A muffle furnace is a specialized heating device designed for high-temperature applications, such as annealing, sintering, and heat treatment, while ensuring the sample is isolated from combustion byproducts and contaminants. Its construction includes a refractory-lined chamber (muffle) that houses heating elements, insulation to prevent heat loss, and components like thermocouples, temperature controllers, and safety switches for precise operation. The furnace works by heating the air inside the chamber through thermal convection and radiation, ensuring uniform temperature distribution and efficient heat transfer. This design allows for rapid heating, recovery, and cooling, making it ideal for laboratory and industrial use.
Key Points Explained:
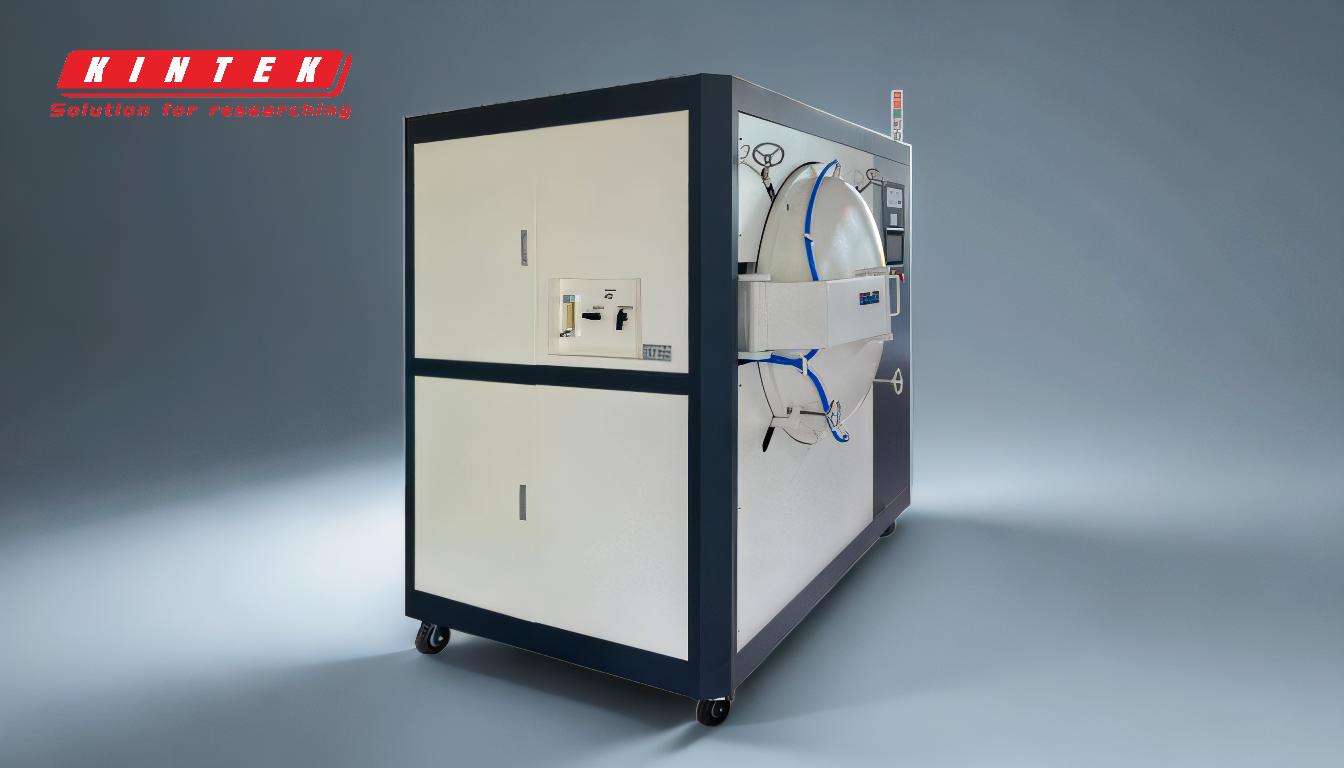
-
Construction of a Muffle Furnace:
- Muffle Chamber: The core component is the muffle, a refractory-lined chamber made of ceramic or other heat-resistant materials. It acts as an insulated enclosure to isolate the sample from direct contact with heating elements and contaminants.
- Heating Elements: These are typically made of high-resistance materials like nichrome or silicon carbide and are positioned around the muffle to provide uniform heating.
- Insulation: Multiple layers of insulating materials surround the muffle to minimize heat loss and maintain high temperatures efficiently.
- Temperature Control System: Includes a thermocouple for temperature measurement, a temperature controller for setting and regulating the desired temperature, and a timer for scheduling operations.
- Safety Features: Equipped with safety switches to cut power in case of overheating or other malfunctions, ensuring user safety.
-
Working Principle:
- The muffle furnace operates on the principles of thermal convection and radiation. Heating elements generate heat, which is transferred to the air inside the muffle chamber. The insulated design ensures that heat is retained within the chamber, allowing for rapid and uniform heating of the sample.
- The temperature control system monitors and adjusts the heat output to maintain the desired temperature, while the thermocouple provides real-time feedback to the controller.
-
Key Components and Their Functions:
- Heating Elements: Generate heat and are strategically placed to ensure uniform temperature distribution.
- Muffle: Acts as a barrier between the sample and heating elements, preventing contamination and ensuring even heating.
- Thermocouple: Measures the internal temperature and sends signals to the temperature controller.
- Temperature Controller: Regulates the heat output to maintain the set temperature.
- Insulation: Reduces heat loss and improves energy efficiency.
- Outer Casing: Provides structural integrity and protects internal components.
- Exhaust System (if present): Vents out any gases or fumes generated during heating.
-
Advantages of Muffle Furnaces:
- Isolation of Samples: The muffle design ensures that samples are not exposed to combustion byproducts or contaminants.
- Uniform Heating: The insulated chamber and strategically placed heating elements provide consistent temperature distribution.
- High-Temperature Capability: Capable of reaching and maintaining very high temperatures, making it suitable for a wide range of applications.
- Safety and Control: Advanced temperature control systems and safety features ensure safe and precise operation.
-
Applications:
- Laboratory Use: Commonly used for ashing, annealing, and heat treatment in research and testing labs.
- Industrial Use: Employed in processes like sintering, brazing, and material testing in industries such as ceramics, metallurgy, and electronics.
By understanding the construction and working principles of a muffle furnace, users can better appreciate its design, functionality, and suitability for various high-temperature applications.
Summary Table:
Component | Function |
---|---|
Muffle Chamber | Insulated enclosure isolating samples from contaminants and heating elements. |
Heating Elements | Generate heat for uniform temperature distribution. |
Insulation | Minimizes heat loss and maintains high temperatures efficiently. |
Temperature Control | Includes thermocouple, controller, and timer for precise operation. |
Safety Features | Cuts power in case of overheating or malfunctions for user safety. |
Outer Casing | Provides structural integrity and protects internal components. |
Exhaust System | Vents out gases or fumes generated during heating (if present). |
Discover how a muffle furnace can elevate your lab or industrial processes—contact us today for expert guidance!