Titanium PVD (Physical Vapor Deposition) coatings are known for their durability, versatility, and aesthetic appeal. The color of titanium PVD coatings can vary widely depending on the specific process and materials used. Common colors include gold, champagne, copper, black, and chocolate bronze, among others. These coatings are highly durable, resistant to corrosion and abrasion, and can be applied to a variety of substrates, making them suitable for numerous applications, including medical devices, optical lenses, and even culinary tools. The color and finish of the PVD coating are influenced by the surface preparation and the specific PVD process used.
Key Points Explained:
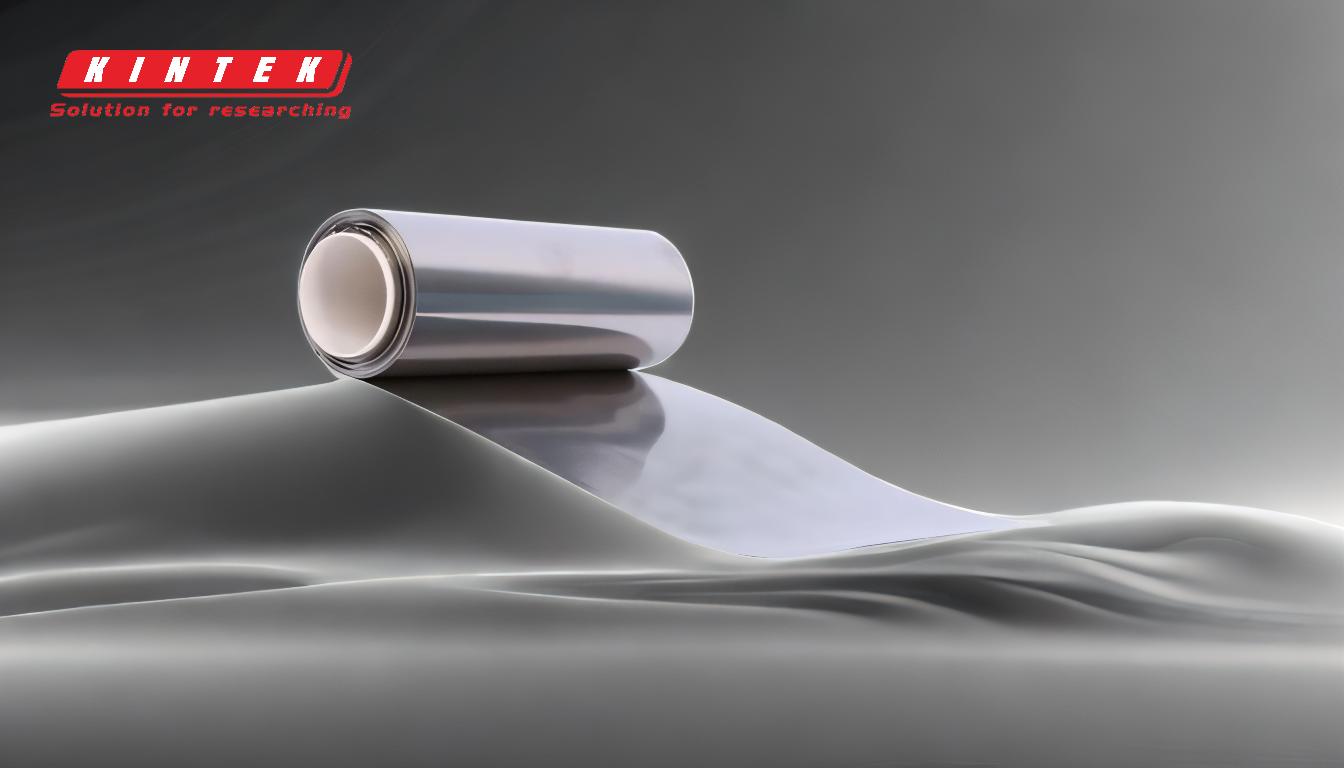
-
Versatility of PVD Coatings:
- PVD coatings are highly versatile and can be applied to a wide range of substrates, including metals, ceramics, and polymers.
- They are suitable for almost any inorganic coating material, making them ideal for various applications, from microchips to medical devices.
-
Color Options in Titanium PVD:
- Titanium PVD coatings come in a variety of colors, including gold, champagne, copper, black, and chocolate bronze.
- The color is determined by the specific materials and processes used during the PVD coating process.
-
Surface Finish and Preparation:
- The finish of the PVD coating closely follows the topology of the surface. A polished surface will result in a polished finish, while a brushed or satin surface will produce a matte or satin finish.
- Pretreatment with a polymer powder coating can provide a smooth, glossy surface, which can enhance the final appearance of the PVD coating.
-
Durability and Performance:
- PVD coatings are known for their durability, with excellent resistance to abrasion, corrosion, and temperature fluctuations.
- They are extremely thin, pure, and clean, offering high performance in demanding applications.
-
Applications of Titanium PVD Coatings:
- Titanium PVD coatings are used in a wide range of industries, including electronics (microchips, semiconductor devices), optics (lenses), renewable energy (solar panels), and medical devices.
- They are also used in culinary tools due to their non-toxic nature and resistance to acid degradation, ensuring they do not affect the taste of food.
-
Control Over Coating Attributes:
- The PVD process allows for precise control over the density, structure, and stoichiometry of the coatings, enabling the development of specific attributes such as adhesion, lubricity, and hardness.
- This level of control is crucial for applications where performance and durability are paramount.
In summary, the color of titanium PVD coatings can vary widely, with common options including gold, champagne, copper, black, and chocolate bronze. These coatings are highly durable and versatile, suitable for a range of applications from medical devices to culinary tools. The finish and color are influenced by the surface preparation and the specific PVD process used, ensuring a high-quality, durable coating that meets the needs of various industries.
Summary Table:
Aspect | Details |
---|---|
Color Options | Gold, champagne, copper, black, chocolate bronze |
Surface Finish | Polished, matte, or satin, depending on surface preparation |
Durability | Resistant to abrasion, corrosion, and temperature fluctuations |
Applications | Medical devices, optical lenses, culinary tools, electronics, solar panels |
Key Benefits | High durability, versatility, and precise control over coating attributes |
Learn more about titanium PVD coatings and their applications—contact us today!