Ball milling is a widely used technique in materials science and engineering for grinding, mixing, and homogenizing materials. However, contamination during ball milling is a significant concern, as it can compromise the quality and properties of the final product. Contamination can arise from various sources, including the milling media, the container, the atmosphere, and the materials being processed. Understanding these sources and their mechanisms is crucial for minimizing contamination and ensuring the integrity of the milled materials.
Key Points Explained:
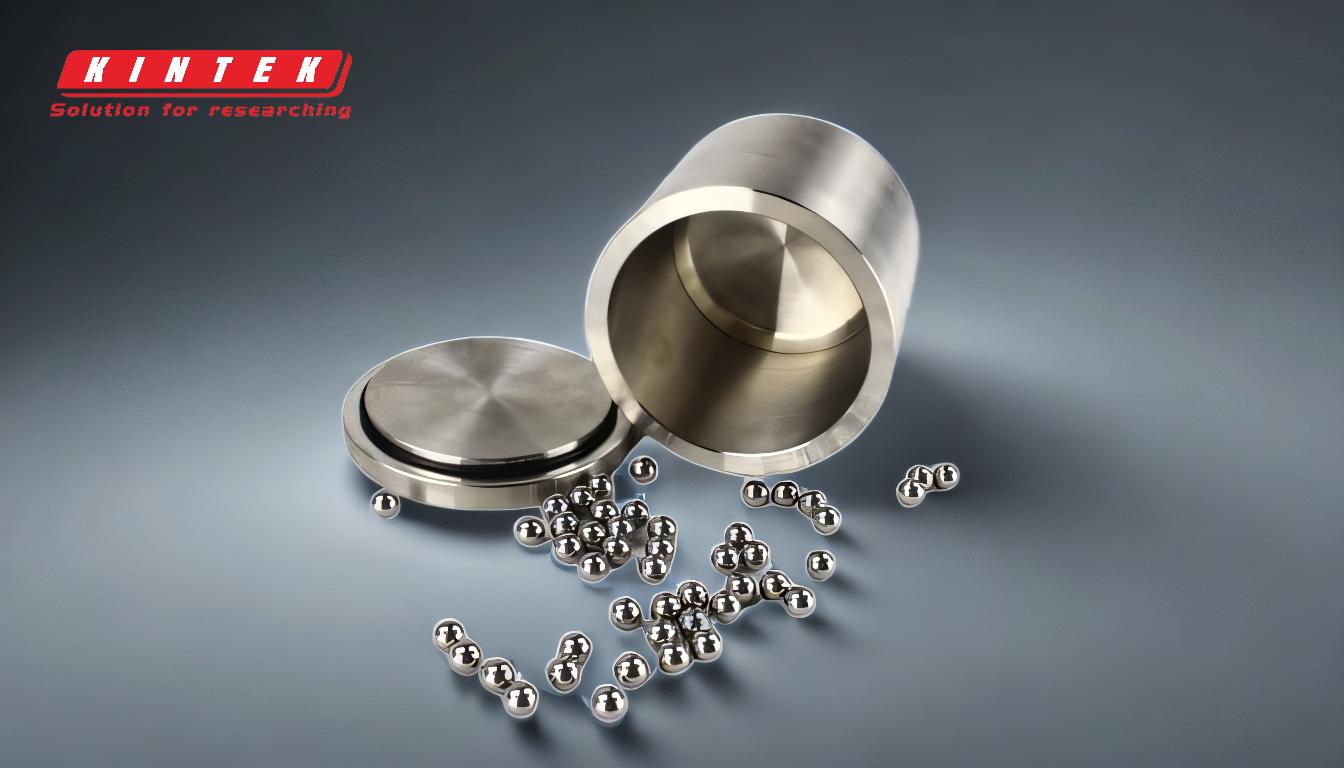
-
Sources of Contamination in Ball Milling:
- Milling Media: The balls used in the milling process can be a major source of contamination. Materials like steel, tungsten carbide, or ceramics can wear down during milling, introducing foreign particles into the sample.
- Milling Container: The container or vial in which the milling occurs can also contribute to contamination. For example, if the container is made of a material that is not chemically inert, it may react with the sample or wear down over time.
- Atmosphere: The environment inside the milling chamber can introduce contaminants, especially if the process is not conducted in an inert atmosphere. Oxygen, moisture, or other gases can react with the sample, leading to oxidation or other chemical changes.
- Starting Materials: Impurities in the raw materials being milled can also lead to contamination. These impurities may be present in the form of oxides, adsorbed gases, or other foreign substances.
-
Types of Contamination:
- Mechanical Contamination: This occurs when particles from the milling media or container are introduced into the sample. For example, steel balls can introduce iron contamination, while ceramic balls may introduce alumina or zirconia particles.
- Chemical Contamination: This type of contamination arises from chemical reactions between the sample and the milling environment. For instance, oxidation of the sample due to exposure to air or moisture can alter its chemical composition.
- Thermal Contamination: High-energy ball milling can generate significant heat, which may lead to thermal degradation of the sample or the milling media. This can result in the formation of unwanted phases or compounds.
-
Mechanisms of Contamination:
- Abrasion and Wear: The continuous impact and friction between the milling balls and the container can cause wear and tear, leading to the release of particles from the milling media or container into the sample.
- Chemical Reactions: The high-energy environment of ball milling can facilitate chemical reactions between the sample and the milling environment. For example, reactive metals may oxidize when exposed to air during milling.
- Adhesion and Transfer: Particles from the milling media or container can adhere to the sample and be transferred into it. This is particularly common when the milling media and sample have similar chemical compositions.
-
Strategies to Minimize Contamination:
- Selection of Milling Media: Choosing the right milling media is crucial. For example, using balls made of the same material as the sample can reduce mechanical contamination. Alternatively, using inert materials like zirconia or alumina can minimize chemical contamination.
- Inert Atmosphere: Conducting the milling process in an inert atmosphere, such as argon or nitrogen, can prevent oxidation and other chemical reactions. This is especially important for reactive materials like metals or alloys.
- Proper Container Material: Selecting a container material that is chemically inert and resistant to wear can help reduce contamination. For example, using containers made of hardened steel, tungsten carbide, or ceramics can minimize the risk of contamination.
- Regular Maintenance: Regularly inspecting and replacing worn-out milling media and containers can help maintain the integrity of the milling process and reduce contamination over time.
-
Impact of Contamination on Material Properties:
- Mechanical Properties: Contamination can affect the mechanical properties of the milled material, such as hardness, tensile strength, and ductility. For example, the introduction of hard particles from the milling media can increase the hardness of the material but may also reduce its ductility.
- Chemical Properties: Chemical contamination can alter the composition of the material, leading to changes in its chemical reactivity, corrosion resistance, or other properties. For instance, oxidation during milling can reduce the corrosion resistance of a metal.
- Thermal Properties: Contamination can also impact the thermal properties of the material, such as its thermal conductivity or melting point. The presence of foreign particles can create thermal barriers or alter the material's phase transition behavior.
-
Detection and Analysis of Contamination:
- Microscopy: Techniques like scanning electron microscopy (SEM) or transmission electron microscopy (TEM) can be used to detect and analyze contamination at the microscopic level. These techniques can reveal the presence of foreign particles and their distribution within the material.
- Spectroscopy: Methods like energy-dispersive X-ray spectroscopy (EDS) or X-ray photoelectron spectroscopy (XPS) can be employed to identify the chemical composition of contaminants. This is particularly useful for detecting chemical contamination.
- Thermal Analysis: Techniques like differential scanning calorimetry (DSC) or thermogravimetric analysis (TGA) can help assess the impact of contamination on the thermal properties of the material.
In conclusion, contamination during ball milling is a multifaceted issue that can arise from various sources and mechanisms. Understanding these factors and implementing strategies to minimize contamination is essential for producing high-quality milled materials with desired properties. By carefully selecting milling media, controlling the milling environment, and regularly maintaining equipment, it is possible to significantly reduce contamination and ensure the success of the ball milling process.
Summary Table:
Aspect | Details |
---|---|
Sources of Contamination | Milling media, container, atmosphere, starting materials |
Types of Contamination | Mechanical, chemical, thermal |
Mechanisms | Abrasion, chemical reactions, adhesion |
Minimization Strategies | Proper media selection, inert atmosphere, container material, maintenance |
Impact on Properties | Mechanical, chemical, thermal properties affected |
Detection Methods | Microscopy, spectroscopy, thermal analysis |
Ensure contamination-free ball milling for your materials—contact our experts today!