Hydraulic pumps are critical components in many industrial and mobile hydraulic systems, and they can experience a variety of common problems that affect their performance and longevity. These issues often stem from factors such as contamination, improper maintenance, or operational errors. Addressing these problems promptly is essential to ensure the reliability and efficiency of the hydraulic system. Below, we explore the key issues that hydraulic pumps commonly face and provide detailed explanations for each.
Key Points Explained:
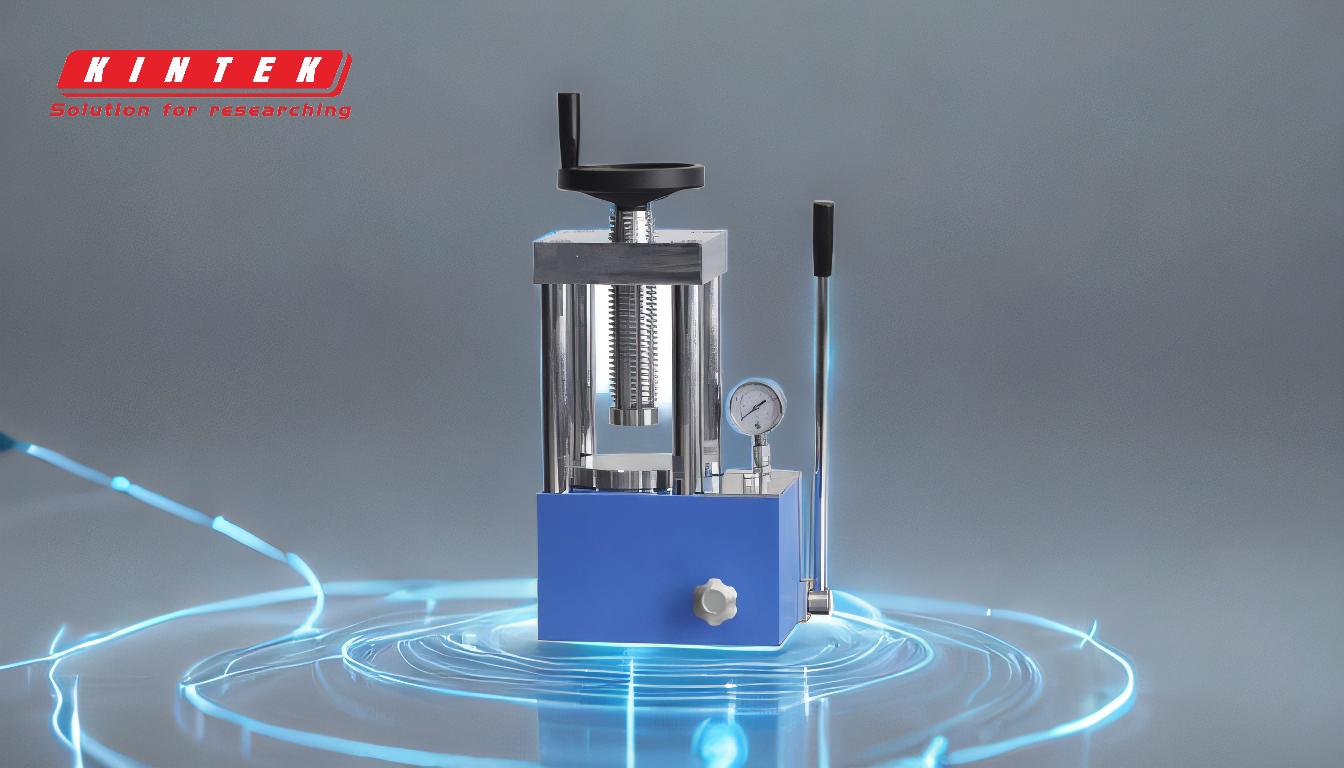
-
Contamination of Hydraulic Fluid
- Cause: Dirt, debris, or water entering the hydraulic system can contaminate the fluid, leading to wear and tear on the pump components.
- Effect: Contamination can cause abrasion, corrosion, and clogging of internal parts, reducing the pump's efficiency and lifespan.
- Solution: Regularly inspect and replace hydraulic filters, use clean fluid, and ensure proper sealing of the system to prevent contaminants from entering.
-
Cavitation
- Cause: Cavitation occurs when the hydraulic fluid cannot fill the pump's inlet fast enough, creating vapor bubbles that collapse violently.
- Effect: This can lead to pitting and erosion of the pump's internal surfaces, resulting in noise, vibration, and reduced performance.
- Solution: Ensure the pump is properly sized, maintain adequate fluid levels, and check for restrictions in the inlet line.
-
Overheating
- Cause: Excessive heat can be generated due to high system pressure, poor fluid quality, or inadequate cooling.
- Effect: Overheating can degrade the hydraulic fluid, damage seals, and cause the pump to fail prematurely.
- Solution: Monitor system temperature, use high-quality fluid with the correct viscosity, and ensure proper cooling mechanisms are in place.
-
Aeration
- Cause: Air entering the hydraulic system can cause aeration, often due to leaks in the suction line or low fluid levels.
- Effect: Aeration leads to noisy operation, reduced efficiency, and potential damage to pump components due to the compressibility of air.
- Solution: Check for and repair any leaks, maintain proper fluid levels, and ensure the system is properly bled of air.
-
Wear and Tear
- Cause: Normal operational use over time can lead to wear of pump components such as seals, bearings, and vanes.
- Effect: Wear can result in decreased performance, leaks, and eventual pump failure.
- Solution: Implement a regular maintenance schedule, replace worn parts promptly, and use high-quality components.
-
Improper Fluid Viscosity
- Cause: Using hydraulic fluid with incorrect viscosity for the operating conditions can lead to inefficiencies and damage.
- Effect: Fluid that is too thick can cause excessive resistance, while fluid that is too thin may not provide adequate lubrication.
- Solution: Select hydraulic fluid with the appropriate viscosity for the operating temperature and conditions.
-
Misalignment
- Cause: Improper installation or shifting of the pump can lead to misalignment with the drive shaft.
- Effect: Misalignment can cause excessive vibration, noise, and wear on the pump and connected components.
- Solution: Ensure proper alignment during installation and regularly check and adjust as necessary.
-
Pressure Surges
- Cause: Rapid changes in system pressure can occur due to sudden valve closures or load changes.
- Effect: Pressure surges can cause shock loads on the pump, leading to damage and reduced lifespan.
- Solution: Use pressure relief valves, accumulators, or other devices to mitigate pressure surges.
By understanding and addressing these common problems, operators can significantly enhance the performance and longevity of hydraulic pumps, ensuring reliable operation and minimizing downtime. Regular maintenance, proper installation, and the use of high-quality components are key to preventing these issues and maintaining an efficient hydraulic system.
Summary Table:
Problem | Cause | Effect | Solution |
---|---|---|---|
Contamination | Dirt, debris, or water entering the system | Abrasion, corrosion, clogging, reduced efficiency | Inspect/replace filters, use clean fluid, ensure proper sealing |
Cavitation | Inadequate fluid filling pump inlet, creating vapor bubbles | Pitting, erosion, noise, vibration, reduced performance | Properly size pump, maintain fluid levels, check inlet line restrictions |
Overheating | High system pressure, poor fluid quality, inadequate cooling | Fluid degradation, seal damage, premature pump failure | Monitor temperature, use correct viscosity fluid, ensure proper cooling |
Aeration | Air entering the system due to leaks or low fluid levels | Noisy operation, reduced efficiency, potential component damage | Check for leaks, maintain fluid levels, bleed air from system |
Wear and Tear | Normal operational use over time | Decreased performance, leaks, pump failure | Regular maintenance, replace worn parts, use high-quality components |
Improper Fluid Viscosity | Incorrect fluid viscosity for operating conditions | Excessive resistance or inadequate lubrication | Select fluid with appropriate viscosity for temperature and conditions |
Misalignment | Improper installation or shifting of pump | Vibration, noise, wear on pump and components | Ensure proper alignment during installation, regularly check and adjust |
Pressure Surges | Sudden valve closures or load changes | Shock loads, damage, reduced lifespan | Use pressure relief valves, accumulators, or other surge mitigation devices |
Need help resolving hydraulic pump issues? Contact our experts today for tailored solutions and support!