A catalyst is essential in the production of graphene, particularly in chemical vapor deposition (CVD) processes, as it significantly reduces the required temperature for the reaction to occur. Without a catalyst, the formation of graphene from disassociated carbon atoms would require extremely high temperatures (over 2500°C). Catalysts such as iron nanoparticles, nickel foam, and gallium vapor are commonly used to lower the energy barrier for both precursor pyrolysis and graphitic structure formation. This not only reduces the need for extreme heat but also improves control over the quality of the graphene film. Some catalysts can be used in situ during graphene buildup, while others require an additional step for removal from the sample material.
Key Points Explained:
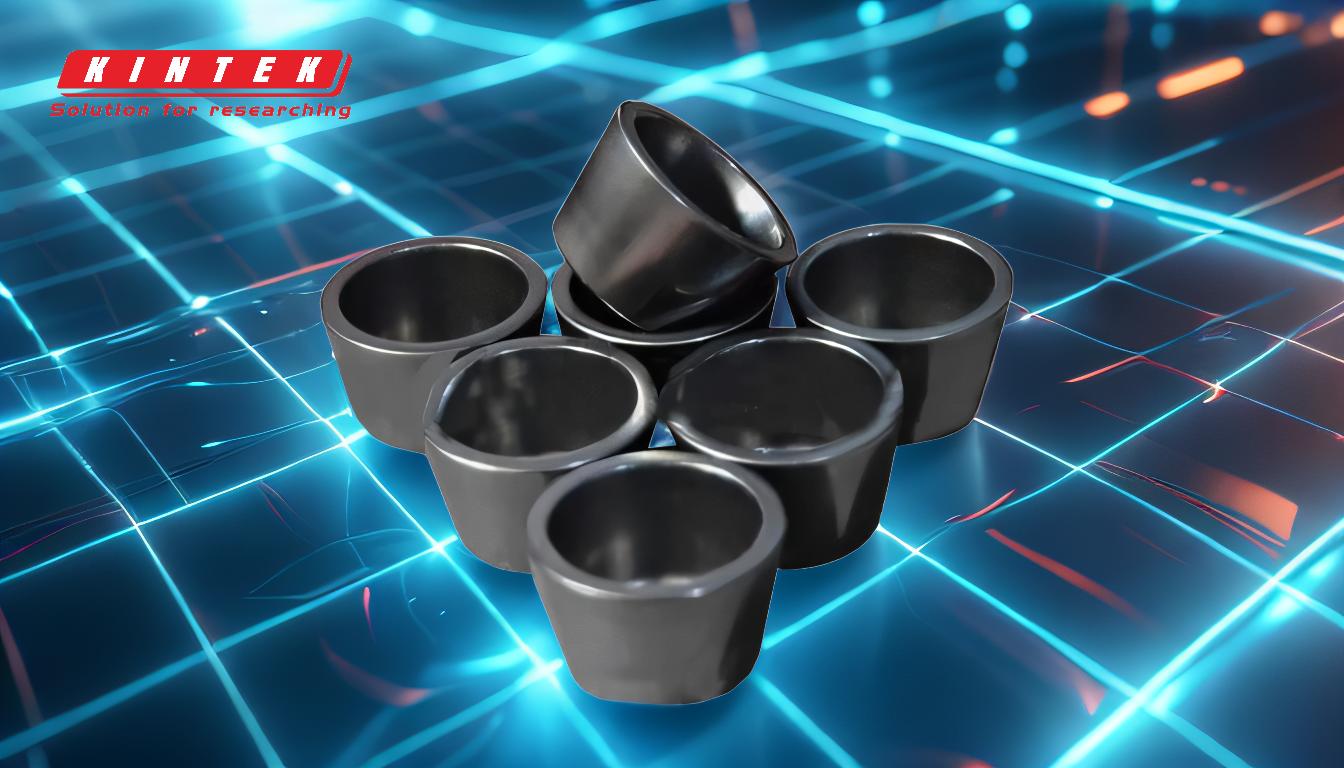
-
Role of Catalysts in Graphene Production
- Catalysts are crucial in the CVD process for graphene production.
- They lower the energy barrier required for the formation of graphene, reducing the need for extremely high temperatures (over 2500°C without a catalyst).
- This makes the process more energy-efficient and controllable, improving the quality of the graphene film.
-
Common Catalysts Used in Graphene Production
- Iron Nanoparticles: These are widely used due to their effectiveness in lowering the reaction temperature and promoting the growth of high-quality graphene.
- Nickel Foam: Nickel is another popular catalyst, known for its ability to facilitate the formation of graphene layers at lower temperatures.
- Gallium Vapor: Gallium is used in specific applications where its unique properties are advantageous, though it may require additional steps for removal after the reaction.
-
Mechanism of Catalyst Action
- Catalysts, typically elemental metals, lower the energy barrier for precursor pyrolysis (breaking down carbon-containing gases into carbon atoms) and graphitic structure formation.
- This dual action reduces the sensitivity of reaction rates to temperature variations, allowing for better control over the graphene production process.
-
Placement and Removal of Catalysts
- Catalysts can be used in situ (directly in the reaction zone) during graphene buildup, or they can be placed at a distance from the deposition area.
- Some catalysts, like nickel and iron, may require an additional step to remove them from the final graphene sample, ensuring the purity and quality of the graphene.
-
Impact on Graphene Quality
- The use of catalysts not only reduces the required temperature but also enhances the uniformity and structural integrity of the graphene film.
- By lowering the energy barrier, catalysts allow for more precise control over the reaction, leading to fewer defects and higher-quality graphene.
-
Energy Efficiency and Scalability
- The reduction in required temperature due to catalysts makes the graphene production process more energy-efficient, which is critical for large-scale industrial applications.
- This energy efficiency also contributes to the scalability of graphene production, making it more feasible for commercial use.
In summary, catalysts play a pivotal role in the production of graphene by lowering the energy requirements and improving the quality and scalability of the process. Common catalysts like iron nanoparticles, nickel foam, and gallium vapor are essential tools in the CVD method, enabling the efficient and controlled synthesis of high-quality graphene.
Summary Table:
Aspect | Details |
---|---|
Role of Catalysts | Lower energy barriers, reduce required temperatures, improve graphene quality. |
Common Catalysts | Iron nanoparticles, nickel foam, gallium vapor. |
Mechanism of Action | Lower energy for precursor pyrolysis and graphitic structure formation. |
Placement & Removal | In situ or at a distance; some require removal for sample purity. |
Impact on Quality | Enhances uniformity, structural integrity, and defect reduction. |
Energy Efficiency | Reduces energy consumption, making production scalable and cost-effective. |
Learn how catalysts can optimize your graphene production—contact our experts today!