using a conductive metal inductor is necessary. The choice of material also depends on the desired temperature variation, heating depth, and the design of the induction heating system.
Key Points Explained:
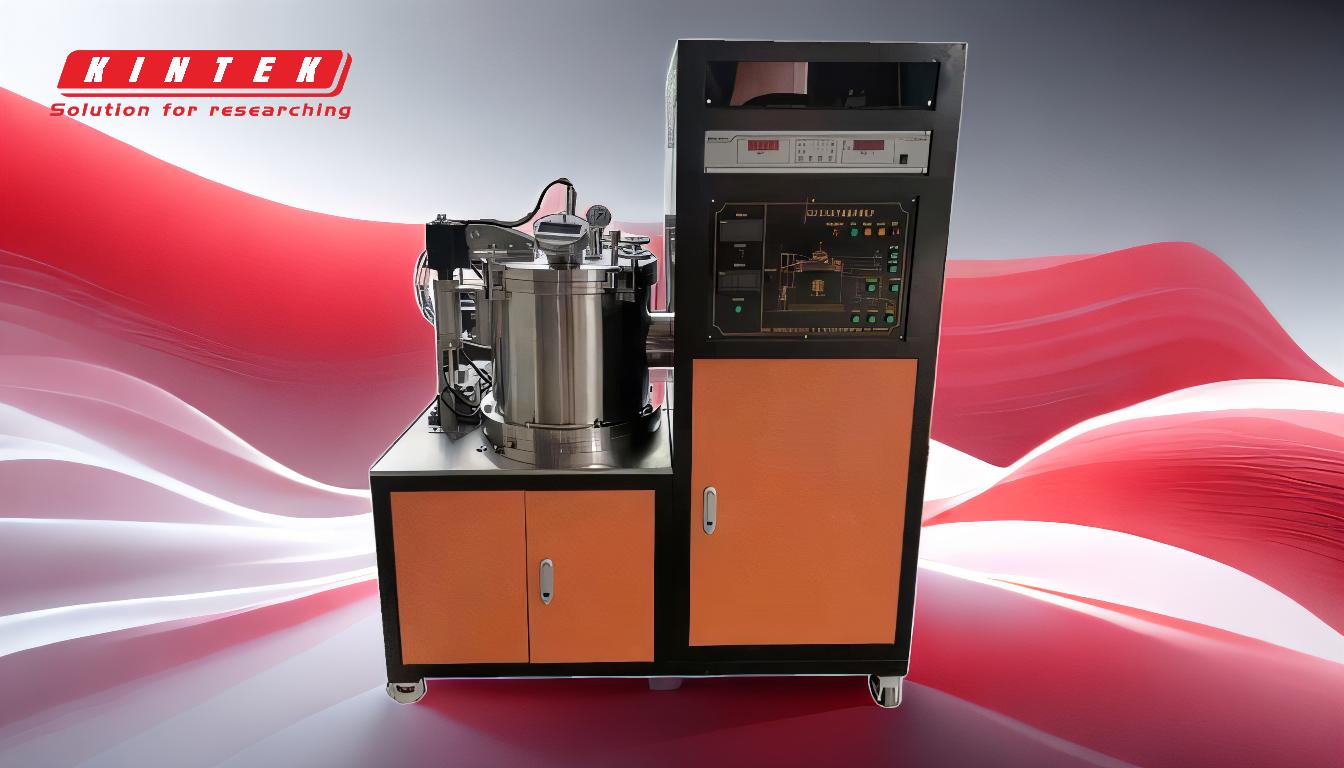
-
Conductive Materials for Direct Induction Heating:
- Induction heating works best with electrically conductive materials, primarily metals. These materials generate heat through eddy currents and hysteresis losses when exposed to an alternating magnetic field.
- Examples of commonly used conductive materials include steel, copper, aluminum, and brass. Each material has different resistivity and thermal properties, affecting the heating efficiency and depth.
-
Non-Conductive Materials and Indirect Heating:
- Non-conductive materials like plastics cannot be heated directly through induction. Instead, a conductive metal inductor is heated first, and the heat is then transferred to the non-conductive material.
- This method is less efficient but allows for the heating of materials that would otherwise be unsuitable for induction heating.
-
Material Resistivity and Heating Efficiency:
- The resistivity of a material plays a crucial role in induction heating. Materials with higher resistivity heat up faster because they generate more heat when subjected to eddy currents.
- For example, steel, with its relatively high resistivity, heats up more quickly than copper, which has lower resistivity. However, copper is still used in applications where high thermal conductivity is required.
-
Size and Thickness of the Material:
- Smaller and thinner materials heat up faster because the eddy currents are concentrated in a smaller volume, leading to more efficient heating.
- Larger or thicker materials may require higher power or longer heating times to achieve the desired temperature.
-
Frequency of Alternating Current:
- The frequency of the alternating current used in induction heating affects the depth of heating. Higher frequencies result in shallower heating depths, which is ideal for surface heating applications.
- Lower frequencies are used for deeper penetration, which is necessary for heating thicker materials.
-
Inductor Design and Power Supply Capacity:
- The design of the inductor coil must match the material's properties and the desired heating pattern. The coil's shape, size, and number of turns affect the distribution and intensity of the magnetic field.
- The power supply must be capable of delivering the required energy to achieve the desired temperature rise, considering factors like the material's specific heat, mass, and heat loss mechanisms (conduction, convection, and radiation).
-
Application-Specific Considerations:
- The choice of material for induction heating depends on the specific application. For example, in metalworking, materials like steel and aluminum are commonly used due to their high melting points and mechanical properties.
- In the food industry, materials like stainless steel are preferred for their corrosion resistance and ease of cleaning.
-
Refractory Materials and High-Temperature Applications:
- In high-temperature applications, such as metal melting, refractory materials are used to line the induction furnace. These materials must withstand extreme temperatures and chemical reactions with molten metals.
- The selection of refractory materials depends on factors like operating temperature, slag formation, and the type of metal being melted.
In summary, the best material for induction heating depends on the specific application, the material's electrical and thermal properties, and the design of the induction heating system. Electrically conductive metals are typically the most effective for direct heating, while non-conductive materials require indirect methods. The choice of material should align with the desired heating efficiency, depth, and application requirements.
Summary Table:
Factor | Description |
---|---|
Conductive Materials | Metals like steel, copper, aluminum, and brass; ideal for direct heating. |
Non-Conductive Materials | Plastics require indirect heating via a conductive metal inductor. |
Resistivity | Higher resistivity materials (e.g., steel) heat faster due to eddy currents. |
Size & Thickness | Smaller, thinner materials heat faster due to concentrated eddy currents. |
Frequency of AC | Higher frequencies for surface heating; lower frequencies for deeper heating. |
Application | Steel and aluminum for metalworking; stainless steel for food industry. |
Refractory Materials | Used in high-temperature applications like metal melting. |
Need help selecting the best material for your induction heating application? Contact our experts today!